Jak podłączyć optymalizator do paneli fotowoltaicznych krok po kroku
Marzy Ci się maksymalna wydajność instalacji fotowoltaicznej bez względu na warunki, a może masz już panele i zastanawiasz się, co zrobić, aby wycisnąć z nich więcej? W tym kontekście często pojawia się pytanie: Jak podłączyć optymalizator do paneli fotowoltaicznych? Okazuje się, że proces ten, choć na pierwszy rzut oka może wydawać się technicznie wymagający, sprowadza się do podłączenia optymalizatora szeregowo pomiędzy panelem a falownikiem i jego konfiguracji, pozwalając panelom działać niezależnie i maksymalizując produkcję energii nawet przy częściowym zacienieniu.
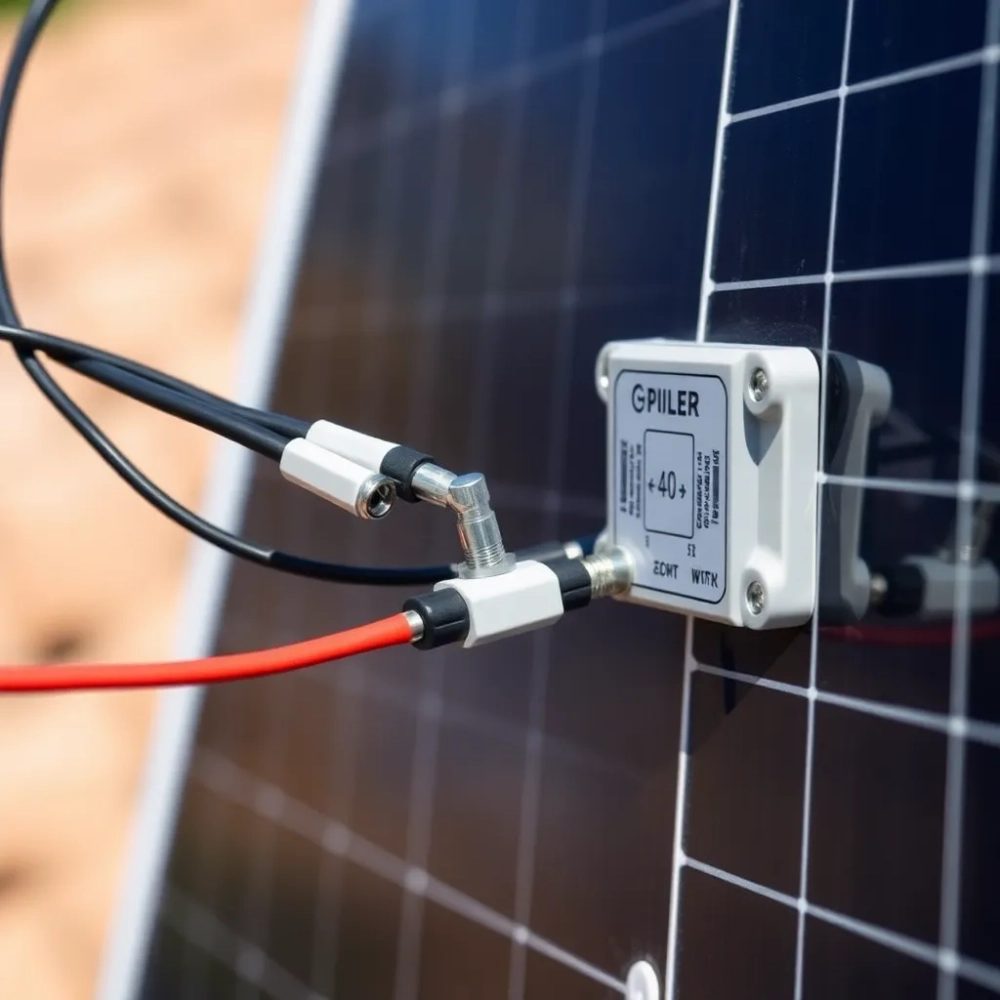
Scenariusz Zacienienia | Typowa Instalacja Szeregowa (Bez Optymalizatorów) Średni Spadek Wydajności (%) |
Instalacja z Optymalizatorami Mocy Średni Spadek Wydajności (%) |
Szacunkowy Wzrost Produkcji Rocznej (%) Dzięki Optymalizatorom |
---|---|---|---|
Brak znaczącego zacienienia | 0-2% | 0-1% | 0-1% |
Okresowe zacienienie (<2 godz./dzień, 1-2 moduły) | 10-15% | 2-4% | 6-13% |
Umiarkowane zacienienie (2-4 godz./dzień, 3-5 modułów) | 20-30% | 4-7% | 13-26% |
Intensywne/Stałe zacienienie (>4 godz./dzień, >5 modułów LUB różne orientacje/nachylenia) | 30-50% | 7-15% | 15-43% |
Co ciekawe, optymalizatory to nie tylko ratunek przed cieniem; stają się niemalże obowiązkowym elementem w bardziej złożonych systemach. Gdy panele ułożone są na różnych połaciach dachu o różnych kątach nachylenia, albo gdy liczba modułów w szeregu jest wyjątkowo duża – ponad dziesięć, piętnaście czy dwadzieścia – to właśnie wtedy optymalizatory ujawniają pełnię swoich możliwości. Pomagają zapanować nad produkcją w nierównomiernych warunkach i zapewniają, że każdy panel pracuje na swoje sto procent. To często te nietypowe lub skomplikowane instalacje stanowią idealną przestrzeń, aby wykorzystać potencjał optymalizacji na poziomie modułu do maksimum. W takiej sytuacji inwestycja w dodatkowy element systemu wydaje się nie tylko zasadna, ale wręcz konieczna do osiągnięcia optymalnych wyników.
Ważne zasady bezpieczeństwa przy podłączaniu optymalizatorów
Podłączanie jakichkolwiek elementów instalacji elektrycznej, zwłaszcza wysokiego napięcia prądu stałego, jakim operują panele fotowoltaiczne, wymaga bezwzględnego przestrzegania zasad bezpieczeństwa. Zignorowanie tych protokołów to prosta droga do wypadku – porażenia prądem, pożaru, czy poważnego uszkodzenia sprzętu, a tego chyba nikt z nas nie chce doświadczyć, prawda? Praca z fotowoltaiką na dachu dodatkowo podnosi stawkę, dodając ryzyko upadku z wysokości. Zanim chwycimy za narzędzia, kluczowe jest uświadomienie sobie, że stoimy przed systemem, który potrafi wygenerować niebezpieczne napięcie nawet przy niewielkim oświetleniu. Podstawą jest całkowite odłączenie instalacji od zasilania – dotyczy to zarówno strony prądu zmiennego (wyłączenie głównego wyłącznika AC, wyłącznika pożarowego, jeśli występuje), jak i odłączenia strony prądu stałego od inwertera. Wiele nowoczesnych inwerterów posiada wbudowany rozłącznik DC, który należy bezwzględnie wykorzystać. Pamiętajmy jednak, że odłączenie od inwertera