Ile zapasu na płytki, parkiet i panele doliczyć przy wylewce? Poradnik 2025
Pytanie, ile zostawić na płytki parkiet i panele przy wylewkach, spędza sen z powiek wielu inwestorom, niczym nierozwiązana szarada na finiszu budowy czy remontu. Odpowiedź, choć może wydawać się skomplikowana, jest w gruncie rzeczy prostsza niż przepis na babkę, a brzmi: ile zostawić na płytki parkiet i panele przy wylewkach powinno być ściśle powiązane z wyborem konkretnego materiału oraz jego przeznaczenia w danym pomieszczeniu. Nie ma jednej magicznej liczby pasującej do wszystkiego, a ignorowanie tego detalu może prowadzić do poważnych komplikacji i niepotrzebnych kosztów.
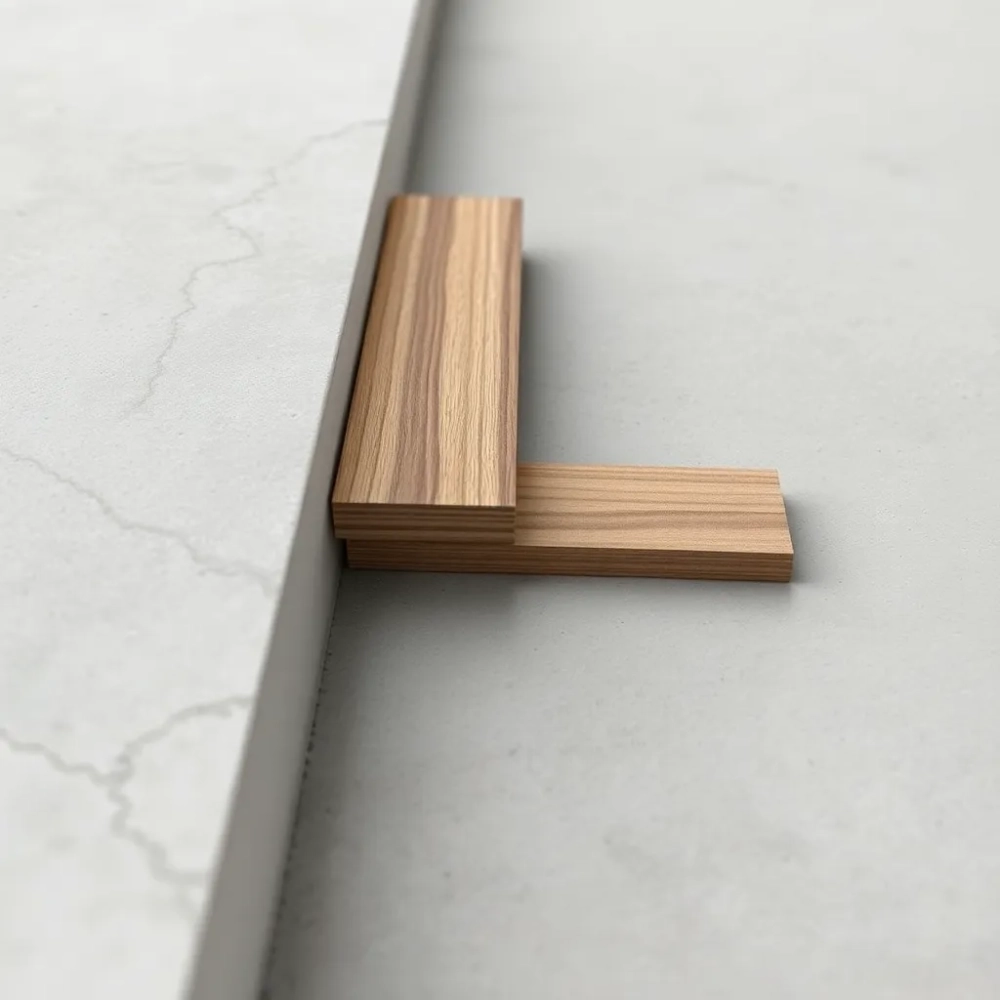
Wiele danych empirycznych zebranych na przestrzeni lat przez fachowców jasno pokazuje, że typowa utrata materiału podczas standardowego montażu podłóg waha się w określonych przedziałach. Dla najpopularniejszych wyborów, takich jak panele laminowane, prostokątne płytki ceramiczne kładzione w prosty wzór oraz deski parkietowe montowane w jodełkę, możemy zaobserwować różnice wynikające bezpośrednio z natury samych materiałów oraz specyfiki ich cięcia i dopasowania. Poniższe dane prezentują szacunkowy rozrzut procentowy, jaki typowo odnotowuje się jako odpad lub rezerwa konieczna do płynnego montażu bez przestojów wynikających z braku materiału, stanowiąc swojego rodzaju punkt odniesienia dla planowania zakupów.
