Ile Odczekać Po Wylewce Przed Ułożeniem Paneli?
Ile razy słyszałeś westchnienie: "Kiedy wreszcie położymy te panele?"? Decyzja o tym, ile zostawić na panele przy wylewkach, to jeden z kluczowych momentów na finiszu budowy czy remontu. Odpowiedź wcale nie sprowadza się tylko do odhaczenia dni w kalendarzu; niezbędny jest precyzyjny pomiar wilgotności wylewki, to on daje zielone światło do dalszych prac.
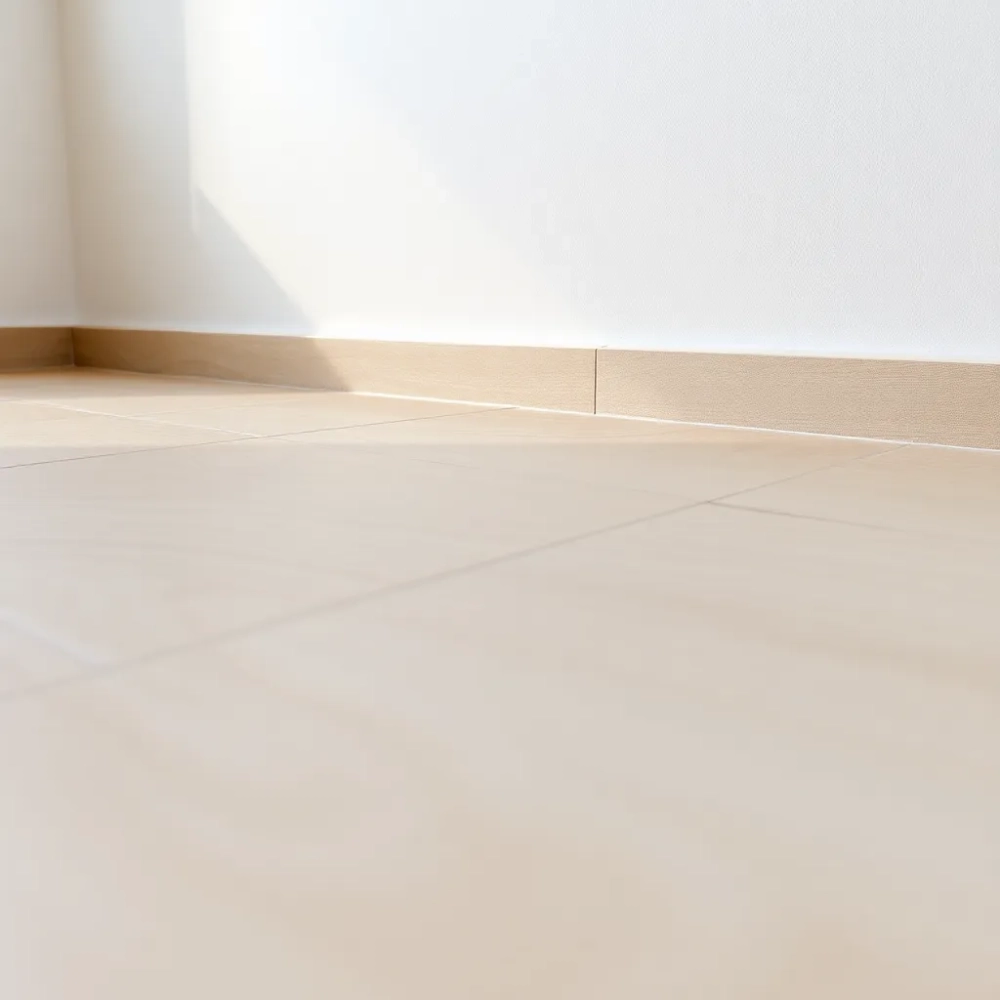
Patrząc na mnogość danych i zaleceń dotyczących przygotowania podłoża pod panele, szybko staje się jasne, że ścieżka do sukcesu nie prowadzi na skróty. Specjaliści z całego świata zgodnie podkreślają rolę kilku kluczowych zmiennych. Analiza setek przypadków potwierdza, że tempo twardnienia i wysychania to dwie różne bajki, a klucz leży w cierpliwym czekaniu, które jednak musi być poparte twardymi dowodami – cyframi z miernika wilgotności.