nie eliminuje napięcia w stringach paneli wystawionych na słońce; optymalizatory, w zależności od modelu i producenta, mogą posiadać funkcje bezpiecznego wyłączania na poziomie modułu, ale zawsze trzeba traktować kable wychodzące z panelu jako potencjalnie pod napięciem, dopóki nie zostaną podłączone do "bezpiecznego" systemu zarządzanego przez inwerter. Niezbędne jest posiadanie odpowiedniego, certyfikowanego sprzętu ochronnego. To nie tylko oczywistości takie jak kask ochronny na dachu i uprząż asekuracyjna, ale przede wszystkim rękawice elektroizolacyjne, dostosowane do napięć operujących w instalacji PV (często do 1000V lub 1500V DC). Podobnie, narzędzia – klucze, ściągacze izolacji, zaciskarki – powinny być izolowane i przeznaczone do prac pod napięciem. Często zdarza się, że w pośpiechu sięgamy po "zwykłe" narzędzia, a to błąd, który może mieć katastrofalne skutki. Wiedza i ostrożność są równie ważne co fizyczne zabezpieczenia. Praca w sprzyjających warunkach atmosferycznych to kolejna, często bagatelizowana zasada. Instalowanie optymalizatorów na mokrym lub śliskim dachu to proszenie się o kłopoty z wielu powodów, nie tylko elektrycznych. Porażenie prądem w takich warunkach potęguje ryzyko upadku. Burza, deszcz, silny wiatr – to czynniki, które bezwzględnie powinny przerwać prace instalacyjne. Słońce owszem, sprzyja produkcji energii po uruchomieniu systemu, ale podczas samej instalacji zwiększa napięcie w modułach i nagrzewa powierzchnię dachu i samego panelu, co może być uciążliwe i niebezpieczne. Instrukcja producenta optymalizatora jest Twoim Pismem Świętym w tym procesie. Każdy producent – SolarEdge, Tigo czy inny – ma swoje specyficzne zalecenia dotyczące montażu, okablowania i uruchomienia. Zignorowanie kroków opisanych w dokumentacji to proszenie się o problemy techniczne, utratę gwarancji, a co gorsza, zagrożenie bezpieczeństwa. Znajomość specyfikacji technicznych – maksymalnego napięcia wejściowego, prądu – optymalizatora i panela jest absolutnie niezbędna. Zamocowanie optymalizatora do ramy panelu powinno odbywać się przy użyciu dedykowanych uchwytów lub śrub, zgodnie z zaleceniami. Zapewnia to stabilność mechaniczną i zapobiega uszkodzeniom spowodowanym np. wiatrem. Okablowanie, a zwłaszcza złącza MC4, wymagają precyzji. Nieprawidłowo zaciśnięte lub uszkodzone złącze to potencjalne miejsce łuku elektrycznego – niebezpiecznego zjawiska mogącego prowadzić do pożaru. To jeden z tych momentów, kiedy dokładność jest ważniejsza niż pośpiech; lepiej poświęcić dodatkowe pięć minut na sprawdzenie połączenia niż później martwić się skutkami. Systemy z optymalizatorami, szczególnie te bazujące na protokołach komunikacyjnych, mogą wymagać specyficznej procedury wyłączania awaryjnego lub "bezpiecznego napięcia". Niektóre rozwiązania obniżają napięcie na poziomie modułu do zera lub do bardzo niskiej, bezpiecznej wartości, gdy tylko inwerter lub system monitoringu zostaną wyłączone. Należy dokładnie zapoznać się z tą funkcjonalnością systemu, aby w sytuacji awaryjnej wiedzieć, jak bezpiecznie rozłączyć instalację. To wiedza, która w krytycznym momencie może uratować życie lub mienie. Przy