Płytki czy Panele Najpierw? Prawidłowa Kolejność Układania Podłóg 2025
Współczesne projekty wnętrz często stawiają na płynne przejścia i otwarte przestrzenie, zacierając granice między poszczególnymi strefami domu czy mieszkania. Kuchnia połączona z salonem to już standard, a naturalnym wizualnym sygnałem zmiany funkcji staje się często inny rodzaj podłogi – gres w strefie gotowania, panele w części wypoczynkowej. Takie rozwiązania są praktyczne, ale rodzą kluczowe pytanie, na które każdy remontujący musi sobie odpowiedzieć: co najpierw kłaść płytki czy panele? Eksperci branżowi są w tej kwestii zgodni – prawidłowa kolejność to układanie płytek przed panelami. Materiał trudniejszy w obróbce powinien zawsze iść pierwszy, by uniknąć uszkodzeń już położonej, bardziej delikatnej podłogi.
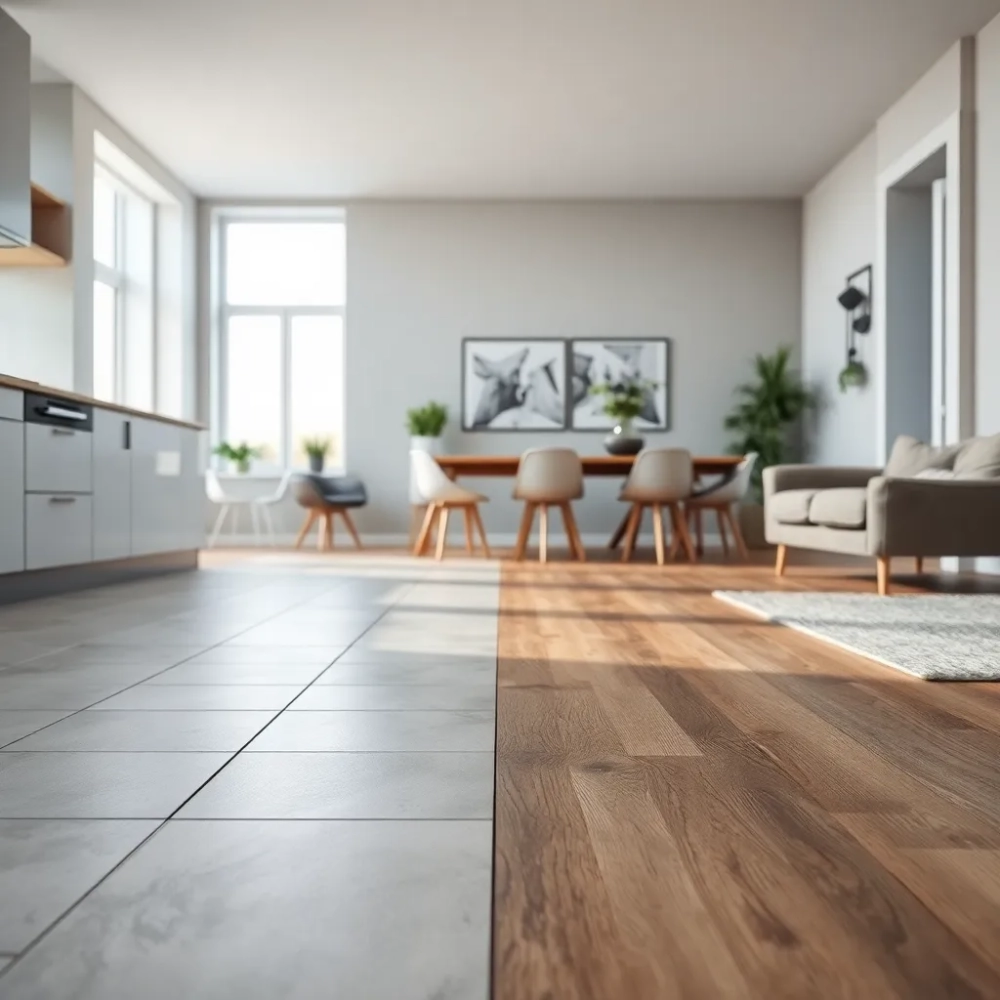
Analizując proces układania różnych rodzajów podłóg, widać wyraźne różnice w metodologii i czasie potrzebnym na poszczególne etapy. Ułożenie metra kwadratowego płytek ceramicznych czy gresu jest z reguły bardziej pracochłonne i czasochłonne niż montaż paneli laminowanych, a co za tym idzie, często generuje wyższe koszty robocizny za jednostkę powierzchni. Rozważmy przeciętne nakłady pracy i materiałów dla porównywalnych powierzchni:
Czynnik | Płytki Ceramiczne/Gres (za 10 m²) | Panele Laminowane (za 10 m²) |
---|---|---|
Orientacyjny czas pracy (samego układania) | ~1.5 - 3 dni (z przygotowaniem podłoża i fugowaniem) | ~0.5 - 1 dzień |
Szacowany koszt materiałów (średnia półka) | ~800 - 1500 PLN (płytki, klej, fuga, grunt) | ~400 - 800 PLN (panele, podkład, listwy) |
Potrzebne narzędzia specjalistyczne | Przecinarka do płytek (wodna lub ręczna), mieszadło do kleju, kielnia zębata, packi, gąbki | Ukośnica/wyrzynarka, młotek, klocki montażowe |
Wymagany czas schnięcia/wiązania | Klej: ~24h, Fuga: ~48-72h (przed pełnym obciążeniem) | Brak (poza schnięciem wylewki samopoziomującej, jeśli była użyta) |