Grubość Wylewki (cm) | Orientacyjny Minimalny Czas Schnięcia (tygodnie) |
---|---|
do 4 | 1 tydzień na każdy cm |
5 | 6 tygodni (4cm x 1 tydz + 1cm x 2 tyg) |
6 | 8 tygodni (4cm x 1 tydz + 2cm x 2 tyg) |
7 | 12 tygodni (pierwsze 6cm = 8 tyg + 1cm x 4 tyg) |
10 | 24 tygodnie (pierwsze 6cm = 8 tyg + 4cm x 4 tyg) |
Dane te, choć dają pewien punkt odniesienia, stanowią jedynie szacunkowe minimum. Rzeczywiste tempo, z jakim wilgoć opuszcza strukturę wylewki, przypomina bardziej maraton z przeszkodami niż sprint. Każda wylewka to indywidualny przypadek, na którego "gotowość" wpływają dziesiątki czynników, od receptury mieszanki po cyrkulację powietrza w budynku.
Z tego powodu, poleganie wyłącznie na kalendarzu to hazard. Podłoga może wydawać się sucha na wierzchu już po kilku dniach, lecz uwięziona w głębszych warstwach wilgoć może być prawdziwą tykającą bombą, która eksploduje w postaci zniszczonych paneli po ich ułożeniu. Właśnie dlatego Pomiar wilgotności jest kluczowy, znacznie ważniejszy od teoretycznych wyliczeń czasu schnięcia.
Pamiętajmy, że wylewki wymagają odpowiednio długiego czasu schnięcia zanim można na nich zamontować podłogę laminowaną. Jest to proces, który natura musi wykonać w swoim tempie. Próba jego przyspieszenia bez zrozumienia podstaw fizyki materiałów budowlanych może prowadzić do kosztownych błędów. Dlatego profesjonalne podejście wymaga zarówno cierpliwości, jak i precyzyjnego sprzętu do kontroli wilgotności.
Poniżej przedstawiamy szczegółowe rozpracowanie wszystkich kluczowych aspektów związanych z przygotowaniem podłoża pod panele, poczynając od orientacyjnego czasu schnięcia, poprzez krytyczny pomiar wilgotności, aż do niezbędnego przygotowania podłoża.
Jak obliczyć wstępny, orientacyjny czas schnięcia wylewki?
Wyobraźmy sobie świeżą wylewkę betonową lub cementową jako gąbkę nasyconą wodą. Czas schnięcia to moment, w którym ta gąbka odda wystarczająco dużo wilgoci do otoczenia, by stać się stabilnym i bezpiecznym podłożem. Istnieje klasyczna, choć bardzo uproszczona zasada dotycząca wstępnego szacowania tego czasu.
Zgodnie z tą regułą, dla pierwszych 4 centymetrów grubości wylewki, przyjmuje się jeden tydzień schnięcia na każdy centymetr. To tempo wydaje się całkiem rozsądne w początkowej fazie, gdy woda ma relatywnie krótką drogę do pokonania w drodze do powierzchni.
Co ciekawe, dla kolejnych centymetrów, tempo schnięcia drastycznie maleje. Dla warstwy między 4 a 6 centymetrem grubości wylewki, przyjmuje się już dwa tygodnie na każdy dodatkowy centymetr. To pokazuje, że proces kapilarny staje się mniej wydajny w miarę wędrowania wilgoci przez grubszą strukturę.
Największym wyzwaniem są wylewki o grubości przekraczającej 6 centymetrów. W ich przypadku, każdy dodatkowy centymetr powyżej magicznej szóstki wymaga aż czterech tygodni na schnięcie. Matematyka jest bezwzględna – 10-centymetrowa wylewka, popularna w budownictwie, to już potencjalnie 24 tygodnie czekania, czyli ponad pół roku! Nie brzmi to optymistycznie, ale taka jest teoria.
Wróćmy do naszego przykładu 6 cm wylewki. Korzystając z tej reguły: pierwsze 4 cm schną 4 tygodnie (4x1 tydzień), kolejne 2 cm (do 6 cm) schną 4 tygodnie (2x2 tygodnie). Razem daje to sumę 8 tygodni, co idealnie pokrywa się z jednym z przykładów podanych w danych.
A co z 7-centymetrową wylewką? To (4cm x 1 tydz) + (2cm x 2 tyg) + (1cm x 4 tyg) = 4 + 4 + 4 = 12 tygodni. Widzicie, jak szybko rośnie czas oczekiwania z każdym dodatkowym centymetrem po szóstym?
