Zewnętrzne Metalowe Panele Ścienne Koszt 2025
Zastanawiasz się nad tym, jakie są koszty zewnętrznych metalowych paneli ściennych? Decydując się na zewnętrzne metalowe panele ścienne, dokonujesz strategicznej inwestycji w trwałość, funkcjonalność i estetykę budynku. Kluczową informacją jest to, że ich cena nie jest jednolitą wartością – koszt zakupu paneli to złożona wypadkowa wielu składowych, które wymagają dokładnej analizy, aby optymalnie dopasować rozwiązanie do indywidualnych potrzeb i budżetu. Nie daj się zwieść prostym cennikom, diabeł tkwi w szczegółach materiału, rdzenia, grubości i montażu.
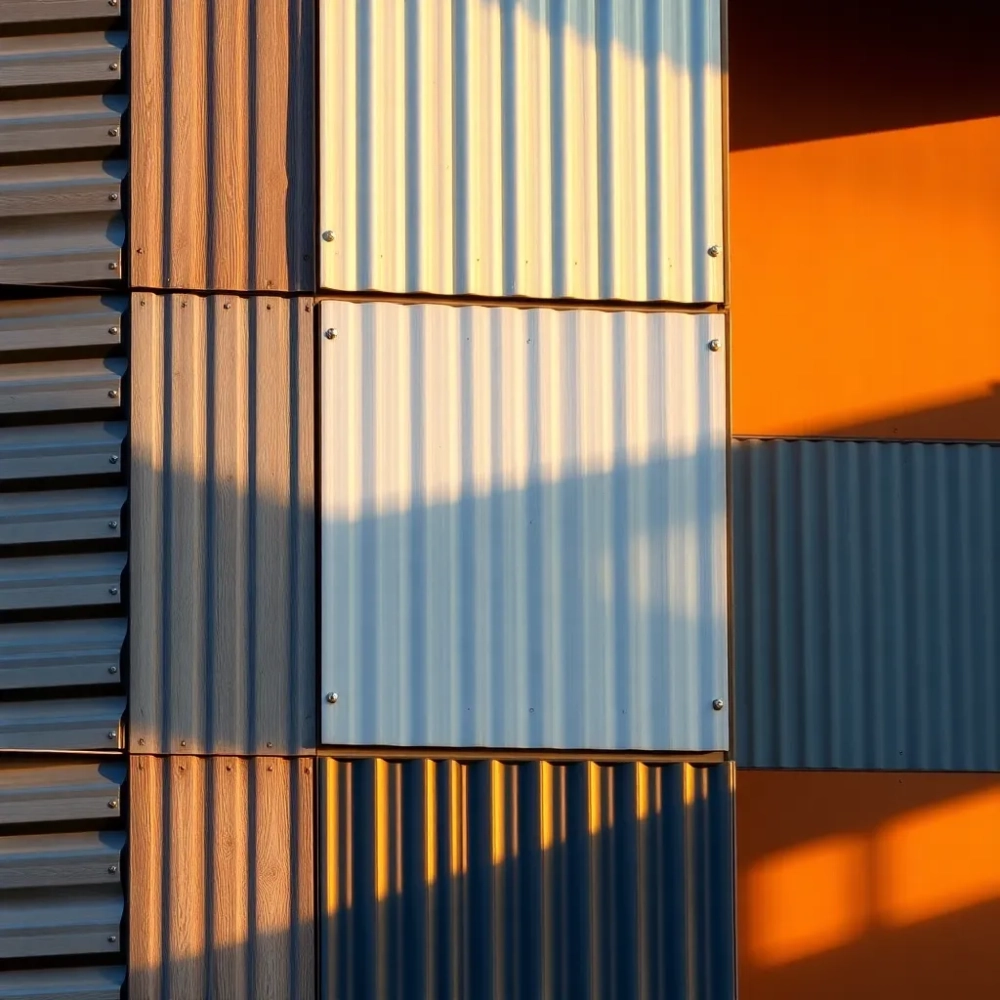
Patrząc na zagadnienie exterior metal wall panels cost z szerszej perspektywy, analiza dostępnych danych rynkowych pozwala dostrzec pewne prawidłowości. Podstawowy koszt metalowych paneli ściennych za metr kwadratowy waha się w zależności od podstawowych parametrów, co pokazuje poniższe zestawienie przykładowych, uśrednionych widełek cenowych obserwowanych w sektorze komercyjnym i przemysłowym w perspektywie nadchodzących lat.