Powyższe dane, choć uśrednione, wyraźnie ilustrują, że praca z płytkami wymaga większych nakładów czasu ze względu na procesy chemiczne wiązania klejów i fug, a także precyzyjne docinanie twardego materiału na mokro, generujące specyficzny rodzaj zabrudzeń. Układanie paneli, zwłaszcza w systemie "klik", jest znacznie szybsze i czystsze. To właśnie te aspekty – długi czas wiązania, konieczność użycia mokrych zapraw i potencjalny bałagan – sprawiają, że logika wskazuje na to, aby etap prac mokrych i brudnych zakończyć przed przejściem do montażu paneli, które są podłogą "suchą" i bardziej podatną na uszkodzenia mechaniczne w trakcie dalszych prac.
Dlaczego Układanie Płytek Rozpoczynamy Przed Panelami?
Decyzja o tym, co położyć najpierw: płytki czy panele, podyktowana jest logiką procesów budowlanych i charakterystyką samych materiałów. Układanie płytek jest zazwyczaj procesem "mokrym". Wymaga użycia klejów i fug, które potrzebują czasu na związanie i wyschnięcie. Ten etap generuje pył z cięcia (szczególnie przy użyciu przecinarki wodnej, ale nawet cięcie na sucho generuje znaczne ilości pyłu), resztki kleju, fugi, a także ryzyko zachlapań i zabrudzeń na dużą skalę.
Panele laminowane czy drewniane układane są zazwyczaj jako system podłogi pływającej na suchym podkładzie. Ich montaż jest szybszy, mniej inwazyjny i generuje przede wszystkim pył drzewny/laminatowy podczas cięcia. Wyobraźmy sobie sytuację, gdy panele leżą już na swoim miejscu, a my zaczynamy docinać i układać płytki obok. Ryzykujemy porysowanie lub trwałe zabrudzenie gotowej, delikatniejszej powierzchni paneli cementowym pyłem, klejem, czy resztkami fugi, które mogą być trudne, a nawet niemożliwe do usunięcia.
Ponadto, kleje do płytek wymagają twardego, stabilnego podłoża i czasu na pełne związanie. Ten proces może trwać od 24 godzin dla podstawowych klejów, do kilku dni w przypadku bardziej wymagających aplikacji czy grubszych warstw. Płytki, które nie zdążyły się w pełni związać z podłożem, są niestabilne i podatne na przesuwanie lub pękanie pod obciążeniem, co mogłoby nastąpić, gdybyśmy od razu rozpoczęli intensywne prace związane z układaniem paneli. Odczekanie z układaniem paneli pozwala płytkom solidnie osiąść i związać się z podłożem.