Jednakże, ten wstępny, orientacyjny czas schnięcia to tylko punkt wyjścia i to obarczony sporym marginesem błędu. Czas schnięcia zależy bezpośrednio od warunków klimatycznych oraz wentylacji. Idealna sytuacja to stabilna temperatura około 20°C i niska wilgotność powietrza, połączona z intensywną, ale kontrolowaną wentylacją. Zbyt szybkie wysuszanie powierzchni może prowadzić do pęknięć skurczowych, ale brak wentylacji to katastrofa – wilgoć zamiast uciekać, krąży w powietrzu i wraca do wylewki.
Na tempo schnięcia wpływa również rodzaj spoiwa (cementowe schną inaczej niż anhydrytowe) oraz ewentualne dodatki chemiczne przyspieszające twardnienie (niekoniecznie schnięcie!) czy zmniejszające ilość wody zarobowej. Nawet rodzaj i grubość izolacji pod wylewką ma znaczenie – gruby styropian utrudni ewentualne schnięcie w dół, kierując całą wilgoć w górę, co z reguły wydłuża proces.
Wyobraźmy sobie taką scenę: na zewnątrz zimno i deszczowo, w środku świeżo położona wylewka w nowym, jeszcze niewentylowanym domu. Wilgoć z wylewki paruje, ale nie ma dokąd uciec. Osadza się na zimnych powierzchniach, nasyca powietrze do granic możliwości i... przestaje odparowywać z wylewki. Proces staje w miejscu. To klasyczny przykład sytuacji, gdy kalendarz pokazuje minione tygodnie, a wylewka wciąż jest mokra jak po powodzi.
Zapewnienie dostatecznej wentylacji budynku jest absolutnie kluczowe. Otwieranie okien na przestrzał (przewiew) przez kilka do kilkunastu minut co kilka godzin jest znacznie efektywniejsze niż uchylenie jednego okna na cały dzień. Chodzi o wymianę wilgotnego powietrza na suche. W okresach wysokiej wilgotności zewnętrznej (np. w deszczowe tygodnie jesienią) może być konieczne wspomaganie się osuszaczami powietrza, ale należy to robić z głową, monitorując wilgotność wylewki, by nie przesuszyć jej zbyt gwałtownie na powierzchni.
Dlatego, choć można obliczyć ten wstępny czas, nigdy, przenigdy nie powinien być on jedyną podstawą do podjęcia decyzji o układaniu paneli. Traktujcie te tygodnie jako sygnał: "może już blisko", a nie "na pewno już sucho". Prawdziwą odpowiedź dadzą tylko dokładne pomiary wilgotności.
Czas schnięcia wylewki to prawdziwa lekcja pokory dla każdego inwestora. Widzimy, jak nasze plany zderzają się z fizycznymi realiami budowy. Frustracja rośnie z każdym dniem, ale pośpiech jest najgorszym doradcą. Zamiast denerwować się na naturę, skupmy się na tym, co możemy kontrolować – monitorowaniu procesu i zapewnieniu optymalnych warunków. Ta cierpliwość się opłaci, gwarantując trwałość i estetykę naszej przyszłej podłogi. Ignorowanie tematu, kiedy należy odczekać jeden tydzień na cm (grubości) wylewki w tych początkowych etapach, to prosta droga do późniejszych problemów.
Należy również wziąć pod uwagę, że wylewki anhydrytowe schną szybciej, ale są bardziej wrażliwe na wilgoć podczas samego procesu schnięcia i wymagają innego reżimu, często obejmującego szlifowanie powierzchni w celu usunięcia "mleczka" kalnej warstwy, która może spowalniać oddawanie wilgoci. W przypadku wylewek cementowych taki problem zazwyczaj nie występuje.
Podsumowując, orientacyjny czas schnięcia według zasady "tygodni na centymetr" to jedynie mapa, a nie faktyczny pomiar. Zawsze należy zapewnić dostateczną wentylację budynku i mieć świadomość, że podany czas powinien być traktowany wyłącznie orientacyjnie. To pierwszy krok w długiej drodze do gotowego podłoża.
Pomiar wilgotności wylewki – Dlaczego jest ważniejszy niż czas?
