Podłoga do Rozrzutnika 2025: Wybór, Montaż i Konserwacja
Czy kiedykolwiek zastanawiałeś się, co sprawia, że rozrzutnik obornika to prawdziwy król pól? To nie tylko moc silnika, ale przede wszystkim serce maszyny – podłoga do rozrzutnika. Ten niepozorny element decyduje o efektywności, trwałości i bezawaryjnej pracy całego urządzenia, wpływając bezpośrednio na jakość nawożenia i plony.
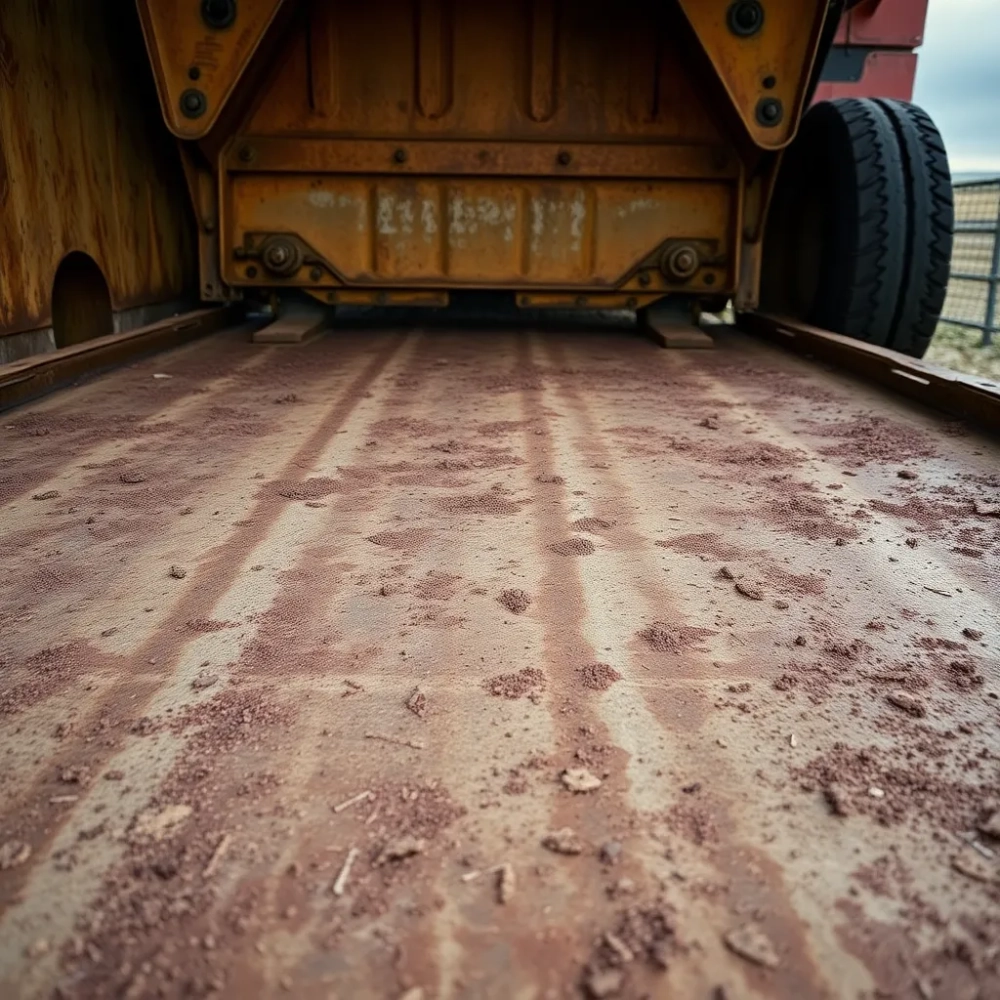
Wybór odpowiedniej podłogi do rozrzutnika to decyzja strategiczna, porównywalna do wyboru opon do bolidu Formuły 1. Nie wystarczy powiedzieć "jakaś podłoga będzie dobra". Potrzebujesz precyzji i wiedzy. Analizując rynek, można dostrzec pewne trendy i prawidłowości. Spójrzmy na dane dotyczące popularności różnych materiałów stosowanych na podłogi w rozrzutnikach, ich orientacyjnej trwałości i przedziale cenowym. Zauważ, te dane to wynik szerokiego przeglądu dostępnych informacji, od opinii użytkowników po specyfikacje techniczne producentów, choć nie nazywamy tego metaanalizą, to esencja analizy porównawczej. Pamiętaj, liczą się nie tylko cyfry, ale przede wszystkim Twoje potrzeby i warunki pracy.