Ułożenie płytek jako pierwszego elementu pozwala także na dokładne wyznaczenie linii styku z przyszłą podłogą panelową. Po stwardnieniu kleju i fugi, krawędź ułożonej podłogi ceramicznej stanowi solidny punkt odniesienia, do którego panele mogą być precyzyjnie dopasowane. Docinanie paneli do istniejącej krawędzi płytek jest łatwiejsze i mniej ryzykowne niż docinanie płytek do delikatnej krawędzi już położonych paneli, gdzie najmniejszy błąd w cięciu kafelka mógłby uszkodzić sąsiadujący panel.
Specyfika montażu paneli podłogowych, polegająca na łączeniu desek na pióro i wpust lub system "klik" i układaniu ich na elastycznym podkładzie, wymaga czystego i równego podłoża, ale nie generuje takiej ilości wilgoci czy uciążliwego pyłu jak prace glazurnicze. Kończąc najpierw z "mokrymi" i "brudnymi" pracami z płytkami, minimalizujemy ryzyko przeniesienia zabrudzeń na powierzchnię paneli. Cementowy pył z cięcia gresu potrafi unosić się w powietrzu i osiadać na wszelkich powierzchniach, wnikając w spoiny czy drobne nierówności paneli, co później może stać się utrapieniem.
Prace związane z fugowaniem płytek, które następują po ułożeniu i związaniu kleju, również mogą być chaotyczne. Nadmiar fugi jest usuwany na mokro, a pozostałości często wymagają kilkukrotnego mycia powierzchni płytek. Wykonywanie tych czynności przy już ułożonych panelach stwarzałoby wysokie ryzyko nieodwracalnego zabrudzenia ich powierzchni, zwłaszcza jeśli są to panele z V-fugą lub strukturą drewna, w której mogłyby utkwić drobiny zaprawy.
Ponadto, ciężar narzędzi, takich jak przecinarka wodna, wiadra z zaprawą czy opakowania płytek, jest znaczny. Przenoszenie ich przez obszar z już ułożonymi panelami mogłoby prowadzić do zarysowań, wgnieceń czy nawet uszkodzenia systemu zamków w panelach, co w skrajnych przypadkach wymagałoby demontażu i wymiany fragmentu podłogi. Rozpoczęcie od płytek pozwala swobodnie manewrować ciężkimi materiałami i narzędziami w "strefie brudnej" bez ryzyka uszkodzenia docelowej podłogi panelowej w sąsiedztwie.
Należy również wziąć pod uwagę potrzebę dylatacji, czyli szczelin umożliwiających naturalną pracę materiałów pod wpływem zmian temperatury i wilgotności. Płytki i panele pracują w różny sposób. Ułożenie płytek najpierw, z pozostawieniem odpowiedniej szczeliny przy planowanym styku z panelami, pozwala na stworzenie precyzyjnego miejsca na dylatację, która zostanie następnie przykryta odpowiednim profilem lub wypełnieniem. Gdybyśmy ułożyli panele jako pierwsze, precyzyjne docięcie twardych płytek do ich krawędzi, z jednoczesnym zachowaniem wymaganej szczeliny dylatacyjnej, byłoby znacznie trudniejsze i niosłoby większe ryzyko błędu.
Podsumowując, układanie płytek przed panelami to standardowa procedura w branży podłogowej, wynikająca z różnic w procesach instalacji i właściwościach materiałów. Jest to strategia minimalizująca ryzyko uszkodzeń i zabrudzeń gotowej podłogi, a także ułatwiająca osiągnięcie estetycznego i trwałego połączenia obu rodzajów nawierzchni. Kafelki jako materiał trudniejszy w obróbce powinny zająć swoje miejsce jako pierwsze.
Jak Dobrać Płytki i Panele, Aby Podłoga Była Trwała? Klasa Ścieralności
Dobór odpowiednich materiałów to kwestia nie tylko estetyki, ale przede wszystkim trwałości, zwłaszcza gdy planujemy połączyć płytki i panele w jednej przestrzeni, na przykład w otwartej kuchni z salonem. Kluczowym aspektem technicznym, który pozwala uniknąć kosztownych problemów w przyszłości, jest dopasowanie materiałów o zbliżonej wytrzymałości na zużycie. Chodzi tutaj głównie o klasy ścieralności, choć nie tylko.