pracach na dachu, zawsze zaleca się pracować co najmniej w dwie osoby. W razie wypadku – poślizgnięcia, upadku narzędzia, zasłabnięcia – druga osoba może szybko zareagować i udzielić pomocy lub wezwać wsparcie. Komunikacja i wzajemne pilnowanie się to elementarna, a zarazem niezwykle skuteczna zasada bezpieczeństwa. Pamiętajmy, że brawura na wysokości nie popłaca. Dbając o te wszystkie aspekty, nie tylko zapewniamy sobie bezpieczeństwo, ale też profesjonalizm i pewność, że wykonujemy pracę solidnie, minimalizując ryzyko problemów w przyszłości. W naszej pracy widzieliśmy, jak drobne zaniedbanie podstawowych zasad bezpieczeństwa prowadziło do poważnych sytuacji – od stopionych złącz po niestety, wypadki z udziałem ludzi. Zawsze warto potraktować bezpieczeństwo priorytetowo.Synchronizacja optymalizatora z inwerterem
Synchronizacja, a właściwie "parowanie" lub "mapowanie" optymalizatorów z inwerterem, to krytyczny etap instalacji, który pozwala systemowi działać jako spójna całość. To moment, w którym każdy indywidualny opiekun modułu zgłasza swoją obecność "mózgowi" systemu – falownikowi – i zaczyna z nim cyfrowo współpracować. Bez tej cyfrowej ceremonii, optymalizatory pozostaną co prawda podłączone elektrycznie, ale system monitoringu nie zobaczy każdego modułu osobno, a w niektórych systemach same optymalizatory mogą nie w pełni realizować swoje zadania optymalizacji mocy, a nawet blokować przepływ energii. To jak posiadanie zespołu znakomitych muzyków, którzy nie wiedzą, do którego dyrygenta mają się zgłosić. Proces synchronizacji różni się w zależności od producenta sprzętu, ale ogólna zasada opiera się na tym, że inwerter musi "odkryć" optymalizatory podłączone w szeregu w danym stringu. W wielu systemach, zwłaszcza tych zoptymalizowanych na poziomie modułu przez jednego producenta (np. systemy, gdzie zarówno optymalizator, jak i inwerter pochodzą od tej samej firmy), synchronizacja rozpoczyna się automatycznie lub półautomatycznie po pierwszym uruchomieniu inwertera. Inwerter wysyła sygnały do podłączonych modułów, a optymalizatory odpowiadają, identyfikując się. Często w tym procesie kluczową rolę odgrywają numery seryjne optymalizatorów, które są skanowane przez instalatora podczas montażu i wprowadzane do systemu monitoringu lub aplikacji instalatorskiej. Mapowanie fizycznej lokalizacji optymalizatora (czyli panela) z jego numerem seryjnym w systemie monitoringowym jest niezwykle ważne dla późniejszej diagnozy problemów. Dzięki temu, widząc w aplikacji, że moduł o numerze seryjnym ABC-123 na pozycji D1 (dach wschód, pierwszy rząd, moduł pierwszy) działa nieprawidłowo, dokładnie wiemy, który panel wymaga interwencji. To znacząco skraca czas serwisowania i pozwala na szybkie zlokalizowanie problemu, np. zabrudzenia, uszkodzenia czy problemu z samym optymalizatorem. Bez tego, szukanie winowajcy na dachu w dużej instalacji byłoby jak szukanie igły w stogu siana. Widzieliśmy przypadki, gdzie brak starannego mapowania podczas instalacji kończył się frustrującymi i czasochłonnymi wizytami serwisowymi. Część systemów wymaga zainicjowania procesu synchronizacji za pomocą dedykowanego