Materiał Podłogowy | Typowy Procent Zapasu (wzór prosty/podstawowy) | Typowy Procent Zapasu (wzór złożony/skomplikowane cięcia) | Główne Powody Wymagania Zapasu |
---|---|---|---|
Panele Laminowane/Winyl (montaż na klik) | 5-8% | 8-12% (np. jodełka, skosy, duża liczba wcięć) | Docinanie na krańcach, uszkodzenia podczas transportu/montażu, nietypowy kształt pomieszczeń |
Płytki Ceramiczne/Gres (format standardowy, układ prosty) | 5-10% | 10-15% (np. płytki hexagonalne, układ diagonalny, duże formaty, mozaiki, dużo docinek przy ościeżnicach, kominach itp.) | Cięcie, ryzyko pęknięcia podczas cięcia/transportu, skomplikowane kształty płytek/pomieszczeń |
Parkiet (deski lite/warstwowe) | 7-10% | 10-15% (np. jodełka francuska, cegiełka, duże formaty) | Docinanie, konieczność selekcji niektórych desek (np. ze względu na sęki), format i wzór układania |
Powyższe dane nie są sztywnymi regułami, a jedynie praktycznymi wskazówkami wynikającymi z doświadczeń pokoleń montażystów i inżynierów budownictwa. Każdy projekt, niczym odrębne dzieło sztuki, ma swoje indywidualne wymagania i pułapki. Procentowa rezerwa, choć pozornie niewielka, staje się kluczowym zabezpieczeniem przed nieprzewidzianymi zdarzeniami, pozwalając zachować płynność prac i uniknąć kosztownych przestojów. Pamiętajmy, że diabeł tkwi w szczegółach, a te szczegóły w przypadku podłóg często objawiają się koniecznością idealnego dopasowania każdego elementu.
Dlaczego warto doliczyć zapas materiału na podłogę?
Doliczenie zapasu materiału na podłogę to jak posiadanie asa w rękawie w grze o idealnie wykończone wnętrze. To nie jest fanaberia ani marketingowy chwyt, a twarda kalkulacja wynikająca z realiów pracy na placu budowy czy podczas remontu. Każdy, kto choć raz mierzył się z układaniem podłogi wie, że proces ten rzadko kiedy przebiega w linii prostej, bez niespodzianek.
Wyobraź sobie sytuację: praca wre, ekipa montażowa ma wolny termin na ostatnie dni, a Ty stajesz przed dylematem – brakuje kilku kluczowych elementów. Może to być ostatni rząd paneli do docięcia w nieregularnym korytarzu, brakująca płytka do dokończenia łazienkowego narożnika albo kilka desek parkietu niezbędnych, by zamknąć wzór w salonie. Czasami winna jest połamana płytka z transportu, innym razem błąd w cięciu, a bywa też, że pomieszczenie okazało się mieć więcej krzywizn niż zakładał projekt. Nawet najbardziej precyzyjny pomiar i dokładny plan nie wyeliminują ryzyka stuprocentowo.
