Jak znalezc uszkodzony panel fotowoltaiczny
Czuć rozczarowanie, gdy Twoja inwestycja w słońce zaczyna kulać, prawda? Nagły spadek produkcji energii z paneli fotowoltaicznych potrafi zepsuć dzień i rachunek za prąd. Ale zanim złapiesz za telefon do instalatora, warto samemu wiedzieć, jak znaleźć uszkodzony panel fotowoltaiczny. Ten ukryty sabotażysta na dachu często zdradza się dopiero przy głębszej analizie, a wbrew pozorom, istnieją systematyczne metody jego zidentyfikowania: szukaj wizualnie, elektrycznie i termowizyjnie. To kluczowe podejścia w detekcji problemu, które pozwalają szybko namierzyć źródło kłopotów z wydajnością instalacji. Nasi specjaliści, analizując setki zgłoszeń i inspekcji na przestrzeni lat, zauważyli pewne powtarzające się wzorce uszkodzeń paneli fotowoltaicznych, które bezpośrednio wpływają na obniżenie wydajności instalacji elektrycznej. Wady ogniw lub uszkodzenia powstały w trakcie pracy, a jak wykryć uszkodzony panel fotowoltaiczny szybko, jest kluczowe, by nie dopuścić do pogłębienia się defektu. Zebraliśmy dane z rutynowych przeglądów, aby lepiej zrozumieć, z jakimi problemami mierzą się użytkownicy i jak często poszczególne defekty dają o sobie znać w działających instalacjach.Rodzaj uszkodzenia | Szacowana częstotliwość występowania* | Typowy objaw (kluczowy do znalezienia) |
---|---|---|
Mikropęknięcia ogniw | ~40% | Spadek mocy, często niewidoczne bez sprzętu lub lupy |
Gorące punkty (Hot spots) | ~25% | Przegrzewanie się obszarów ogniw, wykrywalne termowizją |
Delaminacja (Rozwarstwienie) | ~15% | Widoczne pęcherze, przebarwienia pod szkłem |
Dyskoloracja / PID (Degradacja Indukowanym Potencjałem) | ~10% | Widoczne przebarwienia ogniw, znaczny spadek mocy na poziomie całej instalacji |
Uszkodzenia ramy / Szkła | ~10% | Widoczne pęknięcia, zgięcia, ubytki fizyczne |
*Dane szacunkowe na podstawie analizy inspekcji systemów fotowoltaicznych w Polsce.
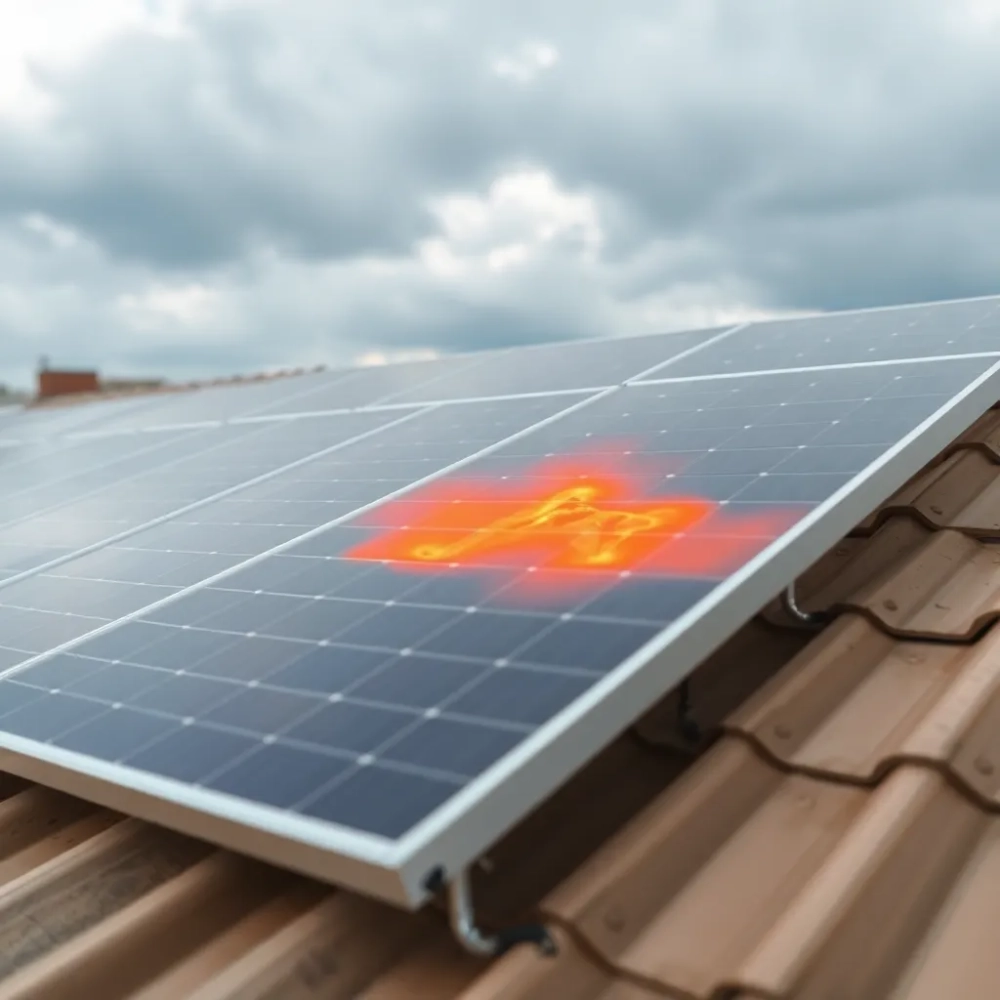
Najczęstsze rodzaje uszkodzeń i ich objawy
Panele fotowoltaiczne, choć wyglądają na solidne szklane tafle, składają się z wielu delikatnych warstw, które mogą ulec uszkodzeniu z różnych powodów. Od ekstremalnych warunków atmosferycznych, takich jak opady gradu czy silny wiatr, po problemy wynikające ze zwykłego zużycia lub zakupu modułów niższej jakości, zagrożenia są liczne.