oprogramowania lub aplikacji mobilnej na smartfonie lub tablecie. Instalator łączy się z inwerterem (często przez Wi-Fi lub Ethernet), a następnie uruchamia funkcję wyszukiwania optymalizatorów. Inwerter "rozmawia" z każdym optymalizatorem w stringu, identyfikując go i potwierdzając komunikację. Ten etap bywa czasem nazywany "treningiem" stringów. Pomyśl o tym jak o nowym nauczycielu poznającym swoich uczniów – musi każdego zobaczyć, usłyszeć jego nazwisko i upewnić się, że jest na liście obecności. W systemach, gdzie optymalizatory i inwerter pochodzą od różnych producentów (mniej powszechne, ale możliwe dzięki standaryzacji np. protokołu komunikacji), proces synchronizacji może być bardziej złożony i wymagać specjalnych procedur opisanych w dokumentacji obu urządzeń. Kluczowe jest, aby upewnić się, że inwerter jest kompatybilny z danym modelem optymalizatora i potrafi z nim poprawnie się komunikować. To trochę jak próba sparowania słuchawek Bluetooth innej marki z telefonem – czasem działa od razu, czasem wymaga ręcznego wyszukiwania, a czasem wcale nie są kompatybilne. Problemy z synchronizacją mogą wynikać z kilku przyczyn: niepoprawnego podłączenia elektrycznego (np. zamieniona polaryzacja, luźne złącze), uszkodzenia optymalizatora, problemów z okablowaniem komunikacyjnym (jeśli system go wymaga), czy błędów w oprogramowaniu inwertera lub aplikacji. W takich sytuacjach, inwerter zazwyczaj wyświetla komunikat błędu, wskazując, że nie widzi jednego lub więcej optymalizatorów w danym stringu. Działania naprawcze często polegają na weryfikacji połączeń fizycznych, sprawdzeniu poprawności skanowania numerów seryjnych i ponowieniu procedury synchronizacji. Pamiętaj, że nawet jeden nieprawidłowo wykryty optymalizator może wpływać na działanie całego stringu, a w skrajnych przypadkach nawet całej instalacji. Synchronizacja jest nie tylko technologicznym krokiem, ale też swoistą obietnicą – obietnicą, że system będzie działał inteligentnie, maksymalizując uzysk z każdego centymetra kwadratowego panelu i dostarczając szczegółowe dane o jego pracy. Dopiero po udanej synchronizacji system zaczyna działać w pełni zgodnie z zamierzeniem, oferując korzyści płynące z optymalizacji na poziomie modułu. To ten cyfrowy "uścisk dłoni" między optymalizatorem a inwerterem otwiera drzwi do efektywniejszej przyszłości energetycznej dla Twojego dachu.Konfiguracja optymalizatora i systemu monitoringu
Konfiguracja optymalizatora i towarzyszącego mu systemu monitoringu to nieodłączny etap po pomyślnym fizycznym podłączeniu i synchronizacji urządzeń. To właśnie tutaj "nadajemy im sens", ustawiając parametry pracy i co ważniejsze, otwierając okno na wgląd w ich codzienną "ciężką pracę" na dachu. Prawidłowa konfiguracja to fundament nie tylko dla optymalnej wydajności, ale także dla możliwości szybkiego diagnozowania i rozwiązywania potencjalnych problemów w przyszłości. Zaniedbanie tego etapu jest jak zakup zaawansowanego samochodu sportowego i nigdy niezaglądanie pod maskę czy na deskę rozdzielczą – owszem, pojedzie, ale czy wykorzystasz jego pełny potencjał i czy w porę zauważysz, gdy coś będzie nie tak? Proces