Konsekwencje braku kilku sztuk są wielorakie i potrafią solidnie uderzyć po kieszeni oraz w nerwy. Po pierwsze, mamy przestój w pracy ekipy. Ich czas kosztuje, a opóźnienia w harmonogramie potrafią lawinowo pociągać za sobą kolejne problemy z innymi fachowcami czekającymi na swoją kolej. Płacisz za dni, kiedy stoją bezczynnie, czekając na materiał, który musisz szybko dokupić.
Po drugie, szybki zakup brakującego elementu nie zawsze jest prosty. Co jeśli kupiłeś materiał z wyprzedaży? Co jeśli to konkretna partia o subtelnie innym odcieniu, która nie jest już dostępna? Materiały wykończeniowe, zwłaszcza te naturalne jak drewno czy płytki ceramiczne, często różnią się między partiami produkcyjnymi kolorem, odcieniem czy kalibracją. Dokupienie małej ilości z innej serii może skończyć się widoczną różnicą na gotowej podłodze, rujnując cały estetyczny efekt.
Wreszcie, dochodzi koszt logistyki. Poświęcasz czas na poszukiwanie brakującego materiału, nierzadko w kilku sklepach. Płacisz za dodatkowy transport, często za kilka sztuk, co w przeliczeniu na jednostkę wychodzi znacznie drożej niż przy zakupie hurtowym. Zapas, nawet te skromne 5%, to inwestycja, która minimalizuje te wszystkie ryzyka. Stanowi poduszkę bezpieczeństwa, która pozwala pracować bez stresu i nagłych improwizacji. Zapobiega sytuacji, w której brak jednego metra kwadratowego paneli zatrzymuje wykończenie salonu wartego dziesiątki tysięcy złotych. Dlatego tak ważne jest, aby zostawić na płytki parkiet i panele przy wylewkach ten niewielki, ale kluczowy naddatek.
Szczególnie newralgiczne stają się projekty z nietypowymi wzorami układania, takimi jak jodełka francuska dla parkietu czy skomplikowane cięcia dla wielkoformatowych płytek ceramicznych wokół licznych przeszkód architektonicznych, jak słupy czy nieregularne wnęki. W takich scenariuszach, procentowy odpad materiału naturalnie wzrasta, a ryzyko popełnienia błędu przy cięciu, którego nie da się już naprawić, jest wyższe. Każdy milimetr ma znaczenie, a jedno niewłaściwe cięcie oznacza bezużyteczny kawałek materiału, który ląduje w koszu. Dlatego rozsądne planowanie zakłada uwzględnienie tego już na etapie zamawiania, by uniknąć późniejszej frustracji i biegania po sklepach w poszukiwaniu jednej, jedynej sztuki, która dokończy dzieło.
Innym czynnikiem, o którym warto pamiętać, jest naturalne uszkodzenie materiału podczas transportu lub przechowywania. Choć sprzedawcy dokładają wszelkich starań, by materiał dotarł nienaruszony, palety płytek czy paczki paneli przejeżdżają setki kilometrów, bywają przenoszone, a każdy stuk czy upadek może skutkować pęknięciem płytki czy uszkodzeniem pióra/wpustu w panelu czy desce parkietu. Posiadając zapas, takie drobne straty nie paraliżują pracy. Możesz po prostu sięgnąć po kolejną sztukę z bufora. W przeciwnym razie, nawet jedno takie uszkodzenie na końcu prac może oznaczać poważny problem i konieczność wstrzymania montażu. W ten sposób, pozornie niewielki koszt zakupu dodatkowego materiału, staje się realnym zabezpieczeniem przed znacznie wyższymi, ukrytymi kosztami, takimi jak płacenie za dni postojowe ekipy, dodatkowy transport czy ryzyko kompromisu na jakości estetycznej z powodu różnic w partii materiału. To po prostu mądra inwestycja.
Ile procent zapasu doliczyć dla płytek, a ile dla paneli i parkietu?