Nieprawidłowy montaż instalacji fotowoltaicznej w nieodpowiednim miejscu jest niestety częstą przyczyną wad, która wpływa na prawidłowe działanie paneli. Uszkodzenia mechaniczne powstały w trakcie transportu, instalacji lub już po jej uruchomieniu, na przykład na skutek działania warunków pogodowych, często manifestują się jako pęknięcia.
Mikropęknięcia ogniw
Jednym z najczęstszych, a jednocześnie najbardziej zdradliwych problemów są mikropęknięcia ogniw krzemowych w panelach. Te niemal niewidoczne gołym okiem rysy powstały najczęściej w czasie transportu, nieprawidłowego przechowywania lub podczas montażu, np. gdy na panel nadepnięto, albo w wyniku naprężeń termicznych i obciążeń wiatrowo-śnieżnych w cyklu życia instalacji.
Chociaż na początku mogą być małe, mikropęknięcia mają tendencję do powiększania się z czasem pod wpływem pracy instalacji i warunków środowiskowych. Działają jak bariery dla swobodnego przepływu elektronów, redukując aktywną powierzchnię ogniwa. Powoduje to lokalny wzrost rezystancji i wydzielanie ciepła wzdłuż linii pęknięcia.
Konsekwencją mikropęknięć jest nie tylko stopniowy spadek wydajności uszkodzonego panelu, często trudny do zauważenia bez dokładnych pomiarów, ale także ryzyko powstania gorących punktów. Tam, gdzie prąd napotyka przeszkodę w pęknięciu, energia jest tracona w postaci ciepła, co może prowadzić do przegrzania i trwałego uszkodzenia ogniwa, a nawet zagrożenia pożarowego w skrajnych przypadkach.
Wykrycie mikropęknięć jest trudne bez specjalistycznego sprzętu; wizualna inspekcja gołym okiem rzadko coś zdradzi, chyba że pęknięcie jest duże i biegnie przez całe ogniwo. Najbardziej skuteczne metody to elektroluminescencja (EL) lub fotoluminescencja (PL), które obrazują przepływ prądu przez ogniwa i potrafią wskazać nawet najmniejsze przerwy, ale są to metody wymagające demontażu panelu i wykonania testów w laboratorium lub w specyficznych warunkach polowych.
Czasami obecność mikropęknięć zdradza się pośrednio podczas inspekcji termowizyjnej, jeśli powstały gorące punkty, lub w testach elektrycznych, gdy panel ma niższą moc niż oczekiwano. Dane z monitoringu systemu, wykazujące stopniowe obniżenie produkcji przez konkretny moduł, mogą być pierwszym sygnałem, że warto zbadać go pod kątem mikropęknięć.
Producenci paneli o wyższej jakości stosują grubsze szkło, wzmocnione ramy i bardziej zaawansowane procesy laminacji, które minimalizują ryzyko powstawania mikropęknięć podczas typowej eksploatacji i transportu. Inwestycja w panele renomowanych marek o potwierdzonej odporności mechanicznej może znacząco ograniczyć to ryzyko.
Gorące Punkty (Hot Spots)
Gorące punkty to kolejne poważne uszkodzenia paneli, często będące konsekwencją innych defektów, takich jak mikropęknięcia, uszkodzone obejścia prądowe (tzw. bypass diody) lub długotrwałe, częściowe zacienienie. Są to obszary ogniw, które zamiast produkować energię, zaczynają ją konsumować od sąsiednich ogniw w szeregu, działając jak obciążenie i wydzielając nadmierne ciepło.
Przyczyny powstawania gorących punktów są różnorodne. Partial shading, czyli częściowe zacienienie panelu przez liście, komin, antenę czy nawet brud, jest częstym winowajcą; jeśli zacienione ogniwo przestaje produkować, powinno zostać pominięte przez diodę bypass. Jeśli dioda bypass zawiedzie lub zacienienie jest nieregularne na obszarze grupy ogniw bez diody, powstaje hot spot.
Uszkodzone lub wadliwe diody bypass, które nie przewodzą prądu wstecznego poprawnie, mogą również powodować przegrzewanie się części panelu. Te diody są kluczowe w ochronie paneli przed efektami zacienienia, kierując prąd produkowany przez niezacienione części stringu wokół zablokowanych sekcji.
Gorące punkty są wyjątkowo niebezpieczne, ponieważ temperatura w uszkodzonym obszarze może gwałtownie wzrosnąć, znacznie przekraczając normalną temperaturę pracy panelu, dochodząc nawet do 80-100°C i więcej. Tak wysokie temperatury przyspieszają degradację materiałów panelu – laminatu (EVA), folii ochronnej (backsheet), a w skrajnych przypadkach mogą doprowadzić do stopienia materiałów, wypalenia otworu w panelu, a nawet samozapłonu.