Zapomnij o kalendarzu jako jedynym wyznaczniku gotowości podłoża. To chyba najważniejsza lekcja, jaką można wynieść z doświadczeń wielu pokoleń budowlańców i parkieciarzy. Choć orientacyjny czas schnięcia daje pewne wyobrażenie, Pomiar wilgotności wylewki jest kluczowy i absolutnie nadrzędny wobec wszelkich szacunków czasowych.
Dlaczego? Bo proces schnięcia jest dynamiczny i zależy od tak wielu zmiennych, że czas jest tylko bardzo grubym przybliżeniem. Temperatura powietrza, wilgotność względna otoczenia, przepływ powietrza (wentylacja), grubość i rodzaj wylewki, ilość wody użytej w mieszance, obecność ogrzewania podłogowego – wszystkie te czynniki wpływają na to, jak szybko wilgoć opuszcza jastrych. Słynne "czas schnięcia zależy bezpośrednio od warunków klimatycznych oraz wentylacji" to nie puste słowa, to fizyka w czystej postaci.
Wylewka może wydawać się twarda i sucha na powierzchni po kilku tygodniach, ale głębiej w jej strukturze wilgoć nadal "siedzi" i wędruje w górę. Ta wędrówka może zabrać trochę czasu. Uwięziona wilgoć musi w końcu znaleźć ujście. Jeśli nałożymy na nią szczelną barierę w postaci folii paroizolacyjnej i paneli laminowanych, wilgoć nie ma drogi ucieczki do góry. Zacznie kumulować się pod folią i wnikać w panele, które są materiałem higroskopijnym – chłoną wodę jak gąbka.
Konsekwencje są, mówiąc delikatnie, opłakane. Panele laminowane, pochłaniając wilgoć, zaczną pęcznieć, wypaczać się, podnosić na łączeniach. Zamki mogą popękać, a cała podłoga stracić swoją płaskość i estetykę. W skrajnych przypadkach, pod panelami może pojawić się pleśń i grzyb, stanowiące zagrożenie dla zdrowia domowników. To scenariusz, którego absolutnie chcemy uniknąć.
To właśnie dlatego wilgotności należy przeprowadzać za każdym razem, gdy myślimy o montażu paneli, i zawsze wykonywać pomiary w każdym przypadku. Pomiar to jedyna obiektywna metoda oceny rzeczywistej kondycji podłoża. Miernik nie kłamie (o ile jest sprawny i prawidłowo używany). Pokazuje nam twardą, choć czasem gorzką, prawdę o tym, czy wylewka jest gotowa na przyjęcie podłogi.
Wymogi producentów paneli laminowanych dotyczące maksymalnej dopuszczalnej wilgotności podłoża są precyzyjne i rygorystyczne. Dla wylewek cementowych (betonowych) zazwyczaj limit wynosi 2.0% wilgotności mierzonej metodą karbidową (CM), a w przypadku podłóg z ogrzewaniem podłogowym nawet poniżej 1.8% CM. Dla wylewek anhydrytowych limity są jeszcze niższe – typowo poniżej 0.5% CM dla podłóg z ogrzewaniem i poniżej 1.8% CM bez ogrzewania (tak, limit dla anhydrytu bez ogrzewania jest podobny jak dla cementu, ale bazuje na innych właściwościach materiału i szybkości schnięcia).
Ignorowanie tych progów, nawet jeśli minęło mnóstwo tygodni zgodnie z zasadą "tygodnia na centymetr", to po prostu proszenie się o problemy. Gwarancja na panele jest często uzależniona od udokumentowania prawidłowej wilgotności podłoża przed montażem. Brak takich dowodów może oznaczać utratę gwarancji w przypadku problemów z podłogą.
Przypomina to trochę jazdę samochodem – możemy obliczyć teoretyczny zasięg na baku, ale to dopiero wskaźnik paliwa i faktyczna droga pokażą, ile jeszcze naprawdę przejedziemy. W przypadku wylewki, wskaźnikiem jest miernik wilgotności. Bez niego jedziemy na oślep, ryzykując, że utkniewy na poboczu, czyli zniszczymy nową podłogę.
Dlatego właśnie zawsze, bez wyjątku, należy prowadzić pomiary wilgotności oraz zapisywać i przechowywać ich wyniki. To nasza polisa ubezpieczeniowa i dowód należytej staranności w przygotowaniu podłoża. Sam upływający czas, choć psychologicznie ważny ("oj, długo to trwa..."), z perspektywy fizyki materiałów jest drugorzędny wobec faktycznego poziomu wilgoci uwięzionej w masie jastrychu. W gruncie rzeczy, to wilgotność rzeczywista, nie kalendarz, decyduje o gotowości.