Dla paneli laminowanych podstawowym wskaźnikiem jest klasa ścieralności, oznaczana symbolami od AC1 do AC6. Klasa AC3 jest odpowiednia do pomieszczeń o niskim i średnim natężeniu ruchu w warunkach domowych (np. sypialnia). Klasa AC4 to dobry wybór do większości pomieszczeń mieszkalnych, w tym tych o średnim natężeniu ruchu, jak salon czy jadalnia. Natomiast klasy AC5 i AC6 są przeznaczone do pomieszczeń o wysokim natężeniu ruchu domowego (korytarze, kuchnie) lub nawet do zastosowań komercyjnych o średnim (AC5) lub wysokim (AC6) natężeniu ruchu.
Dla płytek ceramicznych szkliwionych (np. glazura na ścianę, ale także niektóre płytki podłogowe szkliwione) stosuje się klasy PEI (Porcelain Enamel Institute), numerowane od 0 do 5. Klasa PEI I i II to płytki bardzo delikatne, przeznaczone na ściany lub podłogi o minimalnym ruchu i bez kontaktu z twardymi, rysującymi materiałami (np. łazienki bez bezpośredniego wejścia z zewnątrz). Klasa PEI III nadaje się do pomieszczeń mieszkalnych o normalnym ruchu, jak większość pokoi. PEI IV to płytki na podłogi o intensywnym ruchu w warunkach domowych (przedpokój, kuchnia) oraz o niewielkim ruchu komercyjnym. PEI V oznacza płytki o najwyższej odporności na ścieranie, stosowane w miejscach o bardzo dużym natężeniu ruchu, zarówno w domach, jak i w obiektach użyteczności publicznej. Płytki nieszkliwione, jak gres barwiony w masie, zazwyczaj nie są klasyfikowane wg PEI, a ich odporność na ścieranie jest bardzo wysoka i bardziej jednorodna w całej grubości materiału.
W przestrzeniach, gdzie panele łączą się z płytkami – na przykład na granicy kuchni (płytki) i salonu (panele) – obie nawierzchnie będą narażone na podobne natężenie ruchu, a często także na podobne rodzaje zabrudzeń (piasek, drobne kamyki przyniesione z zewnątrz). Połączenie płytek PEI V lub gresu o wysokiej odporności (charakteryzowanego np. wg normy PN-EN ISO 10545-6) z panelami AC3 byłoby proszeniem się o kłopoty. Podczas gdy płytki pozostaną praktycznie niezmienione przez lata, panele z niższej klasy ścieralności mogą zacząć wykazywać widoczne przetarcia i rysy już po kilku latach intensywnego użytkowania.
Taki dysonans w zużyciu nie tylko szpeci estetykę podłogi, która przestaje wyglądać jednolicie, ale może również prowadzić do problemów funkcjonalnych, a w najgorszym przypadku do konieczności przedwczesnej wymiany fragmentu podłogi panelowej. Pomyślcie o tym: płytki są wieczne, a panele wytarte do białego – kto wtedy zawinił? Ano, zawinił zły dobór materiałów! Wymiana paneli na 20m² salonu, podczas gdy sąsiadująca kuchnia z płytkami 10m² jest nienaruszona, to spory wydatek i logistyczne wyzwanie.
Aby uniknąć takiej sytuacji, do twardych i odpornych na ścieranie płytek stosowanych w miejscach o dużym natężeniu ruchu (jak kuchnia, korytarz) należy dobierać panele laminowane lub drewniane o odpowiednio wysokiej klasie ścieralności. Jeśli w kuchni kładziemy gres o najwyższej odporności na ścieranie lub płytki PEI IV/V, w salonie czy jadalni połączonej z tą strefą powinny znaleźć się panele laminowane przynajmniej klasy AC4, a najlepiej AC5. Choć panele AC5 czy AC6 są zazwyczaj droższe (cena za m² może być o 30-60% wyższa niż AC3), ich wydłużona żywotność i lepsze dopasowanie do trwałości płytek z nawiązką rekompensują tę różnicę w perspektywie lat. Przykład: Panele AC3 za ok. 50 PLN/m², AC5 za ok. 80 PLN/m². Na 20m² różnica to 600 PLN, ale spokój na lata.