Rodzaj Panela (Przykładowy) | Rdzeń | Grubość (mm) | Uśredniony koszt/m² (przykładowe widełki) |
---|---|---|---|
Panel Stalowy (Ocynk + Powłoka) | PIR | 80 | Ok. 180-250 PLN/m² |
Panel Stalowy (Ocynk + Powłoka) | Wełna Mineralna | 100 | Ok. 220-300 PLN/m² |
Panel Stalowy (Ocynk + PVDF) | PIR | 100 | Ok. 280-380 PLN/m² |
Panel ze Stali Nierdzewnej (podstawowy stop) | PIR | 80 | Ok. 450-600+ PLN/m² |
Z przedstawionej analizy widać wyraźnie, że na ostateczną kwotę zakupu wpływa splot konkretnych decyzji projektowych i materiałowych. Przykładowo, wybór grubszego rdzenia izolacyjnego czy zastosowanie powłoki PVDF zamiast standardowej powłoki poliestrowej, automatycznie podnosi koszt jednostkowy za metr kwadratowy. Niemniej jednak, te zróżnicowane ceny odzwierciedlają także różnice w parametrach technicznych, trwałości i docelowej estetyce elewacji, co czyni decyzję o wyborze materiału ważnym elementem planowania całkowitego kosztu elewacji.
Materiał Paneli a Cena
Wpływ materiału, z którego wykonane są panele elewacyjne, na ich ostateczny koszt zakupu jest fundamentalny, można by rzec, że to "serce" wyceny. Niczym w kuchni, gdzie jakość składników decyduje o smaku potrawy, tutaj rodzaj metalu determinuje nie tylko cenę, ale przede wszystkim trwałość, odporność na warunki zewnętrzne i estetykę elewacji na długie lata. Nie ma co owijać w bawełnę – wysokiej jakości surowiec kosztuje, ale przynosi wymierne korzyści w przyszłości.
Zacznijmy od paneli wykonanych ze stali nierdzewnej. To jest crème de la crème, jeśli chodzi o trwałość i odporność na korozję. Ich zastosowanie jest często podyktowane wymagającymi warunkami środowiskowymi, takimi jak bliskość morza z jego zasolonym powietrzem czy środowiska przemysłowe narażone na agresywne substancje chemiczne. Wyobraź sobie elewację narażoną na ciągły kontakt z mgłą morską – stal nierdzewna poradzi sobie z tym wyzwaniem bez mrugnięcia okiem, podczas gdy inne materiały mogłyby szybko poddać się korozji.
Naturalnie, ta ponadprzeciętna odporność ma swoją cenę. Panele ze stali nierdzewnej plasują się w najwyższej kategorii cenowej. Przykładowo, gdy metr kwadratowy standardowego panelu stalowego z powłoką może kosztować około 200-300 zł, metr kwadratowy panelu ze stali nierdzewnej może osiągnąć cenę od 450 zł wzwyż, często przekraczając 600 zł, w zależności od gatunku stali nierdzewnej (np. 304 czy 316) i wykończenia powierzchni.
Alternatywą, znacznie bardziej powszechną i przyjazną dla budżetu większości inwestycji, są panele stalowe z powłokami ochronnymi. Tutaj podstawą jest blacha stalowa ocynkowana, która sama w sobie stanowi pewną barierę antykorozyjną. Kluczowa jednak staje się jakość i rodzaj powłoki zewnętrznej, która nadaje panelom kolor, fakturę i dodatkową odporność na czynniki atmosferyczne oraz promieniowanie UV. To jest ten element, który widzi każdy i który w dużej mierze odpowiada za wygląd elewacji.
