Sklejka na podłogę do busa 2025: Przegląd najlepszych rozwiązań i poradnik wyboru
Czy zastanawiałeś się kiedyś, jak uprościć i zabezpieczyć przestrzeń ładunkową swojego busa? Odpowiedź jest zaskakująco prosta – sklejka na podłogę do busa. To rozwiązanie, które łączy w sobie funkcjonalność, trwałość i estetykę, zamieniając surową podłogę w solidną i bezpieczną bazę do pracy.
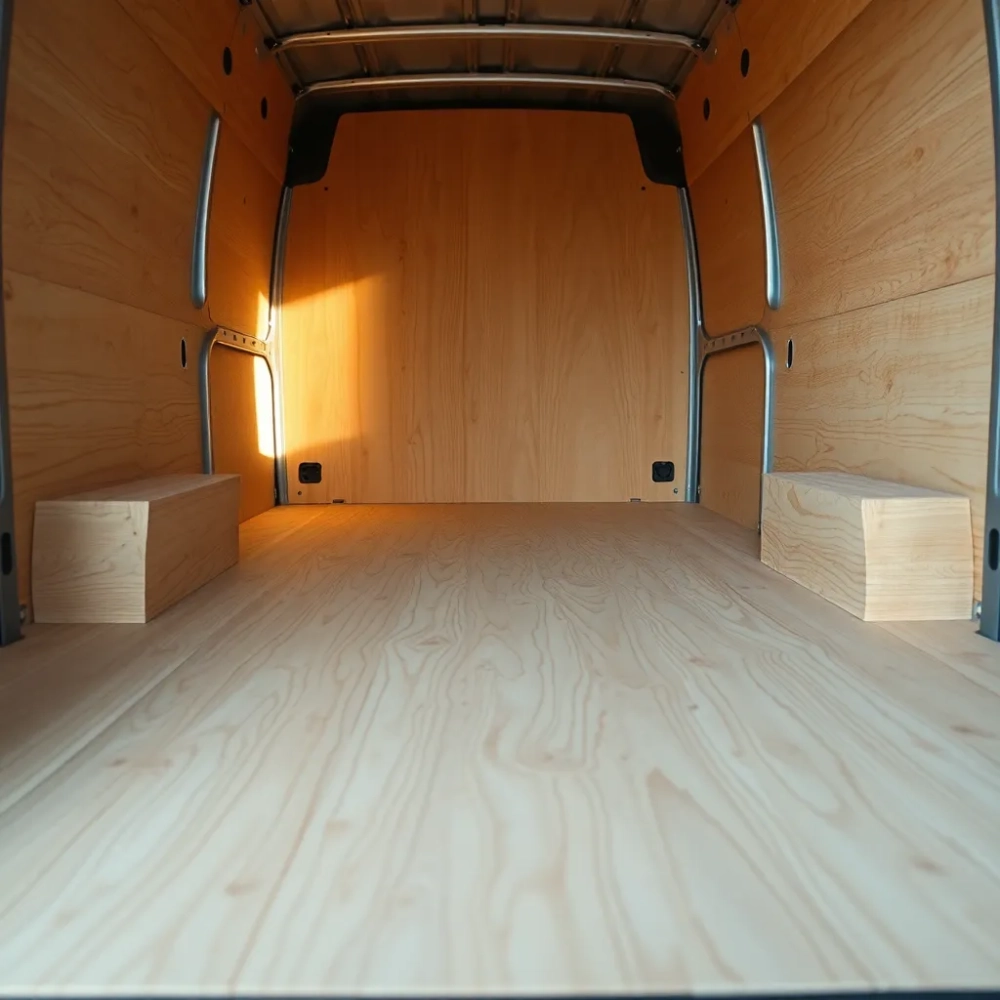
Analizując rynek materiałów wykończeniowych do przestrzeni ładunkowych busów, można dostrzec wyraźną tendencję wzrostową popularności sklejki podłogowej. Jest to wybór podyktowany nie tylko ekonomią, ale przede wszystkim praktycznymi aspektami użytkowania. Zestawiając różne typy wykończeń, sklejka jawi się jako materiał oferujący optymalny balans pomiędzy ceną, trwałością a łatwością montażu. Poniższa tabela przedstawia porównanie kluczowych parametrów dla najczęściej wybieranych rozwiązań.