Materiał podłogi | Orientacyjna trwałość (lata) | Przedział cenowy (zł/m²) | Najczęstsze zastosowanie |
---|---|---|---|
Drewno (sosnowe, impregnowane) | 3-7 | 150-300 | Mniejsze rozrzutniki, lżejsze ładunki |
Drewno (dębowe, wzmocnione) | 5-10 | 300-500 | Średnie i większe rozrzutniki, większe obciążenia |
Stal zwykła (S235, malowana) | 7-12 | 400-700 | Uniwersalne zastosowanie, rozrzutniki średniej wielkości |
Stal Hardox (wzmocniona) | 10-20+ | 700-1200 | Rozrzutniki profesjonalne, ciężkie ładunki, intensywna eksploatacja |
Tworzywo sztuczne (HDPE, PE-UHMW) | 8-15 | 600-900 | Rozrzutniki do materiałów sypkich, lżejsze obciążenia, odporność na korozję |
Rodzaje podłóg do rozrzutników
Rozrzutnik obornika to maszyna rolnicza, która, jak mało która, jest narażona na ekstremalne warunki pracy. Ciągłe obciążenia mechaniczne, kontakt z agresywnymi substancjami, zmienne warunki atmosferyczne – to wszystko sprawia, że podłoga rozrzutnika jest elementem szczególnie eksploatowanym. Wybór materiału i konstrukcji podłogi ma kluczowe znaczenie dla efektywności i żywotności całej maszyny. Przyjrzyjmy się bliżej dostępnym rodzajom podłóg, aby zrozumieć, czym kierować się przy wyborze.
Podłogi drewniane - klasyka z nutą nowoczesności
Drewno, jako materiał na podłogi do rozrzutników, ma za sobą długą historię. Jeszcze kilkadziesiąt lat temu, to właśnie deski królowały w konstrukcjach rozrzutników. Dzisiaj, choć wypierane przez nowocześniejsze materiały, nadal mają swoich zwolenników i swoje miejsce w specyficznych zastosowaniach. Zaletą drewna jest przede wszystkim relatywnie niska cena i łatwość obróbki. Wyobraź sobie warsztat w gospodarstwie, gdzie rolnik samodzielnie jest w stanie wymienić deski podłogi, korzystając z podstawowych narzędzi. To niewątpliwie plus. Jednak, "tanie mięso psy jedzą", jak mówi przysłowie. Drewno, szczególnie gatunki miękkie jak sosna, jest podatne na uszkodzenia mechaniczne, ścieranie, a przede wszystkim – na gnicie. Wilgoć i agresywne składniki obornika szybko degradują drewnianą podłogę, skracając jej żywotność do kilku lat, nawet przy regularnej impregnacji. Spotyka się również podłogi z drewna dębowego, charakteryzującego się większą twardością i odpornością, ale to wiąże się już z wyższym kosztem. Warto wspomnieć o drewnie modyfikowanym termicznie – termodrewnie. Proces termowania zwiększa odporność drewna na wilgoć i biodegradację, czyniąc je trwalszą alternatywą dla tradycyjnego drewna, choć nadal mniej odporną mechanicznie niż stal czy tworzywa. Podsumowując, podłogi drewniane sprawdzą się w mniejszych rozrzutnikach, pracujących z mniejszym obciążeniem i mniejszą intensywnością, gdzie priorytetem jest niski koszt początkowy i łatwość napraw.