Najpopularniejszym rodzajem powłoki jest poliester (SP). Jest to rozwiązanie ekonomiczne i oferujące szeroką paletę kolorów (RAL). Cena paneli z taką powłoką jest najbardziej atrakcyjna, jednak jej trwałość i odporność na blaknięcie w intensywnym słońcu czy zarysowania są niższe w porównaniu do bardziej zaawansowanych powłok. Zwykle gwarancja na takie powłoki wynosi około 10-15 lat.
Nieco wyżej w hierarchii cenowej i jakościowej znajduje się powłoka poliestrowa matowa (Matt Poliester) lub strukturalna. Oferuje ona lepszą odporność na zarysowania i często dłuższą trwałość koloru, dając przy tym bardziej stonowany, elegancki wygląd. Koszt metra kwadratowego paneli z tą powłoką jest zazwyczaj o kilkanaście do kilkudziesięciu procent wyższy niż w przypadku standardowego poliestru.
Szczególnie cenioną, choć droższą opcją, jest powłoka PVDF (polifluorek winylidenu) lub PUR (poliuretan). Te powłoki charakteryzują się wyjątkową odpornością na promieniowanie UV, korozję i czynniki chemiczne. Są one często stosowane w budynkach o podwyższonych wymaganiach estetycznych i trwałościowych, np. w obiektach użyteczności publicznej, biurowcach czy na terenach zanieczyszczonych przemysłowo. Gwarancje na powłoki PVDF/PUR mogą sięgać 25-40 lat, co oczywiście znajduje odzwierciedlenie w wyższej cenie.
Przykładowo, ten sam panel stalowy o grubości 80 mm z rdzeniem PIR, pokryty standardowym poliestrem może kosztować 200 zł/m², podczas gdy wersja z powłoką PVDF już 280-350 zł/m². Różnica pozornie duża na etapie zakupu, w perspektywie 25 czy 40 lat użytkowania może okazać się minimalną dopłatą za spokój i estetyczny wygląd fasady przez długi czas.
Niektóre realizacje wymagają zastosowania paneli aluminiowych. Choć rzadziej stosowane jako panele warstwowe w tradycyjnym rozumieniu, aluminium jest popularnym materiałem na kasetony elewacyjne. Aluminium jest lżejsze i bardziej odporne na korozję niż stal w standardowych warunkach (choć ma inne wyzwania, np. odporność na kwasy). Panele aluminiowe są zazwyczaj droższe od stalowych z powłokami, ale tańsze od paneli ze stali nierdzewnej. Ich cena jest często uzależniona od grubości blachy aluminiowej i stosowanej powłoki (często proszkowe lub PVDF).
Warto również wspomnieć o grubości samej blachy zastosowanej na okładzinę panela. Standardowo stosuje się blachę o grubości 0.4, 0.5 lub 0.6 mm. Cieńsza blacha jest tańsza, ale potencjalnie bardziej podatna na wgniecenia czy odkształcenia podczas montażu lub użytkowania. Grubsza blacha zwiększa sztywność panelu i jego odporność mechaniczną, co wpływa na cenę metra kwadratowego.
Przyjrzyjmy się hipotetycznemu studium przypadku: Klient planuje wybudować niewielką halę magazynową na terenie miejskim. Dostępne opcje elewacji to panele stalowe z powłoką poliestrową lub z powłoką PVDF. Zakładając 1000 m² elewacji, różnica w koszcie zakupu między standardowym poliestrem (np. 220 zł/m²) a PVDF (np. 320 zł/m²) wynosi 100 000 zł. Niby dużo, ale jeśli hala ma stać przez 30-40 lat, a powłoka PVDF ma dwukrotnie dłuższą gwarancję trwałości koloru i odporności na degradację, ta dopłata rozkłada się na dziesiątki lat. Czy warto oszczędzać na powłoce, wiedząc, że fasada po 15-20 latach może wyglądać znacznie gorzej i wymagać kosztownego malowania lub wymiany?