konfiguracji zazwyczaj odbywa się poprzez dedykowaną aplikację mobilną instalatora lub portal internetowy udostępniony przez producenta systemu. Po połączeniu się z inwerterem lub bramką komunikacyjną, instalator uzyskuje dostęp do interfejsu konfiguracyjnego. Tutaj wprowadza kluczowe dane, które zostały wcześniej przygotowane – przede wszystkim numery seryjne zainstalowanych optymalizatorów i ich przyporządkowanie do konkretnych lokalizacji na dachu (to słynne "mapowanie" paneli). Pamiętacie naszą opowieść o szukaniu problematycznego panelu? To właśnie w tym kroku budujemy tę wirtualną mapę instalacji, która później pozwoli nam precyzyjnie namierzyć moduł D1, o którym wspominaliśmy wcześniej. W zależności od producenta, na etapie konfiguracji można również ustawić pewne parametry pracy systemu, choć optymalizatory same w sobie często działają w trybie plug-and-play, automatycznie adaptując się do warunków pracy panela i inwertera. Niemniej jednak, to właśnie na tym etapie aktywuje się zaawansowane funkcje, takie jak wspomniane wcześniej bezpieczne wyłączanie na poziomie modułu czy szczegółowe raportowanie danych. System monitoringu wymaga utworzenia konta dla użytkownika końcowego – Ciebie. To Ty, jako właściciel instalacji, będziesz miał dostęp do danych o produkcji energii, wydajności poszczególnych modułów i ewentualnych alertów. Założenie i skonfigurowanie konta monitoringowego jest zazwyczaj procesem intuicyjnym, prowadzonym krok po kroku. Wprowadzasz podstawowe informacje o lokalizacji instalacji (adres, współrzędne geograficzne, które wpływają na algorytmy śledzenia słońca w zaawansowanych systemach), jej mocy (sumaryczna moc modułów), datę uruchomienia. System monitoringu staje się Twoim centrum dowodzenia. To tam będziesz mógł na co dzień obserwować, jak system radzi sobie z produkcją energii, porównywać dzisiejszy uzysk z wczorajszym, sprawdzać, czy zacienienie wpływa na któryś moduł mocniej niż na inne. Dane prezentowane w systemie monitoringu są prawdziwym skarbem. Możliwość wglądu w produkcję każdego panelu osobno pozwala na natychmiastowe zidentyfikowanie problemów. Moduł, który produkuje znacznie mniej niż sąsiednie panele w tych samych warunkach oświetleniowych, natychmiast rzuca się w oczy. Może to być znak, że coś jest nie tak – brud na panelu (np. ptasia odchodnia, o zgrozo, to częstszy problem niż się wydaje!), uszkodzenie ogniwa, problem z samym optymalizatorem, czy po prostu coś rzucającego na niego nieoczekiwany cień. W tradycyjnym systemie bez optymalizatorów i monitoringu na poziomie modułu, widziałbyś jedynie spadek produkcji całego stringu lub całej instalacji, a ustalenie przyczyny byłoby znacznie trudniejsze i czasochłonne. System monitoringu często oferuje również funkcje raportowania, pozwalające na analizę wydajności w dłuższym okresie – dzienną, miesięczną, roczną. Możesz porównywać rzeczywisty uzysk z przewidywaniami (bazującymi na mocy instalacji, lokalizacji i historycznych danych pogodowych). To pozwala ocenić, czy instalacja działa zgodnie z oczekiwaniami i czy inwestycja przynosi zakładane korzyści. W niektórych systemach możliwe jest nawet ustawienie