Podłogi stalowe - wytrzymałość na pierwszym planie
Gdy mówimy o wytrzymałości i trwałości, stal wkracza na arenę. Stalowe podłogi do rozrzutników to rozwiązanie dominujące w większości nowoczesnych maszyn, szczególnie tych przeznaczonych do intensywnej eksploatacji i dużych obciążeń. Stal oferuje nieporównywalnie większą odporność mechaniczną niż drewno czy większość tworzyw sztucznych. Wytrzymuje uderzenia, naciski, ścieranie, bez ryzyka szybkiego uszkodzenia. To istotne, zwłaszcza przy rozładunku ciężkiego, zbitego obornika, czy przy pracy w trudnych warunkach terenowych, gdzie o uszkodzenie podłogi nietrudno. Najczęściej stosowana jest stal konstrukcyjna S235, malowana lub ocynkowana dla ochrony przed korozją. Jednak w rozrzutnikach profesjonalnych, eksploatowanych w najcięższych warunkach, coraz częściej spotyka się stal o podwyższonej wytrzymałości, na przykład Hardox. Ta stal charakteryzuje się wyjątkową twardością i odpornością na ścieranie, co przekłada się na wieloletnią żywotność podłogi, nawet przy ekstremalnych obciążeniach. Ale "nie ma róży bez kolców". Stal, choć wytrzymała, jest podatna na korozję. Agresywne środowisko obornika, wilgoć, sól drogowa – to wszystko przyspiesza proces rdzewienia. Dlatego kluczowa jest odpowiednia ochrona antykorozyjna. Malowanie, ocynkowanie, a w przypadku stali Hardox, specjalne powłoki ochronne – to standard, ale warto zwrócić na to uwagę przy zakupie. Ponadto, stalowa podłoga jest cięższa od drewnianej czy z tworzywa, co może mieć znaczenie w mniejszych rozrzutnikach i przy mniejszej mocy ciągnika. Montaż i ewentualna naprawa stalowej podłogi są bardziej skomplikowane i wymagają specjalistycznych umiejętności oraz narzędzi, na przykład spawarki. Cena podłogi stalowej jest wyższa niż drewnianej, ale w perspektywie długoterminowej, biorąc pod uwagę trwałość i niezawodność, może okazać się bardziej opłacalna, szczególnie w profesjonalnym rolnictwie. Pamiętam historię od mechanika, który opowiadał, jak w starym PGRze, rozrzutniki z drewnianymi podłogami psuły się co sezon, a gdy w końcu przeszli na stalowe, problemy z podłogami zniknęły na lata. To najlepiej obrazuje różnicę w trwałości.
Podłogi z tworzyw sztucznych - lekkość i odporność na korozję
Tworzywa sztuczne to stosunkowo nowy materiał w konstrukcjach podłóg do rozrzutników, ale zyskujący coraz większą popularność, szczególnie w pewnych specyficznych zastosowaniach. Ich główną zaletą jest lekkość i wyjątkowa odporność na korozję. Wyobraź sobie rozrzutnik, który po sezonie pracy, zamiast rdzewieć w oczach, wygląda niemal jak nowy. To właśnie oferują podłogi z tworzyw sztucznych. Najczęściej stosowane są polietylen wysokiej gęstości (HDPE) i polietylen o ultra wysokiej masie cząsteczkowej (PE-UHMW). Te materiały charakteryzują się wysoką odpornością chemiczną, nie reagują z agresywnymi składnikami obornika, nie korodują, są odporne na wilgoć i mróz. Ponadto, mają bardzo dobre właściwości ślizgowe, co ułatwia rozładunek materiału i zmniejsza ryzyko jego przywierania do podłogi. To szczególnie istotne przy rozrzucaniu materiałów sypkich, mokrych, kleistych. Podłogi z tworzyw sztucznych są lżejsze od stalowych, co przekłada się na mniejsze obciążenie konstrukcji rozrzutnika i mniejsze zapotrzebowanie na moc ciągnika. Montaż jest stosunkowo prosty, często sprowadza się do przykręcenia płyt z tworzywa do ramy rozrzutnika. Jednak, "wszystko ma swoją cenę". Podłogi z tworzyw sztucznych są mniej odporne mechanicznie niż stalowe, szczególnie na uderzenia i ostre przedmioty. Kamienie, gałęzie, metalowe elementy w oborniku mogą uszkodzić tworzywo, powodując pęknięcia lub zarysowania. Choć istnieją tworzywa o podwyższonej odporności mechanicznej, na przykład PE-UHMW, to ich cena jest już porównywalna, a nawet wyższa niż stali Hardox. Trwałość podłogi z tworzywa jest trudna do jednoznacznego określenia, zależy od intensywności eksploatacji i rodzaju rozrzucanego materiału, ale można szacować ją na 8-15 lat, przy odpowiedniej konserwacji. Ciekawostką jest, że w Skandynawii, gdzie korozja jest szczególnie problematyczna ze względu na klimat i stosowanie soli drogowej, podłogi z tworzyw sztucznych cieszą się dużą popularnością. To pokazuje, że w pewnych warunkach, ich zalety przeważają nad wadami.