Poza ścieralnością, w strefach przejściowych warto zwrócić uwagę także na inne parametry, takie jak odporność na zarysowania (np. twardość w skali Mohsa dla płytek lub specyficzne testy dla paneli), odporność na uderzenia oraz, co ważne w kuchni, odporność na wilgoć. Niektóre panele laminowane są specjalnie impregnowane, aby lepiej znosić kontakt z wodą (tzw. panele wodoodporne czy hydrofobowe), co czyni je lepszym wyborem do połączenia z płytkami w aneksie kuchennym, nawet jeśli sama klasa ścieralności jest wysoka. Płytki z natury są odporne na wilgoć, ale w kuchni ważne jest także, aby były antypoślizgowe (klasy R od R9 do R13).
Podsumowując ten wątek, harmonijne starzenie się połączonych materiałów podłogowych jest równie ważne jak ich estetyczne dopasowanie. Wybierając płytki i panele, zwróćmy uwagę nie tylko na kolor i wzór, ale przede wszystkim na parametry techniczne, z klasą ścieralności na czele. Panele podłogowe powinny dorównywać trwałością sąsiednim płytkom, aby uniknąć sytuacji, w której jedne zużywają się znacznie szybciej niż drugie, co zmusza do kosztownej i uciążliwej wymiany. Inwestycja w wyższą klasę ścieralności paneli przy styku z płytkami to po prostu dobry, racjonalny ruch.
Równy Poziom Podłóg: Jak Uzyskać Idealne Połączenie Płytek i Paneli?
Jednym z największych wyzwań technicznych przy łączeniu dwóch różnych rodzajów podłóg, takich jak płytki i panele, jest zapewnienie idealnie równego poziomu obu powierzchni. Nawet minimalna różnica wysokości, rzędu kilku milimetrów, może stanowić poważny problem, zarówno wizualny, jak i funkcjonalny. Nierówne połączenie to nie tylko estetyczny zgrzyt, ale także potencjalne ryzyko potknięcia oraz utrudnienie, a czasem wręcz uniemożliwienie zastosowania estetycznych i dyskretnych sposobów maskowania dylatacji.
Zarówno płytki, jak i panele wymagają stabilnego i równego podłoża. Idealnym fundamentem jest zazwyczaj odpowiednio przygotowany, suchy i wypoziomowany jastrych cementowy lub anhydrytowy. Problem pojawia się, gdy grubość materiałów wraz z warstwą kleju lub podkładu różni się, lub gdy istniejące podłoże nie jest idealnie płaskie. Różne grubości płytek (od 6 mm cienkich, rektyfikowanych po 20 mm grube gresy) i paneli (najczęściej 8-12 mm) w połączeniu z grubością warstwy kleju (3-15 mm, zależnie od formatu płytki i równości podłoża) oraz grubością podkładu pod panele (2-5 mm) mogą stworzyć znaczące różnice poziomów.
Kluczem do sukcesu jest precyzyjne planowanie i przygotowanie podłoża na wczesnym etapie remontu, często zanim jeszcze kupimy materiały wykończeniowe. Pierwszym krokiem jest dokładne zmierzenie poziomu istniejącego podłoża na całej łączonej powierzchni, na przykład za pomocą długiej poziomicy lub poziomicy laserowej. Pozwala to zidentyfikować wszelkie nierówności, wybrzuszenia czy zagłębienia, które wymagają naprawy. Typowe nierówności, dopuszczalne przy standardowym układaniu podłóg, to zazwyczaj 2-3 mm na 2 metrach, ale przy łączeniu różnych materiałów najlepiej dążyć do niemal perfekcyjnej płaskości.
Jeśli nierówności są większe, konieczne może być zastosowanie wylewki samopoziomującej. Wylewka samopoziomująca to płynna masa, którą wylewa się na przygotowane (zagruntowane) podłoże, a która pod wpływem grawitacji rozpływa się, tworząc idealnie równą, gładką powierzchnię. Wylewki te mają różne grubości aplikacji minimalne i maksymalne, np. od 1 mm do 20 mm w jednej warstwie. Jej użycie pozwala uzyskać idealną płaszczyznę bazową dla obu typów podłóg. Należy jednak pamiętać, że wylewki samopoziomujące również wymagają czasu na związanie i całkowite wyschnięcie (często od kilku dni do nawet kilku tygodni, w zależności od grubości warstwy i warunków w pomieszczeniu).