Objawy gorących punktów nie zawsze są widoczne gołym okiem na wczesnym etapie, choć zaawansowane uszkodzenia mogą objawiać się jako wyraźne przebarwienia lub wręcz ślady spalenia na powierzchni ogniwa. Główną i najskuteczniejszą metodą ich wykrycia jest badanie termowizyjne paneli w trakcie pracy instalacji, w warunkach dobrego nasłonecznienia.
Kamera termowizyjna wskaże gorący punkt jako obszar o znacznie podwyższonej temperaturze w porównaniu do otoczenia i innych ogniw w tym samym panelu. Przyjmuje się, że różnica temperatury wynosząca 15-20°C lub więcej względem sąsiednich ogniw czy średniej temperatury panelu jest silnym sygnałem ostrzegawczym.
Delaminacja (Rozwarstwienie)
Delaminacja to proces rozwarstwiania się lub odklejania warstw, z których zbudowany jest panel fotowoltaiczny – najczęściej oddzielenie się szkła od laminatu EVA, lub laminatu od folii tylnej (backsheet). Zdarza się najczęściej w przypadku paneli słabej jakości, gdzie proces laminacji nie był przeprowadzony poprawnie lub użyto materiałów o niskiej trwałości.
Główną przyczyną delaminacji jest przenikanie wilgoci do wnętrza panelu, często przez uszkodzone uszczelnienia, nieszczelności w ramie lub mikropęknięcia w szkle czy folii tylnej. Cykliczne zmiany temperatury powodują rozszerzanie i kurczenie się materiałów, co dodatkowo potęguje problem, "zasysając" wilgoć do środka.
Objawy delaminacji są zazwyczaj widoczne gołym okiem: pęcherze powietrza, "mleczne" lub zmętniałe obszary pod szkłem, zwłaszcza wzdłuż krawędzi lub w rogach panelu. Prowadzi do powstawania kolejnych defektów, na przykład szybkiego korodowania wewnętrznych połączeń lub ścieżek przewodzących.
Delaminacja nie tylko wpływa na estetykę panelu, ale przede wszystkim ma poważne konsekwencje dla jego działania. Zmniejsza ilość światła docierającego do ogniw w zmętniałych obszarach, co prowadzi do spadku produkcji energii. Co gorsza, obecność wilgoci wewnątrz panelu stwarza ryzyko zwarć, korozji połączeń między ogniwami, a nawet problemów z bezpieczeństwem elektrycznym instalacji (np. obniżenie rezystancji izolacji).
Wykrycie delaminacji jest stosunkowo łatwe podczas inspekcji wizualnej z bliska. Ważne jest, aby dokładnie obejrzeć całą powierzchnię panelu, zwracając uwagę na wszelkie nietypowe zmętnienia, pęcherze, odklejające się brzegi czy zmiany koloru, które sugerują penetrację wilgoci. Zmianą koloru na środku ogniwa, choć na brzegach odcień pozostaje bez zmian, też może być objawem.
Choć niewielkie delaminacje mogą nie prowadzić od razu do drastycznego spadku mocy, są sygnałem ostrzegawczym i prekursorem poważniejszych problemów. Panel z zaawansowaną delaminacją wymaga zazwyczaj wymiany ze względów bezpieczeństwa i wydajności. Aby tego uniknąć, stawiając na panele fotowoltaiczne dobrej jakości od renomowanych producentów z długą gwarancją produktową, minimalizujemy ryzyko wystąpienia tej wady.
Degradacja Indukowanym Potencjałem (PID) i inne przebarwienia
Degradacja Indukowanym Potencjałem (PID) to zjawisko, które może wystąpić w niektórych typach paneli fotowoltaicznych, szczególnie w systemach o wysokim napięciu, działających w warunkach wysokiej temperatury i wilgotności. Jest to elektrochemiczny proces zachodzący w materiałach panelu pod wpływem różnicy potencjałów między ogniwem krzemowym a uziemioną ramą panelu.
PID powoduje migrację jonów w materiałach enkapsulujących (np. EVA) lub na granicy szkła i ogniw, co skutkuje obniżeniem wydajności ogniw, spadkiem ich rezystancji bocznikowej i często pojawieniem się charakterystycznych, widocznych gołym okiem wzorów przebarwień na powierzchni ogniw – przypominających "linie papilarne" lub nieregularne plamy. Panel dotknięty PIDem produkuje znacznie mniej energii, czasem tracąc kilkadziesiąt procent swojej nominalnej mocy.
Niektóre nowoczesne technologie ogniw (PERC, Half-Cut) są bardziej odporne na PID, a producenci stosują specjalne metody laminacji, doboru materiałów enkapsulujących oraz odpowiednie strategie uziemienia systemów (np. uziemienie bieguna ujemnego falownika), aby zminimalizować lub wyeliminować to ryzyko. Mimo to, PID nadal bywa problemem w starszych instalacjach lub modułach niższej jakości.
Objawy PIDu to przede wszystkim znaczny, często jednolity spadek mocy w całej grupie paneli w tym samym stringu, na który wpływ ma wysokie napięcie systemowe. Wizualnie można zaobserwować subtelne, siateczkowate przebarwienia na powierzchni ogniw, które mogą być bardziej widoczne po zmierzchu. Te zmiany koloru na środku ogniwa, choć na brzegach odcień pozostaje bez zmian, są wskazówką.