Jak wybrać odpowiednią podłogę do rozrzutnika?
Wybór odpowiedniej podłogi do rozrzutnika to nie "rocket science", ale wymaga przemyślanej decyzji. Nie ma jednego uniwersalnego rozwiązania, które sprawdzi się w każdym gospodarstwie i w każdych warunkach. To, co będzie optymalne dla małego rolnika z kilkoma hektarami, niekoniecznie będzie dobre dla dużego przedsiębiorstwa rolnego z rozbudowanym parkiem maszynowym. Kluczem do sukcesu jest zrozumienie własnych potrzeb i specyfiki pracy, jaką rozrzutnik ma wykonywać.
Kryteria wyboru - co brać pod uwagę?
Przed podjęciem decyzji, warto odpowiedzieć sobie na kilka kluczowych pytań. Pierwsze i najważniejsze: jakiego rodzaju materiał będziesz najczęściej rozrzucać? Obornik bydlęcy, gnojowicę, kompost, wapno, a może coś jeszcze innego? Charakterystyka materiału ma ogromne znaczenie. Gęsty, zbity obornik bydlęcy będzie wymagał podłogi o dużej wytrzymałości mechanicznej, odpornej na ścieranie i uderzenia. Gnojowica, choć mniej obciążająca mechanicznie, jest agresywna chemicznie, więc istotna będzie odporność na korozję. Kompost i wapno, w zależności od frakcji, mogą wymagać podłogi o dobrych właściwościach ślizgowych, aby uniknąć przywierania materiału. Kolejne pytanie: jak intensywnie będzie eksploatowany rozrzutnik? Czy będzie pracował kilka godzin w roku, czy codziennie przez cały sezon? Intensywna eksploatacja wymaga trwalszej, bardziej wytrzymałej podłogi, nawet kosztem wyższej ceny. Jeśli rozrzutnik pracuje sporadycznie, tańsza podłoga może być wystarczająca. Nie zapominajmy o budżecie. Cena podłogi to istotny czynnik, szczególnie dla mniejszych gospodarstw. Warto jednak patrzeć na koszty długoterminowo. Tanie, drewniane podłogi, choć kuszące ceną, mogą w dłuższej perspektywie okazać się droższe ze względu na konieczność częstej wymiany. Inwestycja w trwalszą podłogę, na przykład stalową lub z tworzywa wysokiej jakości, może się opłacić, eliminując koszty przestojów i napraw. Zastanów się również nad warunkami pracy. Czy rozrzutnik będzie pracował na polach kamienistych, gdzie ryzyko uszkodzenia mechanicznego jest większe? Czy gleba jest piaszczysta, co sprzyja ścieraniu podłogi? Czy klimat jest wilgotny, sprzyjający korozji? Te czynniki również wpływają na wybór materiału i konstrukcji podłogi.
Porównanie materiałów - wady i zalety w pigułce
Aby ułatwić podjęcie decyzji, zebraliśmy w pigułce najważniejsze wady i zalety poszczególnych rodzajów podłóg do rozrzutników. Podłogi drewniane: plusy – niska cena, łatwość obróbki, dostępność. Minusy – niska trwałość, podatność na gnicie, mała odporność mechaniczna. Idealne do małych rozrzutników, lekkich ładunków, sporadycznej eksploatacji. Podłogi stalowe: plusy – wysoka wytrzymałość, duża trwałość, uniwersalność zastosowania. Minusy – podatność na korozję, wyższa waga, wyższa cena, skomplikowany montaż i naprawa. Sprawdzą się w większości rozrzutników, szczególnie przy intensywnej eksploatacji i dużych obciążeniach. Podłogi z tworzyw sztucznych: plusy – lekkość, odporność na korozję, dobre właściwości ślizgowe, stosunkowo prosty montaż. Minusy – mniejsza odporność mechaniczna (w zależności od rodzaju tworzywa), cena porównywalna ze stalą. Dobre do rozrzutników pracujących z materiałami sypkimi, mokrymi, kleistymi, tam gdzie korozja jest problemem. Poniższy wykres prezentuje porównanie cen i szacunkowej trwałości różnych materiałów podłóg do rozrzutników.