Podchodząc do tematu ilości materiału, stajemy przed swoistą sztuką optymalizacji. Chcemy mieć go wystarczająco, by praca szła sprawnie i bez komplikacji, ale też nie przesadzić z nadmiernymi zapasami, które później zalegają w garażu czy piwnicy, stanowiąc martwy koszt. Klasyczna zasada mówi, że lepiej mieć za dużo niż za mało, a w praktyce oznacza to doliczenie do wyliczonej powierzchni podłogi od około 5% do nawet 15% zapasu materiału. Konkretna wartość tego bufora bezpieczeństwa zależy jednak od specyfiki materiału i wzoru jego ułożenia.
Dla płytek ceramicznych czy gresu, zwłaszcza tych o regularnych, prostokątnych kształtach układanych w klasycznym, prostym wzorze (równolegle lub prostopadle do ścian), zazwyczaj wystarczy zapas na poziomie 5-10%. Ryzyko pęknięcia podczas transportu czy cięcia, zwłaszcza w przypadku dużych formatów (powyżej 60x60 cm, 60x120 cm), gdzie naprężenia są większe, sugeruje skłanianie się ku wyższemu końcowi tego przedziału (np. 8-10%). Pamiętajmy, że cięcie gresu jest niczym taniec z ostrym nożem – wymaga precyzji i wprawy, a mimo to czasami materiał po prostu "nie współpracuje", pęka nie tam, gdzie powinien. Dotyczy to w szczególności gresu szkliwionego lub z delikatną fakturą.
Sytuacja radykalnie się zmienia, gdy wchodzimy w bardziej skomplikowane projekty z płytkami. Układ diagonalny (w karo) dla kwadratowych lub prostokątnych płytek natychmiast zwiększa ilość wymaganych docinek, a co za tym idzie, potencjalnego odpadu. W tym przypadku zapas na poziomie 10-15% to rozsądne minimum. Gdy na scenę wchodzą płytki o nietypowych kształtach – heksagony, oktagony, "rybie łuski", czy wreszcie drobna mozaika na siatce – liczba cięć, zwłaszcza tych pod kątem i wzdłuż krzywizn, eksploduje. W takich sytuacjach zapas na poziomie nawet 15-20% nie jest niczym niezwykłym, a wręcz wskazanym, aby zapewnić płynność i precyzję prac bez ryzyka braków na finiszu.
Jeśli chodzi o panele laminowane czy winylowe montowane na klik, zapas materiału jest zazwyczaj mniejszy niż dla płytek, gdyż materiał ten jest prostszy w cięciu i rzadziej ulega uszkodzeniom wewnątrz paczki. Przy standardowym układaniu wzdłuż najdłuższej ściany pomieszczenia (tzw. układ deska w deska), zapas rzędu 5-8% jest z reguły wystarczający. Ta ilość pozwala na swobodne docinanie desek na początku i końcu rzędów oraz kompensuje ewentualne uszkodzenia rantów podczas montażu czy transportu. Panele winylowe, ze względu na większą elastyczność i mniejszą podatność na odpryski, czasami wymagają minimalnie niższego zapasu, ale różnica ta jest marginalna w porównaniu do zmiennych związanych z kształtem pomieszczenia czy wzorem układania.
Tak jak w przypadku płytek, również przy panelach skomplikowane wzory i kształt pomieszczeń dyktują wyższy procent zapasu. Jeśli panele mają być układane diagonalnie (pod kątem 45 stopni do ścian), konieczność docinania wszystkich boków pomieszczenia znacznie zwiększa ilość odpadu. Zapas w takim przypadku powinien wzrosnąć do 8-12%. Bardziej fantazyjne wzory, takie jak panele układane w jodełkę, mimo że technika montażu jest nieco inna, również generują więcej odpadu z docinek końcowych, co oznacza potrzebę zapasu rzędu 10-15%. Warto pamiętać, że im więcej nieregularnych kształtów w pomieszczeniu (uskoki ścian, kolumny, wykusze), tym więcej precyzyjnych docinek będzie potrzebnych, a każdy taki punkt to potencjalny wzrost odpadu materiałowego, co wymaga większego bufora w zakupionym zapasie.