alertów – np. powiadomienie e-mail lub push na telefon, gdy produkcja spadnie poniżej określonego poziomu lub gdy wykryty zostanie błąd w komunikacji z urządzeniem. Poprawna konfiguracja systemu monitoringu to także zapewnienie stabilnego połączenia z internetem (przez sieć LAN lub Wi-Fi) oraz weryfikacja, czy dane są regularnie przesyłane do chmury producenta. Bez tego, Twoje okno na instalację pozostanie zamknięte. Czasem wymagane jest przekierowanie portów na routerze lub dostosowanie ustawień sieciowych, co może być drobną przeszkodą, ale jest niezbędne do pełnej funkcjonalności systemu. Pamiętajmy, że monitorowanie to nie tylko komfort psychiczny, ale realne narzędzie do zarządzania i optymalizacji instalacji w czasie.Weryfikacja poprawności podłączenia i działania systemu
Po zakończeniu fizycznego montażu, podłączenia okablowania i przeprowadzeniu procesu synchronizacji oraz wstępnej konfiguracji, następuje moment prawdy: weryfikacja poprawności całego systemu. To jak uruchomienie silnika po remoncie – wszystko wygląda dobrze na papierze, ale prawdziwy test odbywa się w praktyce. Ten etap jest absolutnie kluczowy i nie powinien być w żaden sposób pomijany czy przyspieszany, gdyż może ujawnić potencjalne błędy instalacyjne, które mogłyby prowadzić do nieefektywnej pracy systemu, a w skrajnych przypadkach nawet do zagrożeń bezpieczeństwa. My, jako zespół z wieloletnim doświadczeniem, zawsze kładziemy na ten punkt szczególny nacisk – lepiej poświęcić dodatkową godzinę na dokładne sprawdzenie wszystkiego, niż wracać na dach z interwencją serwisową, która kosztuje czas i pieniądze. Pierwszym etapem weryfikacji są pomiary elektryczne. Dotyczą one strony prądu stałego (DC) i prądu zmiennego (AC). Na stronie DC, przy odłączonym inwerterze (pamiętajmy o bezpieczeństwie!), można zmierzyć napięcie poszczególnych stringów. Systemy z optymalizatorami charakteryzują się specyficznymi napięciami "bezpiecznymi" na wyjściu ze stringu, gdy inwerter jest wyłączony. W zależności od producenta optymalizatorów, może to być niskie napięcie (np. 1V na optymalizator), albo suma napięć, gdy moduły są oświetlone. Należy porównać zmierzone wartości z danymi w dokumentacji technicznej inwertera i optymalizatorów. Pomiary napięcia i prądu zwarcia każdego stringu podłączonego do inwertera (po jego uruchomieniu i ustabilizowaniu pracy) pozwalają potwierdzić, że połączenia są prawidłowe i żaden string nie ma anomalii. Pomiary rezystancji izolacji po stronie DC to również kluczowy test bezpieczeństwa, który pozwala wykryć potencjalne zwarcia doziemne spowodowane np. uszkodzoną izolacją kabla lub problemem z samymi urządzeniami. Weryfikacja polaryzacji kabli DC jest kolejnym, często niedocenianym, ale niezwykle ważnym krokiem. Zamienienie plusa z minusem na wejściu inwertera (o zgrozo, zdarza się najlepszym!) może prowadzić do poważnego uszkodzenia sprzętu. Przed podłączeniem kabli do inwertera, zawsze należy sprawdzić ich polaryzację odpowiednim miernikiem. Wizualna inspekcja to uzupełnienie pomiarów. Sprawdzenie wszystkich połączeń MC4, upewnienie się, że są solidnie zaciśnięte i prawidłowo wpięte, obejrzenie kabli