Materiał | Cena (za m²) | Trwałość (skala 1-5) | Odporność na ścieranie (skala 1-5) | Łatwość montażu (skala 1-5) | Waga (na m², grubość 10mm) |
---|---|---|---|---|---|
Sklejka liściasta | 30-50 PLN | 4 | 4 | 4 | 7 kg |
Sklejka iglasta | 25-40 PLN | 3 | 3 | 4 | 6 kg |
Płyta OSB | 20-35 PLN | 2 | 2 | 3 | 8 kg |
Podłoga aluminiowa (panele) | 150-300 PLN | 5 | 5 | 5 | 5 kg |
Wylewka żywiczna | 80-150 PLN | 5 | 4 | 2 | 10 kg |
Rodzaje sklejki podłogowej do busa – którą wybrać w 2025 roku?
W gąszczu ofert i specyfikacji technicznych łatwo się pogubić, szczególnie gdy stajesz przed wyborem idealnej sklejki podłogowej do busa. Rynek w 2025 roku oferuje szeroki wachlarz opcji, różniących się parametrami, właściwościami i oczywiście ceną. Zanim jednak pochopnie wybierzesz najtańszą opcję, warto zastanowić się, jakie kryteria powinny decydować o twoim wyborze. Czy kluczowa jest wytrzymałość na ekstremalne obciążenia, odporność na wilgoć, a może łatwość utrzymania w czystości? Odpowiedź na te pytania pozwoli zawęzić pole poszukiwań i dokonać świadomego wyboru, który przełoży się na lata bezproblemowego użytkowania.
Na samym początku warto rozróżnić podstawowe typy sklejki, które najczęściej znajdują zastosowanie w busach. Mamy więc sklejkę liściastą, sklejkę iglastą oraz sklejkę specjalistyczną. Ta pierwsza, wykonana z drewna drzew liściastych, takich jak brzoza czy buk, charakteryzuje się wyższą gęstością i twardością. To sprawia, że jest bardziej odporna na uszkodzenia mechaniczne i ścieranie, co jest kluczowe w intensywnie eksploatowanych przestrzeniach ładunkowych. Z kolei sklejka iglasta, wykonana z sosny lub świerku, jest lżejsza i bardziej elastyczna, co może być istotne w konstrukcjach, gdzie waga ma znaczenie. Jest też zazwyczaj tańsza, co czyni ją atrakcyjną opcją dla budżetowych rozwiązań.
W 2025 roku na popularności zyskują sklejki specjalistyczne, projektowane z myślą o konkretnych zastosowaniach. Mowa tu o sklejkach wodoodpornych, idealnych do busów przewożących mokre ładunki, czy sklejkach antypoślizgowych, zwiększających bezpieczeństwo podczas załadunku i rozładunku. Na rynku pojawiają się również sklejki wzmocnione, na przykład kompozytami, oferujące ekstremalną wytrzymałość przy zachowaniu stosunkowo niskiej wagi. Warto zwrócić uwagę na sklejkę filmowaną, pokrytą specjalną powłoką fenolową, która nie tylko chroni drewno przed wilgocią i uszkodzeniami, ale również ułatwia utrzymanie czystości, co jest nieocenione w transporcie spożywczym lub medycznym.
Decydując się na konkretny rodzaj sklejki podłogowej do busa, nie można zapomnieć o grubości materiału. Standardowo, do busów dostawczych najczęściej stosuje się sklejkę o grubości 9 mm, 10 mm, 12 mm, a nawet 15 mm, w zależności od przewidywanego obciążenia i intensywności użytkowania. Cieńsza sklejka, na przykład 9 mm, sprawdzi się w busach lekkich, przewożących stosunkowo lekkie ładunki. Grubsze warianty, 12 mm i więcej, są rekomendowane do busów transportujących ciężkie materiały lub tam, gdzie podłoga jest narażona na intensywne obciążenia punktowe. Warto pamiętać, że grubość sklejki ma bezpośredni wpływ na jej wytrzymałość i trwałość, ale również na wagę, co może mieć znaczenie dla zużycia paliwa i ładowności pojazdu. Dobrze dobrana grubość to gwarancja spokoju na długie lata eksploatacji.
Zalety sklejki podłogowej do busa – trwałość, bezpieczeństwo i ochrona ładunku
Inwestycja w sklejkę podłogową do busa to nie tylko kwestia estetyki czy komfortu, ale przede wszystkim strategiczny krok w kierunku optymalizacji i zabezpieczenia przestrzeni ładunkowej. Mówimy tu o rozwiązaniu, które przynosi realne korzyści w trzech kluczowych obszarach: trwałości, bezpieczeństwie i ochronie ładunku. Zastanówmy się, jak te aspekty przekładają się na codzienną eksploatację busa i dlaczego sklejka podłogowa jest tak ceniona przez profesjonalistów z branży transportowej.