Deski parkietowe (lite lub warstwowe) pod względem zapasu plasują się gdzieś pomiędzy płytkami a panelami, a ich wymagania zależą mocno od systemu montażu (klejony czy na klik, jeśli jest to parkiet warstwowy) oraz, co najważniejsze, od wzoru układania. Przy prostym układaniu desek równolegle do ścian, zapas 7-10% jest standardem. Pozwala on na swobodne docinanie końcowych elementów i uwzględnia ewentualną konieczność selekcji pojedynczych desek, które mogą mieć np. niechciane sęki czy naturalne wady drewna. Parkiet lity zazwyczaj pozwala na pewną tolerancję w docinaniu i szlifowaniu, ale ryzyko rozszczepienia deski podczas cięcia czy montażu też istnieje.
Wzory parkietowe takie jak klasyczna jodełka (pod kątem 90 stopni), jodełka francuska (pod kątem 45 lub 60 stopni), cegiełka, kwadraty czy wzory złożone (np. pałacowe) drastycznie zwiększają ilość odpadu. W jodełce, zwłaszcza francuskiej z frezowaniem na pióro-wpust na końcach, każda docinka jest precyzyjna i często obejmuje cięcie pod kątem na pile. W tych przypadkach zapas na poziomie 10-15% to absolutna konieczność, a w bardzo skomplikowanych projektach z wieloma narożnikami i kolumnami, nawet 15-20% nie powinno dziwić. W przypadku parkietów naturalnych, dochodzi jeszcze aspekt selekcji i sortowania drewna. Część desek może zostać odrzucona ze względu na sęki, kolor czy inne naturalne cechy, które nie pasują do zamierzonego efektu, co również powinno być uwzględnione w ilości zamawianego materiału.
Oprócz samego rodzaju materiału i wzoru, wpływ na wymagany zapas ma także kilka innych czynników, które warto przeanalizować. Pierwszym jest kształt i wielkość pomieszczenia. Im bardziej nieregularny kształt (dużo załamań, wnęk, kolumn), tym więcej będzie potrzebnych docinek, a co za tym idzie, większy odpad. Drugi czynnik to format samego materiału. Układanie wielkoformatowych płytek czy paneli w małym pomieszczeniu z wieloma przeszkodami generuje znacznie więcej odpadu niż ten sam materiał w dużej, otwartej przestrzeni. Zapas materiału pozwala na elastyczność podczas montażu i jest najlepszym ubezpieczeniem przed problemami wynikającymi z jego niedoboru.
Ostatnim, choć nie mniej ważnym, czynnikiem jest poziom doświadczenia osoby układającej podłogę. Choć nawet najbardziej wprawny fachowiec generuje pewien procent odpadu, osoba bez doświadczenia może popełniać więcej błędów w cięciu lub niszczyć materiał podczas montażu. Zwiększenie zapasu o kilka procent może zminimalizować ryzyko problemów w takim przypadku. Podsumowując, choć 5% to często dobry punkt wyjścia dla prostych projektów z panelami czy prostokątnymi płytkami, ile zostawić na płytki parkiet i panele przy wylewkach w rzeczywistości zależy od szczegółowej analizy projektu, w tym wzoru układania, formatu materiału, kształtu pomieszczeń i własnego (lub wynajętej ekipy) doświadczenia, a zwiększenie zapasu w przypadku komplikacji to rozsądne i opłacalne posunięcie.