pod kątem ewentualnych uszkodzeń mechanicznych, prawidłowego ułożenia kabli pod modułami i wzdłuż konstrukcji montażowej (zabezpieczonych przed przetarciem, z dala od ostrych krawędzi, spiętych opaskami), a także weryfikacja poprawnego zamocowania samych optymalizatorów na ramach modułów. Często proste rzeczy, jak źle zapięta opaska kablowa, mogą w przyszłości narobić problemów. Następnie przychodzi moment uruchomienia inwertera i całego systemu. Obserwacja zachowania inwertera podczas startu – czy przechodzi kolejne etapy autodiagnostyki, czy poprawnie wykrywa stringi, czy nawiązuje komunikację z siecią – daje pierwsze sygnały o stanie systemu. W inwerterach współpracujących z optymalizatorami, kluczowe jest sprawdzenie, czy wszystkie optymalizatory zostały poprawnie wykryte i zgłaszają status "online" w interfejsie inwertera lub w aplikacji monitorującej. Jeśli któryś optymalizator nie jest widoczny, wracamy do punktu startowego: weryfikacja fizycznego podłączenia i procesu synchronizacji dla danego stringu lub modułu. Pamiętam sytuację, gdzie winnym okazał się źle wpięty kabel komunikacyjny (cienki, dwużyłowy przewód odpowiedzialny za "rozmowę" optymalizatora z inwerterem w pewnym systemie); choć napięcie płynęło, komunikacja cyfrowa była zerowa, co uniemożliwiało prawidłowe działanie optymalizacji. Weryfikacja działania systemu monitoringu online to kolejny, niezbędny krok. Upewnij się, że dane z instalacji są przesyłane do portalu producenta i że masz do nich dostęp ze swojego konta użytkownika. Sprawdź, czy na wirtualnej mapie instalacji (jeśli system taką oferuje) widzisz wszystkie moduły i ich bieżącą produkcję. Nawet w pochmurny dzień powinieneś widzieć niewielką, ale proporcjonalną produkcję z każdego modułu. Różnice w produkcji między modułami powinny odzwierciedlać lokalne warunki – np. zacienienie od komina rzucające cień tylko na jeden moduł, które powinno być widoczne jako obniżona produkcja tego konkretnego modułu. W pierwszych dniach działania systemu warto częściej zaglądać do aplikacji monitoringowej, aby upewnić się, że wszystko pracuje stabilnie i zgodnie z oczekiwaniami. Porównanie danych rzeczywistej produkcji z prognozami (dostępnymi np. w aplikacjach pogodowych dla instalacji PV) daje dodatkową perspektywę na wydajność. Weryfikacja poprawności podłączenia i działania to proces wieloetapowy, wymagający uwagi na każdym kroku – od pomiarów elektrycznych, przez inspekcję wizualną, po kontrolę danych w systemie monitoringu. Tylko w ten sposób możesz mieć pewność, że Twoja instalacja fotowoltaiczna z optymalizatorami będzie działać bezpiecznie, efektywnie i bezawaryjnie przez wiele lat, przynosząc maksymalny możliwy uzysk energetyczny i finansowy. To inwestycja w spokój ducha i gwarancja, że każdy wat energii ze słońca zostanie przez Twój system skutecznie zagospodarowany.Porównanie Produkcji Energii: Scenariusz z Zacienieniem
Poniższy wykres ilustruje przykładowy wpływ zacienienia na produkcję energii z instalacji fotowoltaicznej w ciągu kilku godzin. Pokazuje różnicę między systemem tradycyjnym a systemem z optymalizatorami, gdzie poszczególne moduły pracują niezależnie.