Trwałość to fundament, na którym opiera się ekonomiczna opłacalność każdego rozwiązania w biznesie. W przypadku podłogi do busa, narażonej na ciągłe obciążenia, wstrząsy, tarcie i różnorodne czynniki atmosferyczne, wytrzymałość materiału staje się priorytetem. Sklejka podłogowa, zwłaszcza ta wysokiej jakości, charakteryzuje się imponującą odpornością na uszkodzenia mechaniczne. Nie straszne jej uderzenia, zarysowania czy punktowe naciski ciężkich przedmiotów. Co więcej, sklejka impregnowana lub filmowana jest dodatkowo chroniona przed wilgocią, olejami i chemikaliami, co znacząco wydłuża jej żywotność. W praktyce oznacza to rzadsze i mniej kosztowne wymiany podłogi, co przekłada się na realne oszczędności w długoterminowej perspektywie. Warto też wspomnieć o odporności na ścieranie, która w przestrzeniach ładunkowych jest szczególnie istotna. Dzięki temu sklejka podłogowa zachowuje estetyczny wygląd i funkcjonalność przez długi czas, nawet przy intensywnym użytkowaniu. Pomyślmy o firmie kurierskiej, gdzie busy codziennie pokonują setki kilometrów, a podłoga jest nieustannie narażona na ciężkie paczki, wózki paletowe i intensywny ruch pieszy. W takich warunkach trwała sklejka staje się nieocenionym sprzymierzeńcem w utrzymaniu efektywności operacyjnej.
Bezpieczeństwo to kolejny kluczowy aspekt, na który wpływa sklejka podłogowa do busa. Gładka, śliska, metalowa podłoga w busie, szczególnie podczas deszczu lub mrozu, może stwarzać realne zagrożenie zarówno dla przewożonego ładunku, jak i osób pracujących w przestrzeni ładunkowej. Sklejka antypoślizgowa z specjalną fakturą powierzchni eliminuje to ryzyko, zapewniając stabilność i pewny chwyt. Dzięki temu ładunki nie przemieszczają się w trakcie jazdy, minimalizując ryzyko uszkodzeń i wypadków. Co więcej, antypoślizgowa powierzchnia sklejki zwiększa bezpieczeństwo pracowników podczas załadunku i rozładunku, zapobiegając poślizgnięciom i upadkom. Wyobraźmy sobie sytuację, gdy kurier musi szybko rozładować delikatny ładunek w deszczowy dzień. Sklejka antypoślizgowa daje mu pewność i stabilność, nawet gdy podłoga jest mokra, co znacząco przyspiesza i ułatwia pracę, jednocześnie minimalizując ryzyko uszkodzenia przesyłek. Bezpieczeństwo to nie tylko komfort, ale również wymierne korzyści ekonomiczne, wynikające z redukcji uszkodzeń ładunku, kosztów leczenia urazów i przestojów w pracy.
Wreszcie, ochrona ładunku to trzeci, ale równie istotny argument przemawiający za zastosowaniem sklejki podłogowej do busa. Surowa podłoga w busie, często nierówna i pełna wystających śrub czy nierówności, może być przyczyną uszkodzeń delikatnych ładunków. Sklejka podłogowa tworzy gładką, równą i jednolitą powierzchnię, która amortyzuje wstrząsy i chroni ładunek przed uszkodzeniami mechanicznymi. Dodatkowo, sklejka izoluje termicznie i akustycznie przestrzeń ładunkową, co jest szczególnie ważne w transporcie towarów wrażliwych na temperaturę lub hałas. Pomyślmy o transporcie mebli, sprzętu elektronicznego czy instrumentów muzycznych. Sklejka podłogowa stanowi dodatkową warstwę ochronną, która pomaga dostarczyć ładunek w nienaruszonym stanie. Dla firm transportowych, które przewożą wartościowe i delikatne towary, inwestycja w sklejkę podłogową to gwarancja satysfakcji klienta i uniknięcie kosztownych reklamacji. Podsumowując, trwałość, bezpieczeństwo i ochrona ładunku to trzy filary, na których opiera się przewaga sklejki podłogowej do busa nad innymi rozwiązaniami. To inwestycja, która zwraca się wielokrotnie, przynosząc wymierne korzyści w każdym aspekcie użytkowania busa.
Jak samodzielnie zamontować sklejkę podłogową w busie – poradnik krok po kroku
Myślisz o samodzielnym montażu sklejki podłogowej do busa? To zadanie, które z odpowiednim przygotowaniem i odrobiną zręczności, możesz z powodzeniem wykonać samodzielnie, oszczędzając tym samym na kosztach usługi montażu. Kluczem do sukcesu jest precyzja, cierpliwość i korzystanie z odpowiednich narzędzi. Przedstawiamy kompleksowy poradnik krok po kroku, który przeprowadzi Cię przez cały proces montażu, od przygotowania, aż po finalne wykończenie.