Kluczowy czynnik: Czas schnięcia wylewki przed montażem podłogi
Kładzenie jakiejkolwiek podłogi na niedostatecznie suchej wylewce jest jak rysowanie na wilgotnym papierze – nie tylko twoje dzieło nie wyjdzie zgodnie z planem, ale także cała koncepcja może się rozpaść. Aspekt, który często jest pomijany w gorączce końcowych prac, to odpowiedni czas schnięcia wylewki. Niezależnie od tego, czy mamy do czynienia z wylewkami betonowymi, cementowymi, czy anhydrytowymi, wymagają one odpowiedniej pielęgnacji i, co najważniejsze, czasu przed przystąpieniem do kolejnych etapów wykończenia wnętrz.
Montaż podłogi na wilgotnym podłożu to prosta droga do katastrofy. Panele laminowane czy winylowe spuchną i wypaczą się. Deski parkietowe (lite czy warstwowe) będą absorbować wilgoć, prowadząc do wybrzuszeń, odspojenia od podłoża czy pękania. Klejone płytki ceramiczne mogą stracić przyczepność, fugi mogą się wykruszać, a co gorsza, wilgoć uwięziona pod nieprzepuszczalnym materiałem staje się idealnym środowiskiem dla rozwoju pleśni i grzybów, co ma bezpośrednie konsekwencje zdrowotne i estetyczne. Mówiąc wprost: niecierpliwość w kwestii schnięcia wylewki kosztuje krocie i przysparza masę problemów.
Ogólna, często powtarzana zasada dla wylewek cementowych mówi, że na każdy centymetr grubości wylewki należy przeznaczyć określony czas schnięcia, przy czym czas ten rośnie nieliniowo wraz z grubością. Przykładowo, często przyjmuje się, że pierwsze 4 cm wylewki schną około 1 tygodnia na każdy centymetr. Natomiast każdy kolejny centymetr powyżej 4 cm wymaga już około 2 tygodni na centymetr. Przywołując studium przypadku z życia wzięte: rozważmy podłogę cementową o grubości 6 cm. Według tej zasady, potrzebuje ona około 4 tygodni schnięcia dla pierwszych 4 cm (4 cm * 1 tydzień/cm) oraz 4 tygodnie dla pozostałych 2 cm (2 cm * 2 tygodnie/cm), co daje łącznie 8 tygodni schnięcia. Z kolei, dla wylewki o grubości 7 cm, możemy mówić już o 4 tygodniach dla pierwszych 4 cm i 6 tygodniach dla kolejnych 3 cm (3 cm * 2 tygodnie/cm), co daje w sumie 10 tygodni schnięcia! Przy 8 cm wylewki to już 12 tygodni (4*1 + 4*2).
Wylewki anhydrytowe schną szybciej, zazwyczaj przyjmuje się około 1 tygodnia na każdy centymetr grubości wylewki, aż do maksymalnej grubości 4 cm. Dla grubszych wylewek anhydrytowych czas ten również rośnie, ale w nieco innej proporcji, np. powyżej 4 cm przyjmuje się 2 tygodnie na cm. Wylewka o grubości 5 cm potrzebowałaby zatem ok. 6 tygodni (4cm*1 tydz/cm + 1cm*2 tydz/cm). Pamiętajmy jednak, że te wartości to tylko szacunki i realny czas schnięcia zależy od wielu czynników zewnętrznych. Naprawdę dużo czasu, ale każdy, kto zna się na budownictwie wie, że pośpiech w tym przypadku to zły doradca.
Najpewniejszym sposobem na sprawdzenie gotowości wylewki do położenia podłogi jest pomiar wilgotności metodą karbidową (CM). Profesjonalne firmy montażowe dysponują odpowiednim sprzętem i wykonują taki pomiar. Dla wylewek cementowych pod panele, parkiet klejony czy płytki, dopuszczalna wilgotność resztkowa wylewki cementowej nie powinna przekraczać 2,0 CM%. Dla wylewek z ogrzewaniem podłogowym ten próg jest jeszcze niższy i wynosi 1,5 CM%. W przypadku wylewek anhydrytowych, wartości są inne: 0,5 CM% bez ogrzewania podłogowego i 0,3 CM% z ogrzewaniem podłogowym. Wynik pomiaru CM to obiektywny dowód na to, czy wylewka jest gotowa na przyjęcie podłogi, czy też wymaga dalszego schnięcia. Ignorowanie tych progów to proszenie się o kłopoty.