Z perspektywy eksperta budowlanego, różnica w cenie między poszczególnymi materiałami i powłokami to nie tylko cyfra w kosztorysie, ale przede wszystkim inwestycja w długowieczność i bezproblemowe użytkowanie obiektu. Wybór najtańszej opcji może kusić, ale często oznacza kompromis w zakresie trwałości i konieczność poniesienia dodatkowych kosztów remontowych w przyszłości. Drogie zazwyczaj oznacza trwalsze i bardziej odporne, co w długim okresie eksploatacji może paradoksalnie przełożyć się na niższe koszty utrzymania.
Podsumowując wpływ materiału na koszt zakupu paneli, można śmiało stwierdzić, że jest to jedna z najważniejszych zmiennych. Stal nierdzewna i wysokiej jakości powłoki typu PVDF czy PUR znacząco podnoszą cenę jednostkową w porównaniu do standardowej stali z powłoką poliestrową. Tańsze panele mogą być wystarczające dla mniej wymagających zastosowań, ale dla budynków, gdzie estetyka i minimalne koszty konserwacji przez długie lata są priorytetem, warto rozważyć droższe, bardziej wytrzymałe opcje. Nie chodzi o to, żeby przepłacać, ale żeby wybierać świadomie, biorąc pod uwagę pełen cykl życia inwestycji.
Cena powłoki zależy również od jej koloru i stopnia połysku. Kolory specjalne, metalizowane lub o wysokim połysku, często kosztują więcej niż standardowe kolory z palety RAL o niższym połysku. Warto to uwzględnić, jeśli projekt zakłada nietypową estetykę elewacji. Czasami nawet subtelna zmiana koloru może wpłynąć na finalną kwotę zakupu paneli na dużą powierzchnię.
Rodzaj zastosowanej stali, a także jej grubość, mają znaczący wpływ na parametry mechaniczne paneli, takie jak nośność na wiatr czy obciążenie śniegiem. Wyższe wymagania konstrukcyjne mogą wymusić zastosowanie grubszej blachy stalowej (np. 0.6 mm zamiast 0.5 mm), co oczywiście zwiększa masę paneli i ich cenę, ale zapewnia niezbędne bezpieczeństwo i trwałość konstrukcji elewacyjnej. To pokazuje, jak pozornie drobne detale techniczne przekładają się na finalne koszty paneli elewacyjnych.
Analizując rynek dostawców, można również zauważyć, że pochodzenie materiałów oraz reputacja producenta mają pewien wpływ na cenę. Renomowani producenci, często używający certyfikowanych surowców i nowoczesnych technologii produkcji, mogą oferować panele w nieco wyższej cenie, ale za to dają większą gwarancję jakości i powtarzalności parametrów, co w przypadku tak ważnego elementu budynku jak elewacja jest nie do przecenienia. Różnice w cenie za metr kwadratowy mogą wynosić od kilku do kilkunastu złotych, co na dużym projekcie przekłada się na znaczącą kwotę.
Nie zapominajmy również o fakturze powierzchni. Oprócz standardowej, gładkiej powierzchni, dostępne są panele z przetłoczeniami (np. mikrofale, liniowe). Choć różnica w koszcie między nimi a panelami gładkimi nie jest zazwyczaj tak drastyczna jak w przypadku różnych typów powłok czy materiałów, faktura również może nieznacznie wpłynąć na cenę panela ze względu na proces technologiczny formowania blachy. Estetyka ma swoje wymagania, które czasami kosztują trochę więcej.