Zanim przystąpisz do działania, upewnij się, że masz wszystko, czego potrzebujesz. Lista niezbędnych narzędzi i materiałów nie jest długa, ale każdy element ma swoje znaczenie. Będziesz potrzebować oczywiście sklejki podłogowej, najlepiej dociętej na wymiar twojego busa. Na rynku dostępne są również gotowe zestawy sklejki, precyzyjnie wycięte do konkretnych modeli samochodów. To znaczne ułatwienie, szczególnie dla osób, które nie czują się pewnie w cięciu drewna. Oprócz sklejki, przygotuj: wiertarkę, wkrętarkę, wyrzynarkę (jeśli sklejka wymaga docinania), miarkę, ołówek, szlifierkę (do wygładzania krawędzi), papier ścierny, śruby lub wkręty do drewna, klej do drewna (opcjonalnie, dla wzmocnienia połączeń), oraz rękawice ochronne i okulary. Pamiętaj o dokładnym pomiarze przestrzeni ładunkowej i sprawdzeniu, czy sklejka pasuje wymiarami. Precyzja na etapie przygotowania to podstawa udanego montażu.
Pierwszym krokiem montażu jest przygotowanie podłoża. Oczyść dokładnie podłogę busa z wszelkich zabrudzeń, kurzu, piasku i resztek materiałów. Sprawdź, czy nie ma żadnych wystających elementów, śrub czy ostrych krawędzi, które mogłyby uszkodzić sklejkę lub utrudnić montaż. Jeśli podłoga jest nierówna, warto zastosować podkładki wyrównujące, aby sklejka leżała stabilnie i równo. Możesz użyć do tego cienkich pasków sklejki lub specjalnych podkładek z tworzywa sztucznego. Następnie, przymierz sklejkę do podłogi busa. Jeśli korzystasz z gotowego zestawu, elementy powinny idealnie pasować do kształtu podłogi. Jeśli sklejka wymaga docinania, wykorzystaj wyrzynarkę i precyzyjnie wytnij odpowiedni kształt. Pamiętaj o zachowaniu marginesu bezpieczeństwa i unikaj zbyt ciasnego dopasowania, które może utrudnić montaż i powodować naprężenia sklejki. Po docięciu, wygładź krawędzie sklejki szlifierką lub papierem ściernym, aby uniknąć ostrych krawędzi i drzazg. Przygotowanie podłoża i dokładne dopasowanie sklejki to kluczowe etapy, które decydują o jakości i trwałości montażu.
Kolejnym krokiem jest mocowanie sklejki do podłogi busa. Istnieje kilka metod montażu, a wybór zależy od preferencji i specyfiki busa. Najpopularniejszą metodą jest mocowanie sklejki za pomocą wkrętów do drewna. Wywierć otwory w sklejce w miejscach, gdzie planujesz wkręcić śruby. Otwory powinny być nieco większe niż średnica śrub, aby sklejka mogła swobodnie pracować pod wpływem temperatury i wilgoci. Przyłóż sklejkę do podłogi busa i, wykorzystując istniejące otwory montażowe w podłodze busa (jeśli są dostępne), przykręć sklejkę za pomocą wkrętarki. Dokręcaj śruby z umiarem, aby nie uszkodzić sklejki i nie zerwać gwintu. Alternatywną metodą jest klejenie sklejki do podłogi busa. W tym przypadku, nałóż klej do drewna na spodnią stronę sklejki i równomiernie rozprowadź go po całej powierzchni. Przyłóż sklejkę do podłogi busa i mocno dociśnij. Możesz dodatkowo obciążyć sklejkę ciężkimi przedmiotami na czas schnięcia kleju. Metoda klejenia jest mniej inwazyjna, ale wymaga dokładnego oczyszczenia i odtłuszczenia powierzchni oraz stosowania odpowiedniego kleju. Warto również rozważyć kombinację obu metod - klejenie i dodatkowe mocowanie wkrętami w strategicznych miejscach. Niezależnie od wybranej metody, upewnij się, że sklejka jest stabilnie i bezpiecznie zamocowana do podłogi busa. Pamiętaj, jedyni na rynku posiadamy podłogę w jednym elemencie do każdego modelu samochodu. Są dopasowane i gotowe do montażu do najbardziej typowych modeli samochodów dostawczych na rynku. W zestawie dołączone są również miseczki haków montażowych, odpowiednie do konkretnego modelu. Takie rozwiązanie znacząco upraszcza i przyspiesza proces montażu, eliminując potrzebę docinania i dopasowywania elementów.