Na czas schnięcia wylewki kluczowy wpływ mają warunki panujące w pomieszczeniu. Optymalna temperatura to około 18-22°C, a wilgotność powietrza powinna być utrzymywana na umiarkowanym poziomie, najlepiej poniżej 65%. Kluczowa jest wentylacja – świeże powietrze pozwala wilgoci ulatniać się z pomieszczenia. Zbyt szybkie schnięcie (np. na skutek przeciągów czy ogrzewania kaloryferami w pierwszych dniach) może prowadzić do skurczu powierzchniowego i powstawania rys. Zbyt wolne schnięcie (wysoka wilgotność, brak wentylacji) znacznie wydłuża czas oczekiwania i zwiększa ryzyko powstania pleśni. Dlatego właściwa pielęgnacja wylewki po jej wylaniu jest równie ważna jak sam proces wylewania. Regularne wietrzenie, a w niektórych przypadkach zastosowanie osuszaczy powietrza, znacząco przyspiesza proces osiągania odpowiedniej wilgotności.
Przygotowań do wylewania podłogi betonowej czy cementowej należy również zwrócić uwagę na inne aspekty, które mogą pośrednio wpływać na proces schnięcia, takie jak izolacja przeciwwilgociowa pod wylewką. Brak odpowiedniej izolacji może powodować podciąganie kapilarne wilgoci z gruntu czy niższych kondygnacji, co skutecznie uniemożliwi prawidłowe wyschnięcie wylewki lub spowoduje ponowne zawilgocenie po jakimś czasie. Dlatego pełen obraz warunków panujących w budynku i podłoża pod wylewką jest niezbędny do prawidłowej oceny sytuacji i oszacowania realnego czasu potrzebnego na wyschnięcie. Pomiar wilgotności CM jest ostatecznym testem, ale zrozumienie procesów schnięcia i dbanie o odpowiednie warunki to droga do sukcesu bez niepotrzebnego stresu i kosztownych poprawek.
Jak widać na powyższym wykresie, wzrost grubości wylewki cementowej ma znaczący, a co najważniejsze, nieliniowy wpływ na wymagany czas schnięcia. Dodatkowy centymetr czy dwa potrafią wydłużyć oczekiwanie o kilka tygodni. Ta wizualizacja wyraźnie pokazuje, dlaczego dokładne zmierzenie grubości wylewki i cierpliwość w procesie schnięcia są absolutnie kluczowe dla zapewnienia trwałości i bezproblemowego użytkowania przyszłej podłogi. Próba przyspieszenia tego etapu poprzez np. włączenie intensywnego ogrzewania czy użycie mocnych osuszaczy bez odpowiedniej kontroli i wiedzy może przynieść więcej szkody niż pożytku, prowadząc do pęknięć wylewki. Dlatego najlepszym doradcą jest czas i profesjonalny pomiar wilgotności.
Folia paroizolacyjna pod panele na wylewce: Niezbędna warstwa ochronna
Na nowych, świeżo wylanych wylewkach cementowych, zanim ułożymy panele laminowane czy winylowe na podkładzie, warto – a w zasadzie wręcz trzeba – zastosować folię plastikową, czyli folię paroizolacyjną. Dlaczego? Bo ma ona kluczowe znaczenie w kontekście ochrony podłogi przed wilgocią, która może pochodzić z samej wylewki lub być podciągana z podłoża. Panele laminowane i większość paneli winylowych układanych w systemie podłogi pływającej są niezwykle wrażliwe na wilgoć, która potrafi spowodować ich nieodwracalne spuchnięcie, wypaczenie, a w konsekwencji zniszczenie.