Diagnostyka PIDu polega na pomiarach mocy paneli (najlepiej z użyciem testera I-V curve tracera) oraz na ocenie wizualnej. Tester wskaże nietypowe krzywe charakterystyki (często z obniżoną rezystancją bocznikową). W skrajnych przypadkach można przeprowadzić laboratoryjne testy przyspieszonego starzenia w celu potwierdzenia podatności na PID.
Oprócz PIDu, panele mogą ulec innym typom przebarwień. Snail trails (ślady ślimaka) to brązowe, cienkie linie pojawiające się na powierzchni ogniw, przypominające ślady po ślimaku. Są one wynikiem reakcji chemicznej między wilgocią, tlenem i pastą metaliczną wewnątrz ogniwa, często zapoczątkowaną przez mikropęknięcia lub nieszczelności. Choć początkowo mogą być tylko kosmetyczne, wskazują na penetrację wilgoci i ryzyko dalszych problemów.
Żółknięcie laminatu EVA (enkapsulantu) to kolejna forma przebarwienia, która może wystąpić w starszych lub niższej jakości panelach pod wpływem promieniowania UV i temperatury. Żółty kolor redukuje ilość światła docierającego do ogniw, prowadząc do spadku mocy. Wybór paneli z enkapsulantem o potwierdzonej odporności na UV jest kluczowy w zapobieganiu temu zjawisku.
Problemy z Puszkami Przyłączeniowymi (Junction Box) i Kablami
Puszka przyłączeniowa na odwrocie panelu fotowoltaicznego jest jego "mózgiem elektrycznym", zawierającym zaciski do połączeń kablowych oraz diody bypass. Uszkodzenia w tej części panelu mogą prowadzić do całkowitego jego wyłączenia z pracy, problemów w całym stringu, a nawet zagrożenia pożarowego.
Najczęstsze problemy to uszkodzenie samych diod bypass (zwarcie lub rozwarcie), które przegrzewają się, topiąc obudowę puszki. Winne mogą być wady produkcyjne diod, przegrzanie spowodowane hot spotami w ogniwach, które dioda powinna obejść, lub przepięcia.
Inne problemy to luźne lub skorodowane połączenia wewnątrz puszki lub w samych złączach kablowych (np. MC4). Może to być efekt nieprawidłowego zaciśnięcia złączy podczas montażu, niskiej jakości samych złączy lub penetracji wilgoci prowadzącej do korozji. Luźne połączenie oznacza zwiększoną rezystancję i wydzielanie ciepła – często prowadzi do przegrzewania i stopienia plastiku złączy lub puszki.
Kable DC łączące panele w stringi również są narażone na uszkodzenia. Promieniowanie UV, skrajne temperatury, uszkodzenia mechaniczne (np. przetarcia o ostre krawędzie, uszkodzenia przez zwierzęta – wiewiórki czy kuny potrafią pogryźć izolację) lub błędy w układaniu kabli (np. tworzenie pętli indukcyjnych, kontakt z gorącą powierzchnią dachu) mogą prowadzić do zwarć, przerw w obwodzie lub obniżenia rezystancji izolacji.
Objawy uszkodzeń puszki lub kabli mogą być bardzo zróżnicowane: od całkowitego braku produkcji przez panel lub cały string, poprzez okresowe zaniki mocy, aż do widocznych śladów przegrzania, stopienia plastiku puszki lub złączy (często wykrywalne badaniem termowizyjnym), czy nawet wyzwolenie zabezpieczeń w falowniku lub rozłączniku DC (w przypadku zwarcia do masy).
Inspekcja wizualna puszki i kabli jest kluczowa: należy sprawdzić, czy obudowa puszki nie jest pęknięta, odkształcona, czy nie widać śladów przegrzania lub zapachu spalonego plastiku. Należy obejrzeć kable na całej długości, szukając uszkodzeń izolacji, przetarć. Termowizja jest niezwykle użyteczna do wykrywania przegrzewających się złączy lub diod w puszce.
Testy elektryczne, takie jak pomiar napięcia na złączach panelu lub stringu, pomiar prądu zwarcia (Isc), a zwłaszcza pomiar rezystancji izolacji między przewodami a ramą panelu lub konstrukcją, mogą wskazać na problemy z puszką, diodami lub kablami. Niska rezystancja izolacji często oznacza uszkodzoną izolację kabla lub penetrację wilgoci do puszki.
Bezpieczeństwo jest priorytetem: Praca przy puszkach przyłączeniowych i kablach DC wymaga zachowania szczególnej ostrożności ze względu na wysokie napięcia stałe, które mogą być śmiertelne. Zawsze należy odłączyć system po stronie AC i DC przed przystąpieniem do pracy i upewnić się miernikiem, że napięcie zanikło.
Uszkodzenia Ramy i Szkła
Choć rama panelu i szkło wydają się być bardzo wytrzymałe, one również mogą ulec uszkodzeniom, które wpływają na działanie, bezpieczeństwo i trwałość modułu. Szkło chroni ogniwa i laminat przed czynnikami zewnętrznymi, a rama zapewnia sztywność konstrukcji i ułatwia montaż.
Pęknięcia szyby panelu mogą być wynikiem uderzenia (grad, spadające przedmioty, ptaki, kamienie), transportu lub montażu, lub ekstremalnych naprężeń termicznych lub mechanicznych (np. zbyt mocne dokręcenie klem montażowych w niewłaściwym miejscu). Nawet małe pęknięcie w szkle może prowadzić do przenikania wilgoci do środka panelu, rozpoczynając proces delaminacji i korozji.