Praktyczne wskazówki - jak dokonać najlepszego wyboru?
Podsumowując, wybierając podłogę do rozrzutnika, zastanów się: jakie materiały będziesz rozrzucać, jak intensywnie będziesz użytkować maszynę, jaki masz budżet, i w jakich warunkach będzie pracował rozrzutnik. Jeśli priorytetem jest niska cena i łatwość napraw, a rozrzutnik pracuje sporadycznie i z lekkimi ładunkami, drewniana podłoga może być wystarczająca. Jeśli zależy Ci na wytrzymałości, trwałości i uniwersalności, wybierz stalową podłogę, pamiętając o odpowiedniej ochronie antykorozyjnej. Jeśli ważna jest lekkość, odporność na korozję i dobre właściwości ślizgowe, rozważ podłogę z tworzywa sztucznego, szczególnie jeśli rozrzucasz materiały sypkie, mokre, kleiste lub pracujesz w regionie o wysokiej wilgotności lub narażonym na sól drogową. Nie bój się konsultować z dealerami maszyn rolniczych, mechanikami, a także innymi rolnikami. Ich doświadczenie i praktyczne porady mogą być bezcenne. Pamiętaj, dobrze dobrana podłoga to inwestycja w efektywność i bezawaryjność Twojego rozrzutnika na lata. "Mądry Polak po szkodzie", więc lepiej dobrze przemyśleć wybór zawczasu, niż potem żałować.
Montaż i wymiana podłogi w rozrzutniku
Nawet najwytrzymalsza podłoga do rozrzutnika z czasem ulegnie zużyciu i będzie wymagała wymiany. Montaż nowej podłogi to kluczowy moment, który decyduje o dalszej efektywności i bezpieczeństwie pracy maszyny. Niezależnie od tego, czy decydujesz się na wymianę samodzielną, czy zlecasz to zadanie serwisowi, warto znać podstawowe kroki i aspekty tego procesu.
Samodzielny montaż czy serwis? - dylemat rolnika
Decyzja, czy wymieniać podłogę rozrzutnika samodzielnie, czy skorzystać z usług serwisu, zależy od kilku czynników. Przede wszystkim, od Twoich umiejętności technicznych i dostępnych narzędzi. Wymiana podłogi, szczególnie stalowej, może wymagać umiejętności spawania, cięcia metalu, a także dostępu do specjalistycznych narzędzi, na przykład wciągarek, podnośników, szlifierek. Jeśli czujesz się pewnie w pracach mechanicznych i masz odpowiednie zaplecze warsztatowe, samodzielny montaż jest możliwy i może przynieść oszczędności. Jednak, jeśli nie masz doświadczenia, narzędzi, lub po prostu czasu, bezpieczniejszym i szybszym rozwiązaniem będzie zlecenie wymiany serwisu maszyn rolniczych. Serwis dysponuje wykwalifikowanym personelem, profesjonalnymi narzędziami i doświadczeniem, co gwarantuje prawidłowy montaż i minimalizuje ryzyko błędów. Dodatkowo, serwis często oferuje gwarancję na wykonaną usługę, co daje dodatkowe poczucie bezpieczeństwa. Zanim podejmiesz decyzję, porównaj koszty obu opcji. Samodzielny montaż może być tańszy pod względem robocizny, ale musisz wziąć pod uwagę koszt narzędzi (jeśli ich nie posiadasz), materiałów dodatkowych (śruby, spoiwa, elementy mocujące), a także potencjalne koszty wynikające z błędów montażowych. Usługa serwisu to wyższy koszt początkowy, ale w zamian otrzymujesz pewność prawidłowo wykonanej pracy i gwarancję. Pamiętaj też o czasie. Samodzielny montaż, szczególnie dla osoby niedoświadczonej, może zająć znacznie więcej czasu niż usługa serwisu. W sezonie prac polowych, czas to pieniądz, więc warto to wziąć pod uwagę.