Po przygotowaniu równego podłoża (lub w przypadku nowego jastrychu), należy dokładnie obliczyć wysokość docelowej podłogi dla płytek i dla paneli. Dla płytek będzie to: grubość płytki + grubość kleju. Dla paneli: grubość panelu + grubość podkładu. Grubość kleju pod płytkami jest zmienna – zależy od formatu płytki (duże formaty wymagają grubszej warstwy, ok. 8-12 mm, a czasem nawet więcej, jeśli klei się na tzw. "masło" w celu zniwelowania minimalnych nierówności samej płytki czy podłoża) oraz zaleceń producenta kleju. Zazwyczaj mieści się w przedziale 5-15 mm. Grubość podkładu pod panele zależy od jego rodzaju – filcowy może mieć 3-5 mm, piankowy 2-3 mm, a droższe podkłady wyciszające zintegrowane z matą paroszczelną ok. 3-5 mm.
Chodzi o to, aby suma grubości dla obu typów podłóg była identyczna. Jeśli płytki z klejem wychodzą wyżej niż panele z podkładem, można to skorygować, stosując grubszą warstwę kleju pod płytkami (jeśli mieszczą się w zaleceniach producenta i format płytki na to pozwala) lub podnosząc poziom podłoża w strefie paneli poprzez dodatkową warstwę wylewki samopoziomującej lub specjalne maty poziomujące pod podkład. Jeśli panele wychodzą wyżej, jedyną opcją na uzyskanie równego poziomu na przygotowanym podłożu jest użycie cieńszych paneli/podkładu lub grubszych płytek/więcej kleju, o ile jest to technicznie możliwe i zgodne z normami. Pamiętajmy, że kleju nie należy stosować pod panelami!
Dokładne wyliczenie poziomów i odpowiednie przygotowanie podłoża przed rozpoczęciem układania to absolutna podstawa. Zazwyczaj dąży się do tego, aby to poziom płytek wyznaczał bazę wysokościową, a następnie poziom podłoża w strefie paneli był do tego dopasowywany (podnoszony lub korygowany wylewką), tak aby po położeniu paneli i podkładu obie powierzchnie spotkały się na tej samej wysokości. Można sobie nawet zrobić małą "próbkę" – ułożyć kawałek płytki z planowaną warstwą kleju oraz kawałek panela z podkładem na docelowym podłożu, aby sprawdzić poziom. To pozwala na precyzyjne ustalenie docelowej wysokości posadzki.
Co zrobić, gdy różnica poziomów już istnieje i jest niewielka (np. 1-4 mm)? W takim przypadku można spróbować zniwelować ją częściowo lub całkowicie za pomocą odpowiedniego rodzaju listwy przejściowej, która ma profil pozwalający na łagodne przejście między różnymi wysokościami. Niestety, takie listwy bywają mniej estetyczne i bardziej widoczne niż profile do łączenia powierzchni o równym poziomie. Z kolei większe różnice (powyżej 5 mm) są trudne do estetycznego zamaskowania i niemal zawsze wymagają korekty podłoża, np. poprzez częściowe zdjęcie istniejącego jastrychu pod cieńszą posadzką lub wylanie dodatkowej warstwy wylewki pod posadzką, która wyszła niżej.
Zatem klucz do idealnego połączenia estetycznego i funkcjonalnego to nie tylko wybór odpowiednich materiałów i sposobu łączenia, ale przede wszystkim inwestycja w perfekcyjne przygotowanie i wyrównanie podłoża. Dopilnuj też, by oba rodzaje podłogi miały równą wysokość już na etapie planowania prac, a nie tylko po ich wykonaniu. Precyzja na tym etapie zaprocentuje piękną, równą i bezpieczną podłogą bez widocznych uskoków i potknięć, umożliwiając zastosowanie dyskretnych, estetycznych rozwiązań do maskowania dylatacji. Mała różnica między poziomami posadzek naprawdę może uniemożliwić zastosowanie większości dyskretnych profili, skazując nas na mniej zgrabne rozwiązania.