Uszkodzenia ramy, takie jak zgięcia, wgniecenia czy skorodowanie, najczęściej wynikają z niewłaściwego transportu, montażu (np. upadek panela), silnego wiatru lub błędu w konstrukcji montażowej. Zgięta rama może wywierać dodatkowe naprężenia na szybę i ogniwa, zwiększając ryzyko mikropęknięć, a korozja ramy może osłabiać całą konstrukcję.
Inspekcja wizualna jest podstawową metodą wykrycia tych uszkodzeń. Należy dokładnie obejrzeć powierzchnię szkła pod różnymi kątami, szukając pęknięć (nawet włoskowatych) i zarysowań, które wydają się wnikać głębiej. Obejrzeć ramę, szukając zniekształceń, wgnieceń, śladów korozji, zwłaszcza w miejscach styku z klemami montażowymi.
Ubytki w uszczelkach między szybą a ramą również są ważnym elementem do sprawdzenia wizualnie. Stanowią one pierwszą barierę dla wilgoci. Jeśli uszczelka jest sparciała, pęknięta lub odklejona, panel jest narażony na delaminację.
Panel z uszkodzoną szybą powinien być jak najszybciej zabezpieczony, a następnie wymieniony. Próby zaklejenia pęknięcia w szkle rzadko są trwałym rozwiązaniem i nie zapobiegają przenikaniu wilgoci w stu procentach. Złamana lub poważnie zgięta rama również dyskwalifikuje panel, ponieważ traci on swoją sztywność konstrukcyjną i ochronę.
Koszt wymiany pojedynczego uszkodzonego panelu w Polsce waha się zazwyczaj od kilkuset do ponad tysiąca złotych, w zależności od mocy i producenta panela, a do tego dochodzi koszt robocizny ekipy montażowej. Regularne inspekcje pozwalają wcześnie wyłapać drobne uszkodzenia, zanim doprowadzą one do poważniejszych i kosztowniejszych problemów.
Inspekcja wizualna: Co sprawdzić gołym okiem?
Inspekcja wizualna to pierwszy, najprostszy i często niedoceniany krok w procesie diagnozowania uszkodzonego panelu fotowoltaicznego. Wiele problemów z modułami manifestuje się na powierzchni lub w strukturze panelu w sposób widoczny gołym okiem, lub przy użyciu podstawowych narzędzi pomocniczych.
Przed rozpoczęciem inspekcji wizualnej należy zadbać o bezpieczeństwo. Jeśli inspekcja ma miejsce na dachu, wymagany jest odpowiedni sprzęt asekuracyjny, uprawnienia do prac na wysokości i przestrzeganie procedur bezpieczeństwa. Należy pamiętać o wyłączeniu instalacji fotowoltaicznej po stronie AC i DC przed jakimkolwiek dotykaniem przewodów czy złączy, choć sama inspekcja wizualna nie wymaga dotykania elementów pod napięciem.
Optymalnym momentem na inspekcję wizualną jest dzień o dobrym nasłonecznieniu, co pozwoli lepiej dostrzec przebarwienia czy ukryte defekty pod szkłem, oraz ułatwi ewentualne badanie termowizyjne, które wykonuje się równolegle. Do inspekcji z poziomu gruntu lub z drabin/podnośników przydatne mogą być lornetka dobrej jakości i aparat fotograficzny do dokumentowania znalezionych problemów.
Kluczowe punkty inspekcji wizualnej:
Powierzchnia szkła: Obejrzyj szkło pod różnymi kątami, szukając pęknięć. Nawet niewielkie rysy powstały na skutek naprężeń mogą być ledwo widoczne pod jednym kątem, a rzucać się w oczy pod innym. Sprawdź, czy nie ma na szybie odprysków, dużych rys (inne niż powierzchowne), śladów uderzeń (np. od gradu, który mógł pozostawić małe kratery). Szukaj zabrudzeń, które są trudne do usunięcia lub pozostawiły trwałe plamy na szybie.
Stan ogniw pod kątem wizualnym: Przyjrzyj się uważnie poszczególnym ogniwom pod szkłem. Czy wszystkie mają jednolity kolor? Szukaj przebarwień: żółtych lub brązowych obszarów (EVA discoloration), siateczkowatych wzorów lub nieregularnych plam (potencjalny PID), białych "śladów ślimaka" (snail trails). Szukaj ogniw o innym odcieniu niż sąsiednie – może to wskazywać na problem z danym ogniwem.
Wizualna detekcja gorących punktów i wypaleń: Choć badanie termowizyjne jest najlepsze do wykrywania hot-spotów, zaawansowane przypadki przegrzania ogniw mogą być widoczne gołym okiem jako ciemne, spalone obszary na powierzchni ogniwa. Takie wypalone punkty są poważnym uszkodzeniem i sygnałem do natychmiastowej reakcji.
Delaminacja i pęcherze: Dokładnie obejrzyj przestrzeń pod szkłem, szukając oznak delaminacji, czyli rozwarstwienia się folii laminującej EVA. Delaminacja często objawia się jako mleczne, nieprzezroczyste obszary lub widoczne pęcherze powietrza pod szkłem, zazwyczaj zaczynając od krawędzi lub narożników panelu. Jest to sygnał przenikania wilgoci.