Wybór odpowiedniej metody pomiaru jest równie ważny, co sam fakt jego przeprowadzenia. Różne mierniki dają różne wyniki i nie wszystkie są akceptowane przez producentów paneli jako dowód gotowości. O tym, jakie metody są prawidłowe i powszechnie stosowane, opowiemy w kolejnym rozdziale.
Pamiętajmy: cel jest jeden – sucha i stabilna powierzchnia pod panele. Czas to tylko zmienna w równaniu, podczas gdy wilgotność to bezpośredni wskaźnik stanu materii. Inwestując w dobry miernik lub zlecając pomiary specjaliście, inwestujemy w spokój ducha i trwałość naszej podłogi na lata.
Prawidłowe metody pomiaru wilgotności podłoża przed ułożeniem paneli
Skoro już wiemy, że pomiar wilgotności jest ważniejszy od czasu, przyjrzyjmy się temu, jak to zrobić poprawnie. Na rynku dostępnych jest kilka metod i rodzajów urządzeń, ale nie wszystkie są sobie równe, szczególnie jeśli chodzi o precyzję i akceptację przez producentów paneli jako dowód gotowości podłoża.
Zasadniczo wyróżniamy dwie główne grupy metod pomiarowych: metody elektryczne i metody chemiczne (najbardziej znana to metoda karbidowa CM). Każda z nich ma swoje zastosowania, zalety i wady.
Elektryczne mierniki wilgotności
Są to najczęściej spotykane i najbardziej przystępne cenowo urządzenia. Działają na zasadzie pomiaru przewodnictwa elektrycznego lub impedancji materiału. Im więcej wilgoci w podłożu, tym lepiej przewodzi ono prąd (zawarte w wodzie sole zwiększają przewodność), co przekłada się na wyższy odczyt wilgotności.
Mierniki elektryczne dzielą się na:
- Mierniki kołkowe (oporowe): Posiadają dwa lub więcej ostrych bolców, które wbija się w powierzchnię wylewki na głębokość kilku milimetrów. Mierzą opór elektryczny między bolcami.
- Mierniki bezinwazyjne (pojemnościowe): Przykładane są do powierzchni podłoża. Mierzą zmiany w polu elektromagnetycznym wywołane przez wilgoć w materiale. Pozwalają szybko skanować większe powierzchnie bez niszczenia jastrychu.
Zalety mierników elektrycznych to szybkość pomiaru, łatwość obsługi i zazwyczaj niższy koszt zakupu. Nadają się świetnie do wstępnego skanowania powierzchni, lokalizowania potencjalnie bardziej wilgotnych obszarów (np. w narożnikach, przy ścianach, w miejscach o słabszej wentylacji) i monitorowania procesu schnięcia w czasie. Pozwalają nam "zobaczyć", gdzie problem wilgoci jest największy.
Niestety, mierniki elektryczne mają poważne wady, które dyskwalifikują je jako narzędzie do ostatecznej oceny gotowości podłoża pod panele w wielu sytuacjach (zwłaszcza formalnych lub gwarancyjnych). Ich odczyty są bardzo wrażliwe na temperaturę wylewki i otoczenia, wilgotność względną powietrza, a co najważniejsze, na obecność soli i innych substancji chemicznych w wylewce. Mogą dawać zafałszowane wyniki, zawyżając wilgotność, nawet jeśli wylewka jest już w miarę sucha.
Wielu producentów paneli nie akceptuje pomiarów wykonanych jedynie miernikami elektrycznymi jako podstawy roszczeń gwarancyjnych. Traktują je jako narzędzie pomocnicze i orientacyjne. Należy to mieć na uwadze, używając takiego sprzętu – to świetny "termometr", ale nie "rentgen", jeśli idzie o strukturę wylewki.
Metoda karbidowa (CM - Calcium Carbide Method)
To jest złoty standard w branży podłogowej i metoda najczęściej wymagana przez producentów paneli do formalnej akceptacji podłoża. Polega na chemicznej reakcji wody zawartej w próbce wylewki z karbidem wapnia (CaC₂). W reakcji powstaje acetylen (C₂H₂) i wodorotlenek wapnia (Ca(OH)₂). Kluczem jest wydzielanie acetylenu, który będąc gazem, powoduje wzrost ciśnienia w zamkniętym naczyniu reakcyjnym.