Choć wylewka wydaje się sucha w dotyku i osiągnęła parametry pozwalające na ułożenie podłogi (niski procent wilgotności resztkowej według pomiaru CM), w dalszym ciągu może ona oddawać niewielkie ilości pary wodnej do góry przez długi czas. Jest to naturalny proces fizyczny, zwłaszcza w przypadku grubych wylewek cementowych czy tych, które nie mają skutecznej izolacji od gruntu. Bez folii paroizolacyjnej, ta subtelna, lecz stała emisja wilgoci będzie systematycznie oddziaływać na spód paneli. A panele laminowane, zbudowane głównie z HDF (High-Density Fibreboard), czyli sprasowanych włókien drzewnych, chłoną wilgoć niczym gąbka. Efekt? Niewidzialny wróg powoli, ale skutecznie, degraduje rdzeń paneli, prowadząc do ich wybrzuszeń i deformacji.
Folia paroizolacyjna pod panele na wylewce działa jak skuteczna bariera. Jej zadaniem jest zatrzymanie pary wodnej w wylewce i uniemożliwienie jej przedostania się do warstwy paneli. Standardowo stosuje się grubą folię polietylenową (PE) o grubości minimum 0,2 mm. Kluczowe jest jej prawidłowe ułożenie: pasy folii muszą być układane na zakładkę o szerokości co najmniej 20-30 cm, a miejsca połączeń powinny być szczelnie sklejone taśmą paroizolacyjną. Ważne jest także wywinięcie folii na ściany na wysokość kilku centymetrów powyżej planowanego poziomu gotowej podłogi, tak aby tworzyła szczelną wannę. Nadmiar folii odcina się dopiero po ułożeniu paneli i założeniu listew przypodłogowych.
Co ciekawe, folia paroizolacyjna jest zazwyczaj pomijana pod płytkami ceramicznymi czy klejonym parkietem, ale z zupełnie innych powodów. Kleje do płytek i parkietu często są dobrane w taki sposób, aby mogły "pracować" z pewną minimalną wilgotnością resztkową wylewki lub wręcz wspomagać jej odparowanie. Ponadto, płytki same w sobie są materiałem nieprzepuszczalnym dla wilgoci. Parkiet klejony do odpowiednio przygotowanej i przede wszystkim wystarczająco suchej wylewki tworzy w miarę stabilną warstwę, a stosowane grunty i kleje do drewna zazwyczaj tolerują minimalną wilgotność podłoża (niższą niż dla paneli) lub tworzą barierę. Natomiast w przypadku podłóg pływających, takich jak panele na klik, wilgoć nie ma jak uciec w kleju czy gruncie i wprost dostaje się do materiału paneli. Dlatego folia paroizolacyjna jest tak istotna dla trwałości podłogi panelowej, stanowiąc pierwszą linię obrony przed potencjalnym zagrożeniem ze strony wilgoci.
Choć rynek oferuje podkłady pod panele zintegrowane z warstwą paroizolacyjną, nawet wtedy warto upewnić się co do skuteczności takiego rozwiązania i sposobu łączenia kolejnych pasów podkładu, aby uzyskać pełną szczelność. Klasyczna folia PE o grubości 0,2 mm, odpowiednio ułożona na zakładkę i sklejona, jest sprawdzonym i niezawodnym sposobem na odcięcie podłogi pływającej od wilgoci. Jej koszt jest minimalny w porównaniu do potencjalnych kosztów wymiany spuchniętej podłogi. W tym kontekście, brak tej prostej warstwy ochronnej to czysta oszczędność pozornego grosza, która może skończyć się wydatkiem na dziesiątki tysięcy złotych w przypadku awarii. Dlatego, planując montaż paneli na wylewce, należy bezwzględnie uwzględnić w budżecie i planie prac położenie folii paroizolacyjnej. To absolutna podstawa, gwarantująca spokój ducha i trwałość wykończonej podłogi przez lata.