Sposoby Łączenia Płytek i Paneli: Estetyka i Funkcjonalność
Styk między dwiema różnymi nawierzchniami podłogowymi w jednej płaszczyźnie, takimi jak płytki i panele, wymaga przemyślanego i solidnego wykończenia. To nie tylko kwestia estetyki, ale także konieczność techniczna związana z dylatacją – czyli szczeliną, która umożliwia niezależną pracę (rozszerzanie i kurczenie) każdego z materiałów pod wpływem zmian temperatury i wilgotności. Ignorowanie potrzeby dylatacji lub jej niewłaściwe wykończenie może prowadzić do wybrzuszania się paneli, pękania fug, a nawet uszkodzenia krawędzi płytek. Istnieje kilka podstawowych sposobów na jak połączyć płytki z panelami, każdy z własnymi zaletami, wadami i specyfiką montażu.
Najpopularniejszym i najbardziej uniwersalnym rozwiązaniem są listwy przejściowe, zwane też profilami dylatacyjnymi. Są one dostępne w różnych kształtach, materiałach i kolorach, co pozwala dopasować je do stylu wnętrza i konkretnej sytuacji montażowej. Najczęściej spotykane profile wykonane są z aluminium (często anodowanego, malowanego proszkowo lub oklejonego folią imitującą drewno), mosiądzu, stali nierdzewnej, a także z tworzywa sztucznego lub drewna. Ich kształt może być prosty (np. płaskie listwy), T-kształtny (do równego poziomu), Z-kształtny (gdy panele są nieco niżej niż płytki), a także L-kształtny lub specjalne profile kompensujące niewielkie różnice poziomów.
Listwy T-kształtne są idealne do łączenia dwóch powierzchni o równym poziomie podłóg, co podkreśla znaczenie perfekcyjnego przygotowania podłoża. Montuje się je zazwyczaj na dyblach lub klei do podłoża w szczelinie dylatacyjnej. Często posiadają ukryty system mocowania, który po zainstalowaniu jest niewidoczny. Przykład: aluminiowa listwa T-kształtna o szerokości 20mm i długości 90 cm kosztuje od ok. 25 do 60 PLN, zależnie od materiału i wykończenia. Są stosunkowo łatwe w montażu i dobrze maskują szczelinę dylatacyjną, ale są widoczne na podłodze i mogą stanowić minimalną przeszkodę, np. dla kółek krzesła.
W przypadku niewielkich różnic poziomów (do ok. 3-5 mm), można zastosować profile z łagodnym przejściem. Mają one zazwyczaj jedną krawędź zaprojektowaną tak, aby płynnie nakładać się na niższą podłogę (np. panele), podczas gdy druga krawędź przylega do wyższej podłogi (np. płytki). Nie są one tak dyskretne jak listwy T-kształtne przy równym poziomie, ale skutecznie niwelują małe uskoki. Ich cena jest porównywalna z listwami T-kształtnymi. Wybór odpowiedniego kształtu listwy zależy więc bezpośrednio od precyzji wykonania posadzki na etapie przygotowania podłoża i układania obu nawierzchni.
Alternatywnym, bardziej minimalistycznym rozwiązaniem jest wypełnienie szczeliny dylatacyjnej elastycznym materiałem, najczęściej silikonem budowlanym lub akrylem. Ta metoda daje efekt wizualnie niemal "czystego" połączenia bez wystającego profilu. Wymaga jednak bardzo precyzyjnego docięcia obu materiałów (zwłaszcza krawędzi paneli i płytek) oraz idealnie równego poziomu. Szczelina musi być czysta i odtłuszczona. Przed aplikacją silikonu/akrylu brzegi podłóg zazwyczaj zabezpiecza się taśmą malarską, aby linia wypełnienia była prosta i czysta. Po aplikacji masa jest wygładzana szpatułką.