Stan ramy i uszczelek: Rama powinna być prosta i bez zniekształceń. Szukaj wgnieceń, zagięć (zwłaszcza w punktach montażowych) i śladów korozji (rdzy). Sprawdź stan uszczelek między ramą a szybą – powinny być elastyczne, nie sparciałe ani popękane, i dokładnie przylegać na całej długości. Niedoskonałości uszczelek to otwarta droga dla wilgoci.
Junkcion Box i kable: Obejrzyj puszkę przyłączeniową na odwrocie panelu. Czy jej obudowa nie jest pęknięta, odkształcona? Czy wszystkie zaślepki lub dławiki kablowe są na miejscu i szczelnie zamknięte? Szukaj jakichkolwiek śladów przegrzania – stopionego plastiku, odbarwień, zapachu spalenizny wokół puszki lub wychodzących z niej kabli.
Kable DC i złącza: Obejrzyj wizualnie kable biegnące od paneli. Czy izolacja nie jest popękana (od UV), przetarta o ostre krawędzie (konstrukcji, innych paneli)? Czy kable są poprawnie ułożone i zabezpieczone opaskami UV, czy nie wiszą luźno? Obejrzyj złącza MC4 (o ile są widoczne i dostępne) – czy nie są uszkodzone mechanicznie, czy nie widać śladów przegrzania (czarny, stopiony plastik).
Konstrukcja montażowa i sposób mocowania paneli: Chociaż nie jest to część panelu, stan konstrukcji i montażu wpływa na panele. Sprawdź, czy konstrukcja nie rdzewieje, czy śruby są dokręcone. Czy klemy montażowe paneli są założone poprawnie, w wyznaczonych przez producenta miejscach, i czy panel nie rusza się w mocowaniach?
Inspekcja wizualna wymaga uwagi i metodyczności. Choć może nie wykryć mikropęknięć ani początkowego PIDu, pozwoli znaleźć wiele oczywistych problemów, które wymagają dalszej diagnostyki lub natychmiastowej reakcji. Uszkodzony panel fotowoltaiczny często daje o sobie znać najpierw wizualnie.
Diagnostyka elektryczna: Testowanie paneli miernikami
Jeśli inspekcja wizualna nie ujawniła problemów, lub wykryte wady nie tłumaczą w pełni spadku wydajności instalacji, kolejnym krokiem jest diagnostyka elektryczna paneli fotowoltaicznych. Pomiar kluczowych parametrów elektrycznych pozwala ocenić, jak panele zachowują się "pod prądem" i porównać ich rzeczywiste osiągi ze specyfikacją producenta lub z parametrami sąsiednich, sprawnych modułów.
Testowanie paneli miernikami elektrycznymi to zadanie wymagające podstawowej wiedzy z zakresu elektrotechniki oraz zachowania szczególnych środków ostrożności. Panele fotowoltaiczne produkują prąd stały (DC), a stringi połączonych paneli mogą generować bardzo wysokie i niebezpieczne napięcia, sięgające nawet kilkuset, a w większych instalacjach ponad 1000 V DC.
Przed przystąpieniem do jakichkolwiek pomiarów elektrycznych, kluczowe jest całkowite odłączenie badanej części instalacji od falownika i sieci energetycznej po stronie AC i DC. Należy zawsze sprawdzić miernikiem, czy na odłączonych przewodach nie ma napięcia, zanim cokolwiek się dotknie lub rozłączy. Praca powinna być wykonywana w odpowiednim obuwiu ochronnym i, w miarę możliwości, z użyciem narzędzi z izolowanymi rękojeściami. Rękawice izolacyjne mogą być wskazane przy pracy z wysokimi napięciami.
Podstawowe pomiary miernikami:
Napięcie jałowe (Voc - Open Circuit Voltage): Ten pomiar polega na zmierzeniu napięcia na zaciskach niepodłączonego (rozwartego) panelu lub stringu. Używa się do tego dobrej jakości multimetru z odpowiednim zakresem napięcia stałego (np. do 1000V lub 1500V DC). Pomiary Voc są stosunkowo proste do wykonania.
Napięcie jałowe jest głównie zależne od temperatury ogniwa – rośnie nieznacznie ze spadkiem temperatury, a maleje ze wzrostem. W mniejszym stopniu zależy od nasłonecznienia. Wynik pomiaru należy porównać ze specyfikacją producenta podaną w karcie katalogowej panelu dla Standardowych Warunków Testowych (STC: 1000 W/m², 25°C temperatury ogniwa) lub dla Rzeczywistych Warunków Pomiaru (NMOT - Nominal Module Operating Temperature). Jeśli zmierzona wartość Voc jest znacząco niższa (np. o więcej niż 5-10%) niż oczekiwana po korekcie na panujące warunki, może to wskazywać na problem z ogniwami, połączeniami wewnątrz panelu lub przerwę w obwodzie stringu.
Prąd zwarcia (Isc - Short Circuit Current): Ten pomiar polega na zmierzeniu prądu przepływającego przez miernik przy bezpośrednim zwarciu zacisków panelu lub stringu. Używa się do tego multimetru z funkcją pomiaru prądu stałego lub, wygodniej i bezpieczniej w stringach, miernika cęgów do DC (DC Clamp Meter). Testowanie paneli miernikami pod kątem Isc wymaga bezpośredniego połączenia, co w przypadku stringu wymaga miernika cęgów, aby uniknąć rozpinania obwodu pod prądem.