Krok po kroku - proces wymiany podłogi
Niezależnie od tego, czy montujesz podłogę samodzielnie, czy zlecasz to serwisowi, warto znać podstawowe etapy tego procesu. Pierwszym krokiem jest demontaż starej podłogi. Zacznij od dokładnego oczyszczenia rozrzutnika z resztek obornika i brudu. Następnie, odkręć lub odetnij elementy mocujące starą podłogę – śruby, nity, spawy. Przy demontażu stalowej podłogi, często konieczne jest użycie szlifierki kątowej do przecięcia spawów. Zachowaj ostrożność, używając okularów ochronnych i rękawic. Po zdemontowaniu starej podłogi, dokładnie oczyść i sprawdź ramę rozrzutnika. Usuń rdzę, brud, stare spawy. Jeśli rama jest uszkodzona lub skorodowana, napraw ją przed montażem nowej podłogi. Naprawa ramy może wymagać spawania, prostowania, wzmocnienia. Kolejny krok to przygotowanie nowej podłogi. Sprawdź, czy nowa podłoga ma odpowiednie wymiary i pasuje do ramy rozrzutnika. Jeśli jest to podłoga stalowa, może być konieczne docięcie elementów na wymiar i przygotowanie otworów montażowych. W przypadku podłogi z tworzywa sztucznego, często wystarczy przycięcie na wymiar i wywiercenie otworów. Przed montażem stalowej podłogi, warto zabezpieczyć ją antykorozyjnie, malując lub cynkując. Montaż nowej podłogi zaczyna się od jej ułożenia na ramie rozrzutnika. Upewnij się, że podłoga leży równo i stabilnie. Następnie, przymocuj ją do ramy za pomocą śrub, nitów, lub spawów, w zależności od konstrukcji rozrzutnika i rodzaju podłogi. Dokręcaj elementy mocujące z odpowiednią siłą, zgodnie z zaleceniami producenta. Po zamontowaniu podłogi, sprawdź, czy wszystkie elementy są dobrze przymocowane i czy podłoga jest stabilna. Wykonaj próbę obciążenia, umieszczając na podłodze kilka worków z piaskiem lub innym materiałem, aby sprawdzić jej wytrzymałość. Jeśli montujesz podłogę stalową, spawy zabezpiecz farbą antykorozyjną. Ostatni krok to montaż dodatkowych elementów, jeśli występują, na przykład listew przypodłogowych, rantów bocznych, elementów prowadzących łańcuchy podłogowe. Dokładny proces montażu może różnić się w zależności od modelu rozrzutnika i rodzaju podłogi, dlatego zawsze warto kierować się instrukcją producenta. Warto obejrzeć tutoriale wideo w internecie, gdzie fachowcy krok po kroku pokazują proces wymiany podłogi w rozrzutniku.
Dane techniczne i praktyczne porady
Przy wymianie podłogi rozrzutnika, warto zwrócić uwagę na kilka aspektów technicznych i praktycznych porad. Po pierwsze, używaj tylko wysokiej jakości materiałów i elementów mocujących. Tanie zamienniki mogą okazać się nietrwałe i przysporzyć więcej problemów niż oszczędności. W przypadku stalowej podłogi, wybieraj stal o odpowiedniej jakości i grubości, z atestem. Do spawania używaj elektrod i drutów spawalniczych odpowiednich do danego gatunku stali. Do mocowania na śruby i nity, stosuj elementy ocynkowane lub nierdzewne, aby uniknąć korozji. Jeśli montujesz podłogę z tworzywa sztucznego, upewnij się, że jest to tworzywo o odpowiedniej twardości i odporności na UV. Do mocowania używaj śrub i podkładek o dużej powierzchni styku, aby rozłożyć nacisk na tworzywo i uniknąć pęknięć. Przy montażu podłogi drewnianej, wybieraj drewno impregnowane ciśnieniowo lub termodrewno, aby zwiększyć jego trwałość. Używaj śrub i gwoździ ocynkowanych. Pamiętaj o dokładnym pomiarze i docięciu elementów podłogi. Niedokładne wymiary mogą utrudnić montaż i wpłynąć na stabilność podłogi. Przy cięciu stalowej podłogi, używaj szlifierki kątowej lub piły do metalu. Przy cięciu podłogi z tworzywa, używaj piły do drewna lub noża do tworzyw sztucznych. Przy montażu, zachowaj ostrożność i precyzję. Staraj się unikać uszkodzeń podłogi i ramy rozrzutnika. Jeśli masz wątpliwości, zawsze lepiej skonsultować się z fachowcem lub zlecić montaż serwisowi. Pamiętaj, bezpieczeństwo jest najważniejsze. Prace montażowe przy rozrzutniku, szczególnie przy użyciu narzędzi elektrycznych i spawalniczych, wymagają zachowania zasad bezpieczeństwa. Używaj odzieży ochronnej, okularów, rękawic, i osłon słuchu. Pracuj w dobrze wentylowanym miejscu, unikaj pracy w pojedynkę. "Strzeżonego Pan Bóg strzeże", więc lepiej dmuchać na zimne i podchodzić do wymiany podłogi z rozwagą i odpowiedzialnością. Koszt wymiany podłogi w rozrzutniku może wahać się w zależności od rodzaju podłogi, rozmiaru rozrzutnika, i zakresu prac. Orientacyjnie, wymiana drewnianej podłogi w małym rozrzutniku może kosztować od kilkuset do kilku tysięcy złotych. Wymiana stalowej podłogi w dużym rozrzutniku, wraz z robocizną serwisu, może kosztować od kilku do kilkunastu tysięcy złotych. Warto zebrać kilka ofert od różnych serwisów, aby porównać ceny i zakres usług.