Wypełnienie silikonem sprawdza się najlepiej w miejscach o niskim natężeniu ruchu i tam, gdzie nie ma ryzyka wprowadzania brudu czy piasku w spoinę (np. w połączeniu kuchni/salonu, ale z dala od drzwi wejściowych). Silikon jest elastyczny i dobrze przenosi niewielkie ruchy materiałów. Jego wady to skłonność do zbierania brudu (szczególnie jasne kolory w kuchni) oraz ograniczona odporność mechaniczna – silikonowa spoina może się z czasem wycierać lub uszkodzić. Cena tubki dobrego silikonu sanitarnego/budowlanego to ok. 20-40 PLN, co jest znacznie niższym kosztem materiałowym niż listwy, ale wymaga precyzyjnej pracy i nierzadko regularnego odnawiania. Akryl jest mniej elastyczny i nie nadaje się do miejsc, gdzie podłogi pracują intensywniej, a także chłonie wilgoć, więc do kuchni czy przedpokoju jest mniej zalecany niż silikon.
Innym, mniej popularnym, ale wartym rozważenia rozwiązaniem, zwłaszcza przy podłogach drewnianych lub panelach wysokiej jakości, jest zastosowanie korka dylatacyjnego. Korek dylatacyjny to listwa wykonana ze sprasowanego korka, którą wkleja się w szczelinę dylatacyjną między płytkami a panelami. Jest naturalny, elastyczny i estetyczny, często stosowany przy połączeniu płytek z parkietem czy deskami. W przypadku paneli laminowanych jest rzadziej używany, ale może być opcją przy panelach imitujących drewno. Listwy korkowe są dostępne w różnych szerokościach (np. 10-15 mm) i długościach. Po wklejeniu, nadmiar można odciąć i przeszlifować, a następnie polakierować lub zabejcować, aby dopasować kolorystycznie do paneli.
Zaletą korka jest jego naturalny wygląd i dobra zdolność do kompensowania ruchów podłóg. Jest stosunkowo trwały i elastyczny. Wadą może być ograniczony wybór kolorystyczny (naturalny korek, chyba że barwiony) oraz niższa odporność na intensywne ścieranie czy wilgoć w porównaniu do listew metalowych czy płytek. Wymaga też starannego wklejenia i zabezpieczenia. Cena listwy korkowej o szerokości ok. 10 mm to ok. 15-30 PLN za metr bieżący. Jest to rozwiązanie, które wymaga odrobiny manualnych umiejętności i dbałości o szczegóły podczas montażu, ale efekt może być bardzo zadowalający wizualnie.
Najbardziej ambitnym, a zarazem najtrudniejszym do wykonania i ryzykownym sposobem, jest próba stworzenia wizualnie "bezzespoinowego" połączenia bez użycia listwy czy wypełnienia silikonem, tj. docięcie paneli do krawędzi płytek z zachowaniem minimalnej szczeliny, ukrytej pod krawędzią panela. Wymaga to absolutnie idealnego poziomu obu powierzchni, precyzyjnego cięcia obu materiałów, oraz stabilnego podłoża. W rzeczywistości, ze względu na nieuniknioną pracę paneli (rozszerzanie i kurczenie), taka szczelina dylatacyjna musi pozostać, a krawędź panelu może nieestetycznie "dyndać" nad szczeliną lub ocierać się o płytki, prowadząc do uszkodzeń. To rozwiązanie często wygląda dobrze na zdjęciach w katalogach, ale w realnym życiu bywa problematyczne i rzadko stosowane przez profesjonalistów bez profilu ukrytego pod krawędzią. Wymaga nadzwyczajnej precyzji i wiedzy, co zazwyczaj oznacza wyższy koszt robocizny.
Wybór metody łączenia płytek i paneli zależy od wielu czynników: wspomnianej różnicy poziomów (która powinna być zerowa!), grubości szczeliny dylatacyjnej (określanej przez producenta paneli, zazwyczaj 8-15 mm przy ścianie, co przekłada się też na styk z innym materiałem), budżetu, preferowanej estetyki oraz oczekiwanej trwałości rozwiązania. Listwy przejściowe są najbardziej praktyczne i uniwersalne, radzą sobie z niewielkimi niedoskonałościami poziomów i dylatacji. Wypełnienia silikonowe są estetyczne, ale mniej trwałe i wymagają perfekcji wykonania. Korek to naturalna opcja, dobra dla parkietów, ale wymaga starannego zabezpieczenia. Ambitne "bezlistwowe" połączenia to pieśń przyszłości, bardzo trudna w praktyce. Decyzja o sposobach łączenia płytek i paneli powinna być podjęta świadomie, po analizie specyfiki pomieszczenia i materiałów.