Procedura pomiaru metodą CM jest bardziej skomplikowana niż użycie miernika elektrycznego i wymaga specjalistycznego sprzętu: wagi laboratoryjnej do precyzyjnego odmierzenia próbki, młotka i dłuta do pobrania próbki (lub wiertła), moździerza do rozkruszenia materiału, naczynia reakcyjnego (stalowej butelki) z manometrem i specjalnych ampułek z karbidem.
Próbki do badania pobiera się z głębszych warstw wylewki (np. z 2/3 grubości lub minimum 2-3 cm pod powierzchnią), a nie tylko z góry. Jest to kluczowe, ponieważ, jak już wiemy, wierzch wylewki może być suchy, podczas gdy niższe warstwy są nadal nasycone wilgocią. Pobieranie próbek z kilku miejsc (minimum 3-4 na standardowe pomieszczenie) jest absolutnie niezbędne, aby uzyskać reprezentatywny obraz całej powierzchni.
Próbka jest następnie dokładnie ważona, rozkruszana, umieszczana w naczyniu z rozbitą ampułką karbidu. Naczynie jest szczelnie zamykane, a jego zawartość mieszana. Powstałe ciśnienie jest mierzone manometrem po określonym czasie (np. 10-20 minut), zgodnie z normą. Odczyt ciśnienia przeliczany jest na procent wilgotności wylewki, wyrażony w % CM.
Zalety metody CM: daje najbardziej wiarygodne wyniki dotyczące rzeczywistej zawartości wody w głębszych warstwach wylewki. Pomiar jest mniej wrażliwy na temperaturę, wilgotność powietrza czy zanieczyszczenia soli w porównaniu do metod elektrycznych. Jest to metoda referencyjna, uznawana w normach i powszechnie akceptowana w protokołach zdawczo-odbiorczych.
Wady: metoda CM jest niszcząca (trzeba wykuć lub wywiercić fragment wylewki), czasochłonna (trzeba odczekać na reakcję) i wymaga stosunkowo drogiego sprzętu oraz wiedzy fachowej do prawidłowego przeprowadzenia i interpretacji wyników. Koszt wykonania kilku pomiarów przez certyfikowanego specjalistę może być znaczący, ale to inwestycja w bezpieczeństwo.
Jak zatem postąpić? Prawidłowe metody pomiaru wilgotności podłoża przed ułożeniem paneli to przede wszystkim te zgodne z zaleceniami producenta paneli. Zawsze, zawsze należy wykonywać pomiary wilgotności podłoża przed ułożeniem paneli. W każdym przypadku należy prowadzić pomiary wilgotności oraz zapisywać i przechowywać ich wyniki. Nawet jeśli producent dopuszcza użycie mierników elektrycznych, często wymagane są dodatkowe warunki lub konieczność kalibracji do danego typu podłoża.
Z doświadczenia wiem, że najlepiej zacząć od monitorowania procesu schnięcia tańszym miernikiem elektrycznym, identyfikując najwolniej schnące strefy. Kiedy odczyty na mierniku elektrycznym zbliżą się do wartości, które z doświadczenia (lub po konsultacji) wskazują na potencjalną gotowość, należy wykonać pomiary metodą CM, pobierając próbki w kilku krytycznych punktach, zwłaszcza w tych, które wcześniej elektryczny miernik wskazał jako najbardziej wilgotne. To połączenie szybkości z dokładnością.
Producenci paneli laminowanych w swoich instrukcjach montażu często podają konkretne wartości wilgotności CM, które nie mogą zostać przekroczone. Należy ściśle przestrzegać zaleceń producenta paneli, zarówno jeśli chodzi o dopuszczalny poziom wilgotności, jak i metody jego pomiaru. Nieprzestrzeganie tych wytycznych może skutkować odmową uznania gwarancji.
Podsumowując, choć mierniki elektryczne są wygodne do wstępnej oceny i monitorowania, do ostatecznej akceptacji podłoża pod panele laminowane na wylewkach cementowych najczęściej stosowaną i wymaganą metodą jest standardowa metoda karbidowa (CM). Pamiętajmy też, że w przypadku podłóg betonowych należy zawsze postępować zgodnie z zaleceniami określonymi w instrukcji montażu paneli, które są dostosowane do specyfiki produktu i warunków jego użytkowania.