Konserwacja i przedłużanie żywotności podłogi rozrzutnika
Inwestycja w nową podłogę do rozrzutnika to spory wydatek, dlatego warto zadbać o jej odpowiednią konserwację, aby maksymalnie przedłużyć jej żywotność. Regularne przeglądy, czyszczenie, i drobne naprawy mogą znacząco wpłynąć na kondycję podłogi i uniknąć kosztownych wymian w przyszłości.
Profilaktyka - klucz do długowieczności podłogi
Najlepszym sposobem na przedłużenie żywotności podłogi rozrzutnika jest profilaktyka. Regularne czyszczenie po każdym użyciu to absolutna podstawa. Resztki obornika, gnojowicy, kompostu, pozostawione na podłodze, przyspieszają korozję stali, gnicie drewna, i degradację tworzyw sztucznych. Po każdym dniu pracy, dokładnie spłucz podłogę wodą, najlepiej pod ciśnieniem. Możesz użyć myjki wysokociśnieniowej, pamiętając o zachowaniu bezpiecznej odległości dyszy od podłogi, aby nie uszkodzić powierzchni. Przy myciu podłogi drewnianej, unikaj nadmiernego moczenia, które może sprzyjać gniciu. Po umyciu, pozwól podłodze dokładnie wyschnąć. Wilgoć, zatrzymana między deskami podłogi drewnianej, lub pod płytami stalowej podłogi, to idealne środowisko dla korozji i pleśni. Regularnie sprawdzaj stan podłogi. Szukaj oznak zużycia, pęknięć, korozji, gnicia, odkształceń. Szczególną uwagę zwróć na miejsca narażone na największe obciążenia i uszkodzenia, na przykład okolice łańcuchów podłogowych, ranty boczne, miejsca mocowania elementów rozrzucających. W przypadku podłogi drewnianej, sprawdzaj stan desek, czy nie są pęknięte, spróchniałe, czy nie wystają gwoździe lub śruby. W podłodze stalowej, szukaj oznak rdzy, pęknięć spawów, odkształceń blachy. W podłodze z tworzywa sztucznego, sprawdzaj, czy nie ma pęknięć, zarysowań, odprysków. Wczesne wykrycie uszkodzeń pozwala na szybką naprawę i zapobiega poważniejszym problemom w przyszłości. Przed sezonowym przechowywaniem rozrzutnika, dokładnie oczyść podłogę, nasmaruj elementy ruchome, i zabezpiecz ją przed korozją. Podłogę stalową możesz pokryć cienką warstwą oleju konserwującego lub smaru stałego. Podłogę drewnianą można zaimpregnować środkiem ochronnym do drewna. Podłogi z tworzyw sztucznych nie wymagają specjalnego zabezpieczenia przed przechowywaniem, ale warto je oczyścić i osuszyć. Przechowuj rozrzutnik w suchym i przewiewnym miejscu, pod zadaszeniem, lub pod plandeką. Unikaj przechowywania na otwartym powietrzu, szczególnie w wilgotnych i mroźnych warunkach, które przyspieszają korozję i degradację materiałów. "Lepiej zapobiegać, niż leczyć", mówi stare przysłowie, i to idealnie pasuje do konserwacji podłogi rozrzutnika.