Prąd zwarcia jest proporcjonalny do natężenia promieniowania słonecznego (irradiancji) padającego na panel i w niewielkim stopniu zależy od temperatury. Jest to dobry wskaźnik jakości ogniw i ich zdolności do przetwarzania światła na prąd. Należy zmierzyć aktualną irradiancję (miernikiem nasłonecznienia W/m²) i temperaturę panelu, a następnie skorygować wartość Isc z karty katalogowej dla STC do panujących warunków. Jeśli zmierzony Isc jest znacząco niższy (np. o więcej niż 5-10%) od wartości skorygowanej lub od wartości z sąsiedniego, sprawnie działającego panelu w tych samych warunkach, wskazuje to na problemy z ogniwami, częściowe zacienienie lub zwiększoną rezystancję wewnętrzną panelu.
Wszystko wygląda dobrze wizualnie, a Voc i Isc są w normie? Problemem może być punkt mocy maksymalnej (Pmax), który determinuje faktyczną wydajność panelu pod obciążeniem. Multimetr pozwoli zmierzyć Voc i Isc, ale nie powie, ile mocy panel produkuje w punkcie optymalnym (Maximum Power Point - MPP), charakteryzowanym przez napięcie Vmp i prąd Imp.
Zaawansowana diagnostyka - testery PV i pomiar I-V curve:
Aby uzyskać pełniejszy obraz wydajności panelu, konieczne jest użycie dedykowanego testera paneli fotowoltaicznych, potrafiącego narysować krzywą charakterystyki prądowo-napięciowej (I-V curve) oraz mocy (P-V curve). Te testery symulują różne obciążenia, mierząc Vmp, Imp i wyliczając Pmax. Porównanie zmierzonej krzywej z referencyjną (z karty katalogowej skorygowanej na warunki) lub z krzywymi innych paneli w stringu jest najdokładniejszym sposobem oceny stanu technicznego modułu.
Kształt krzywej I-V dostarcza mnóstwo informacji o problemach panelu. "Stopniowanie" na krzywej I-V wskazuje na działanie diod bypass lub problem z grupą ogniw (np. częściowe zacienienie, uszkodzenie wewnętrzne). Zniekształcenie krzywej, zwłaszcza w okolicy MPP, może świadczyć o podwyższonej rezystancji szeregowej (np. luźne połączenia) lub obniżonej rezystancji bocznikowej (np. PID, wilgoć w ogniwach). Znacznie obniżony punkt Pmax wskazuje na ogólną degradację lub uszkodzenie panela.
Pomiar rezystancji izolacji:
Bardzo ważnym, często pomijanym elektrycznym testem jest pomiar rezystancji izolacji paneli i całej instalacji DC do uziemienia. Wykonuje się go za pomocą megomierza (insulation tester), który generuje wysokie napięcie testowe (np. 500V lub 1000V DC) i mierzy prąd upływu. Niska rezystancja izolacji wskazuje na przenikanie wilgoci do paneli (delaminacja, uszkodzone uszczelki/puszki) lub uszkodzenie izolacji kabli.
Minimalna dopuszczalna rezystancja izolacji jest określona w normach instalacyjnych i wytycznych producentów. Typowo oczekuje się wartości >1 MΩ na panel lub wartości zbiorczej dla stringu zgodnie z normą (np. 1 MΩ / (V_systemu / 1000 V), ale nie mniej niż 1 MΩ). Regularny pomiar izolacji pomaga jak sprawdzić uszkodzony panel fotowoltaiczny pod kątem bezpieczeństwa i trwałości, identyfikując ryzyko zwarcia do masy, które może prowadzić do uszkodzenia falownika lub pożaru. Niskie parametry znacznie się różnią od specyfikacji, oznacza to, że panel jest uszkodzony lub niewydajny i wymaga wymiany.
Termowizja: Jak znaleźć uszkodzenia niewidoczne gołym okiem?
Badanie termowizyjne jest jedną z najbardziej efektywnych metod diagnozowania paneli fotowoltaicznych, pozwalającą zlokalizować wiele typów uszkodzeń, które są całkowicie niewidoczne podczas inspekcji wizualnej i nie zawsze jednoznacznie zidentyfikowane przez pomiary elektryczne. Ta technika opiera się na zasadzie, że uszkodzone lub niepracujące prawidłowo elementy panelu fotowoltaicznego zazwyczaj emitują więcej ciepła niż ich sprawne odpowiedniki, lub wręcz przeciwnie – pozostają chłodniejsze, gdy powinny być ciepłe.
Każde pracujące ogniwo fotowoltaiczne nie jest w 100% wydajne; część energii świetlnej, która w nie pada, jest przekształcana nie na energię elektryczną, lecz na ciepło. Jednak w przypadku defektów – takich jak mikropęknięcia, gorące punkty, problemy z połączeniami między ogniwami, wadliwe diody bypass czy efekty PID – strata energii w postaci ciepła jest znacznie większa i lokalna.
Do wykonania inspekcji termowizyjnej niezbędna jest kamera termowizyjna wysokiej jakości. Kluczowe parametry kamery to rozdzielczość matrycy termicznej (im wyższa, tym bardziej szczegółowy obraz i mniejsza plamka pomiarowa, co jest ważne przy małych ogniwach), czułość termiczna (NETD - Noise Equivalent Temperature Difference; im niższa wartość, np. <50 mK, tym mniejsza różnica temperatur jest wykrywalna) oraz zakres temperatur pomiarowych. Dobrej klasy kamera, często montowana na dronie do szybkiego skanowania dużych instalacji dachowych, to inwestycja rzędu kilkunastu lub nawet kilkudziesięciu tysięcy złotych, ale istnieją też tańsze, ręczne modele wystarczające do inspekcji mniejszych instalacji.