Niezbędne przygotowanie podłoża: folia paroizolacyjna i podkład
Gdy wreszcie, po tygodniach lub miesiącach czekania i precyzyjnych pomiarach, wylewka osiągnie wymaganą suchość, wydawać by się mogło, że droga pod panele jest wolna. Stop! Sukces tkwi w szczegółach, a dwa kluczowe elementy przygotowania podłoża są absolutnie niezbędne: folia paroizolacyjna i podkład.
Folia Paroizolacyjna – Nasz "parasol" od spodu
Dlaczego folia paroizolacyjna? Przecież wylewka jest już sucha! Teoretycznie tak, ale w praktyce nawet wylewka, która spełnia normy wilgotności dla danego momentu, może przez lata eksploatacji "pracować", wchłaniając wilgoć z powietrza w okresach jej wysokiej wilgotności lub w marginalnym stopniu migrując z podłoża gruntowego, jeśli mieszkamy na parterze (choć oczywiście powinna być tam solidna hydroizolacja główna). Folia stanowi zabezpieczenie przed wilgocią od spodu, działając jak ostatnia linia obrony przed wszelkimi, nawet niewielkimi, źródłami wilgoci, które mogłyby zaszkodzić panelom.
Jest to szczególnie ważne w przypadku nowych podłóg betonowych. Standardem jest, że przed ułożeniem paneli laminowanych na nowych podłogach betonowych należy zawsze położyć folię plastikową na podłogę betonową. Jaki rodzaj folii wybrać? Najczęściej stosuje się grubą folię polietylenową (PE) o minimalnej grubości 0.2 mm (czyli 200 mikronów). Nie oszczędzajmy na tym elemencie, cieńsza folia jest podatna na uszkodzenia podczas montażu i może nie spełnić swojej roli.
Montaż folii jest kluczowy. Folię kładzie się na oczyszczonej z wszelkich zanieczyszczeń i ostrych elementów wylewce. Poszczególne pasy folii muszą na siebie zachodzić z dużym zakładem, minimum 20-30 cm. Zakłady te muszą być szczelnie sklejone wodoodporną taśmą (np. specjalną taśmą do folii lub szeroką taśmą budowlaną o wysokiej przyczepności). To nie jest miejsce na niedokładności – każdy niezaklejony zakład to potencjalna droga dla wilgoci.
Bardzo ważnym etapem jest wywinięcie folii na ściany. Folię należy poprowadzić w górę ściany na wysokość przyszłego montażu listew przypodłogowych (zazwyczaj 5-10 cm). Również w tych miejscach folia powinna być przyklejona do ściany, tworząc swego rodzaju "wannę". Po zamontowaniu paneli, nadmiar folii wystający ponad ich powierzchnię zostanie obcięty, a całość schowana pod listwą. Takie solidne zabezpieczenie to tania i niezwykle skuteczna polisa na przyszłość.
Istnieją wyjątki od reguły kładzenia folii paroizolacyjnej. Czasami, w przypadku wylewek anhydrytowych na parterze, producenci paneli mogą dopuścić brak folii, pod warunkiem, że pod anhydrytem znajduje się szczelna, pierwotna hydroizolacja budynku. Zawsze jednak należy to dokładnie sprawdzić w instrukcji montażu konkretnych paneli i w dokumentacji technicznej budynku. W zdecydowanej większości przypadków, zwłaszcza na piętrach czy w budownictwie starszego typu, folia jest absolutnym must-have.
Podkład pod panele – Wyrównanie, izolacja i amortyzacja
Po rozłożeniu i uszczelnieniu folii przychodzi czas na podkład. Choć wydaje się prostym elementem, wybór odpowiedniego podkładu jest niezwykle ważny, aby uniknąć problemów w przyszłości, takich jak skrzypienie podłogi, pękanie zamków paneli czy słaba izolacja akustyczna i termiczna.
Podkład pełni kilka kluczowych funkcji:
- Wyrównanie niewielkich nierówności podłoża: Dobrej jakości podkład może zniwelować drobne nierówności (do 1-4 mm, w zależności od typu), które pozostały na wylewce po jej wylaniu.
- Izolacja akustyczna: Podkłady znacząco poprawiają komfort użytkowania podłogi, redukując dźwięki przenoszone do pomieszczenia poniżej (dźwięki uderzeniowe IS, np. stąpanie) oraz dźwięki odbijające się w samym pomieszczeniu (dźwięki powietrzne RWS).