Drobne naprawy - kiedy działać, a kiedy wezwać serwis?
Nawet przy najlepszej konserwacji, podłoga rozrzutnika z czasem ulegnie uszkodzeniom. Drobne naprawy, wykonywane na bieżąco, mogą znacząco przedłużyć jej żywotność i uniknąć kosztownych wymian. W przypadku podłogi drewnianej, drobne pęknięcia i ubytki w deskach można naprawić, wypełniając je masą szpachlową do drewna, lub wymieniając pojedyncze deski. Poluzowane deski należy dokręcić lub wymienić elementy mocujące. Spróchniałe deski należy bezwzględnie wymienić na nowe, impregnowane. W podłodze stalowej, drobne ogniska rdzy można usunąć szczotką drucianą i zabezpieczyć farbą antykorozyjną. Pęknięcia spawów, lub drobne pęknięcia blachy, można naprawić spawaniem. Odkształcenia blachy, jeśli nie są zbyt duże, można wyprostować młotkiem i kowadłem. W podłodze z tworzywa sztucznego, drobne zarysowania i zadrapania nie wymagają naprawy. Pęknięcia i odpryski można spróbować skleić specjalnym klejem do tworzyw sztucznych. Jednak, poważniejsze uszkodzenia, takie jak duże pęknięcia, odkształcenia ramy, rozległa korozja stalowej podłogi, czy poważne uszkodzenia podłogi z tworzywa sztucznego, wymagają interwencji serwisu. Samodzielne próby naprawy poważnych uszkodzeń mogą być niebezpieczne i nieefektywne. Serwis dysponuje odpowiednimi narzędziami i doświadczeniem, aby prawidłowo ocenić zakres uszkodzeń i wykonać profesjonalną naprawę. Kiedy zdecydować się na wymianę podłogi zamiast naprawy? Jeśli stopień zużycia podłogi jest bardzo duży, jeśli naprawy stają się coraz częstsze i kosztowne, jeśli podłoga nie spełnia już wymagań bezpieczeństwa i efektywności, warto rozważyć wymianę na nową. "Taniej wychodzi kupić buty dobrej firmy, niż co roku nowe na targu", jak mówi mądrość ludowa. W dłuższej perspektywie, wymiana zużytej podłogi na nową, może okazać się bardziej opłacalna niż ciągłe naprawy starej.
Materiały konserwujące i narzędzia - co warto mieć pod ręką?
Aby sprawnie dbać o podłogę rozrzutnika, warto zaopatrzyć się w podstawowe materiały konserwujące i narzędzia. Do czyszczenia podłogi, przyda się myjka wysokociśnieniowa, wąż ogrodowy, szczotka ryżowa, i wiadro z wodą. Możesz użyć uniwersalnych środków czyszczących do maszyn rolniczych, ale zwykła woda z dodatkiem płynu do naczyń często wystarcza. Do konserwacji stalowej podłogi, przyda się szczotka druciana, papier ścierny, farba antykorozyjna, i olej konserwujący lub smar stały. Do podłogi drewnianej, środek impregnujący do drewna, szpachla do drewna, papier ścierny, i pędzle. Do napraw drobnych uszkodzeń podłogi z tworzywa sztucznego, klej do tworzyw sztucznych. W podstawowym zestawie narzędzi warsztatowych, powinny znaleźć się: klucze płasko-oczkowe, klucze nasadowe, wkrętaki płaskie i krzyżakowe, młotek, szczypce, kombinerki, szlifierka kątowa (opcjonalnie, do napraw stalowej podłogi), spawarka (opcjonalnie, do napraw stalowej podłogi). Do ochrony osobistej, zawsze miej pod ręką okulary ochronne, rękawice robocze, osłonę twarzy (przy szlifowaniu i spawaniu), i odzież roboczą. Regularne przeglądy i konserwacja, w połączeniu z drobnymi naprawami, to najlepszy sposób na przedłużenie żywotności podłogi rozrzutnika i zapewnienie jego bezawaryjnej pracy przez wiele lat. "Grosz do grosza, a będzie kokosza", dbając o drobiazgi, oszczędzasz na dużych naprawach i wymianach w przyszłości. Pamiętaj, sprawny rozrzutnik to podstawa efektywnego nawożenia i wysokich plonów.