Warunki niezbędne do poprawnego badania termowizyjnego:
Panel musi produkować energię elektryczną. Inspekcję termowizyjną paneli wykonuje się podczas pracy systemu, gdy panele są obciążone (podłączone do falownika i produkują prąd). Bezoobciążeniowy panel (np. w nocy lub odłączony) nie ujawni większości defektów poprzez wydzielanie ciepła związanego z przepływem prądu.
Wymagane jest odpowiednie natężenie promieniowania słonecznego. Aby defekty termiczne były wyraźnie widoczne, panele muszą pracować z wystarczającą mocą. Zazwyczaj zaleca się wykonanie pomiarów przy irradiancji powyżej 600 W/m², a najlepiej w pełnym słońcu (800-1000 W/m²). Słabe nasłonecznienie (pochmurny dzień, wczesny poranek, późne popołudnie) sprawi, że różnice temperatur będą zbyt małe, aby były wykrywalne.
Potrzebna jest wystarczająca różnica temperatury między panelem a otoczeniem lub, co ważniejsze, między sprawnymi a uszkodzonymi obszarami panelu. Optymalne warunki to stabilne nasłonecznienie i niezbyt silny wiatr, który może szybko chłodzić powierzchnię paneli, zacierając subtelne różnice temperatur. Unikaj testowania podczas opadów deszczu, gdyż woda na powierzchni może zafałszować pomiar termowizyjny.
Konieczne jest odpowiednie ustawienie kąta kamery względem powierzchni panelu, aby uniknąć odbić promieniowania podczerwonego od sąsiednich obiektów lub nieba, które mogą zakłócić obraz termiczny. Emisyjność powierzchni panelu (szkła) jest wysoka, ale odbicia nadal mogą stanowić problem, zwłaszcza pod ostrymi kątami. Pomocy kamer termowizyjnych sprawdzisz temperaturę paneli, która powinna być we wszystkich miejscach taka, ale często tak nie jest.
Interpretacja obrazów termowizyjnych:
Gorące Punkty (Hot Spots): Widoczne jako jasne, gorące obszary na ciemniejszym tle normalnie pracujących ogniw. Wskazują na obszary o podwyższonej rezystancji, które nadmiernie się nagrzewają. Mogą być spowodowane przez mikropęknięcia, uszkodzone połączenia, zablokowane diody bypass lub długotrwałe, intensywne zacienienie konkretnego obszaru ogniwa. Temperatura w hot spotach może być o 15-20°C, a w skrajnych przypadkach o kilkadziesiąt stopni wyższa od otoczenia. Zidentyfikowanie hot spotów to klucz do szybkiego działania.
Chłodne Ogniwa/Obszary: Na działającym w pełnym słońcu panelu wszystkie sprawne ogniwa powinny być mniej więcej w tej samej, podwyższonej temperaturze (np. 40-60°C). Jeśli widzisz ogniwo lub grupę ogniw, które są znacznie chłodniejsze niż sąsiednie, podczas gdy reszta panelu pracuje normalnie, może to oznaczać, że to ogniwo/grupa ogniw w ogóle nie pracuje. Przyczyną może być przerwa w obwodzie (np. duży crack), uszkodzenie diody bypass (która jest włączona na stałe, obchodząc sekcję) lub całkowity zanik produkcji przez dany obszar z innego powodu. Trzeba odróżnić chłodne obszary spowodowane awarią od tych wynikających z zacienienia – zacieniony obszar naturalnie będzie chłodniejszy, bo nie produkuje i nie jest nagrzewany światłem.
Całe Chłodniejsze Panele lub Stringi: Jeśli cały panel lub cały string (grupa paneli połączonych szeregowo) jest wyraźnie chłodniejszy od sąsiednich stringów czy paneli pracujących w identycznych warunkach nasłonecznienia, może to wskazywać na problem wpływający na całą sekcję. Może to być problem z falownikiem (np. wyłączony kanał MPPT), problem z połączeniami na początku stringu, globalne zacienienie tego stringu (np. drzewo zasłaniające część dachu o danej porze dnia) lub generalnie znacznie niższa wydajność tych modułów.
Problemy z Puszkami Przyłączeniowymi i Złączami: Termowizja jest również doskonałym narzędziem do identyfikowania przegrzewających się diod bypass w puszce przyłączeniowej lub luźnych, skorodowanych złączy kablowych. Obszary te, mimo niewielkich rozmiarów, często generują znaczne ilości ciepła wskutek zwiększonej rezystancji, co kamera termowizyjna doskonale wychwytuje.
Badanie termowizyjne wymaga umiejętności interpretacji obrazów i kontekstualizacji wyników z warunkami pracy systemu. To nie tylko patrzenie na kolory, ale analiza rozkładu temperatury, identyfikacja wzorców i powiązanie ich z potencjalnymi defektami fizycznymi lub elektrycznymi. Jest to jednak metoda niezwykle szybka i efektywna, pozwalająca przeskanować dużą liczbę paneli w krótkim czasie i precyzyjnie wskazać te problematyczne, które wymagają dalszych, bardziej szczegółowych badań lub natychmiastowej wymiany. Znaczące różnice temperatury są kluczowym wskaźnikiem, jak znaleźć uszkodzony panel fotowoltaiczny ukryty w systemie.