- Izolacja termiczna: Podkłady zmniejszają ucieczkę ciepła do wylewki, co czyni podłogę przyjemniejszą w dotyku. W przypadku ogrzewania podłogowego należy jednak wybrać podkład o niskim oporze cieplnym (np. perforowany XPS), aby ciepło mogło efektywnie przenikać do pomieszczenia.
- Ochrona systemu zamków: Podkład amortyzuje naciski i drgania, chroniąc delikatne zamki paneli przed uszkodzeniem pod wpływem obciążeń.
- Odporność na obciążenia (Wytrzymałość na ściskanie CS): To jeden z najważniejszych parametrów! Podkład musi być na tyle sztywny i gęsty, aby pod ciężarem mebli czy intensywnego użytkowania nie uginał się zbyt mocno, co prowadziłoby do pracy (uginania) paneli i pękania ich zamków. Dobry podkład powinien mieć współczynnik CS na poziomie co najmniej 100 kPa dla normalnego użytkowania domowego, a w miejscach o większym obciążeniu (np. pod szafami, w ciągach komunikacyjnych) lub przy cienkich panelach nawet powyżej 200 kPa. Miękkie podkłady gąbkowe mogą prowadzić do szybkiego zniszczenia podłogi.
Na rynku dostępnych jest wiele rodzajów podkładów:
- Pianki polietylenowe (PE): Najtańsze, ale często najmniej sztywne (niski CS). Sprawdzają się raczej w pomieszczeniach o niskim natężeniu ruchu. Ich opór cieplny jest wysoki, słabo nadają się na ogrzewanie podłogowe.
- Podkłady z ekstrudowanego polistyrenu (XPS): Gęste, bardziej odporne na ściskanie, dobrze niwelują nierówności (np. do 2-3 mm). Są dobrym wyborem, zwłaszcza w wersji perforowanej na ogrzewanie podłogowe.
- Podkłady z włókien drzewnych: Ekologiczne, charakteryzują się dobrą izolacyjnością termiczną i akustyczną (szczególnie dźwięki uderzeniowe), ale mogą być podatne na wilgoć, jeśli folia nie została położona idealnie. Niewielkie właściwości wyrównujące.
- Podkłady kwarcowe lub mineralne (maty): Bardzo gęste, wysoki CS, doskonale przewodzą ciepło (świetne na ogrzewanie podłogowe), dobrze redukują dźwięki, ale są stosunkowo drogie i ciężkie. Wymagają niemal idealnie równego podłoża.
Niektóre podkłady mają już przytwierdzoną folię z tworzywa sztucznego, co pozornie ułatwia montaż. Należy jednak upewnić się, że zakładanie pasów takiego podkładu również wykonamy z należytą starannością, zachowując wymagany zakład (zwykle 10-15 cm) i szczelnie go sklejając taśmą. Choć jest to wygodne rozwiązanie "dwa w jednym", w przypadku podłóg na gruncie czy pomieszczeń o podwyższonej wilgotności, czasem bezpieczniej jest zastosować grubą folię 0.2 mm jako osobną warstwę pod podkład.
Zawsze konsultujmy wybór podkładu z instrukcją montażu paneli. Producenci paneli często określają minimalne wymagania dotyczące parametrów podkładu (szczególnie CS), których spełnienie jest warunkiem utrzymania gwarancji.
Podsumowując, przygotowanie podłoża pod panele laminowane na nowych wylewkach nie kończy się na samym schnięciu i pomiarze wilgotności. Zastosowanie folii paroizolacyjnej o grubości minimum 0.2 mm, kładzionej z zakładami i wywijanej na ściany, jest absolutnie niezbędne jako folia paroizolacyjna jest absolutnie niezbędna do zabezpieczenia przed wilgocią resztkową i kapilarną. Dodatkowo, wybór odpowiedniego podkładu, dostosowanego do rodzaju paneli, podłoża, oczekiwanej akustyki i obecności ogrzewania podłogowego, a przede wszystkim o podkład z odpowiednią wytrzymałością na ściskanie (CS), ma kluczowe znaczenie dla trwałości, stabilności i komfortu użytkowania naszej przyszłej podłogi. Ignorowanie tych etapów to proszenie się o bardzo kosztowny, powtórny remont.