Reasumując, materiał i jego wykończenie to pierwsza i często największa pozycja wpływająca na exterior metal wall panels cost. Zrozumienie różnic między stalą nierdzewną, panelami stalowymi z różnymi powłokami, a także blachami o różnej grubości i fakturze, jest kluczowe dla świadomego podejmowania decyzji inwestycyjnych. Wybierając, warto patrzeć nie tylko na cenę za metr kwadratowy w danym momencie, ale także na przyszłe koszty utrzymania i oczekiwany cykl życia elewacji. Odpowiedni dobór materiału to fundament trwałej i estetycznej elewacji.
Rodzaj Rdzenia Izolacyjnego a Koszt Paneli
Gdy wybieramy panele warstwowe do ocieplenia elewacji, decydujemy nie tylko o zewnętrznej "skórze" budynku, ale przede wszystkim o jego termoizolacyjnym i, co równie ważne, pożarowym "sercu" – rdzeniu. Podobnie jak w samochodzie, gdzie cena i osiągi w dużej mierze zależą od silnika, tak w panelach warstwowych kluczowy wpływ na cenę i właściwości ma typ zastosowanego rdzenia izolacyjnego. To właśnie rdzeń odpowiada za parametry cieplne i reakcję na ogień, a co za tym idzie, za przyszłe koszty eksploatacji i bezpieczeństwo.
Najczęściej spotykane rodzaje rdzeni w panelach warstwowych to sztywna pianka poliuretanowa (PIR), wełna mineralna oraz styropian (EPS) – choć ten ostatni bywa rzadziej stosowany w elewacjach zewnętrznych z uwagi na niższe parametry ogniowe. Różnice między nimi są fundamentalne i przekładają się wprost na cenę zakupu paneli, a także na ich docelowe zastosowanie. Nie można po prostu wybrać najtańszej opcji bez analizy wymagań stawianych budynkowi, bo konsekwencje mogą być kosztowne i, co gorsza, niebezpieczne.
Panele warstwowe z rdzeniem PIR (Polyisocyanurate) są cenione przede wszystkim za swoje znakomite właściwości termoizolacyjne. Pianka PIR charakteryzuje się bardzo niskim współczynnikiem przenikania ciepła (lambda, λ), zazwyczaj w przedziale 0.022-0.024 W/(m·K). Oznacza to, że panel o danej grubości z rdzeniem PIR zapewnia lepszą izolacyjność cieplną niż panel o tej samej grubości z rdzeniem z wełny mineralnej czy EPS.
Wyższa efektywność termoizolacyjna paneli PIR pozwala często na zastosowanie mniejszej grubości panela do osiągnięcia wymaganego współczynnika U dla ściany, co może mieć wpływ na ogólny koszt materiałów i konstrukcji wsporczej. Przykładowo, aby osiągnąć U = 0.20 W/(m²·K) dla ściany, możemy potrzebować panela PIR o grubości 100 mm lub panela z wełną mineralną o grubości 140-150 mm. Mniejsza grubość panela to mniejsze obciążenie konstrukcji, często tańszy transport i łatwiejszy montaż, ale sam panel PIR per metr kwadratowy jest zazwyczaj droższy od panelu z wełną mineralną o tej samej grubości.
Standardowe panele warstwowe z rdzeniem PIR idą w parze z wyższą ceną w porównaniu do paneli z wełną mineralną o tej samej grubości. Wynika to z technologii produkcji i ceny samego surowca (policjanuranu). Ta różnica w cenie za metr kwadratowy może wynosić od 10 do nawet 30-40% na korzyść wełny mineralnej, w zależności od producenta i specyfikacji panela. Jednak pamiętajmy o efektywności: tańsza w zakupie wełna mineralna może wymagać większej grubości, co sumarycznie może zniwelować część tej różnicy, a nawet uczynić droższy panel PIR bardziej opłacalnym w kontekście osiągnięcia docelowej izolacji.
Panele warstwowe z rdzeniem z wełny mineralnej to z kolei mistrzowie odporności ogniowej. Wełna mineralna jest materiałem niepalnym (klasa reakcji na ogień A1). Jest to często kluczowy argument za jej wyborem w obiektach o podwyższonych wymaganiach przeciwpożarowych, takich jak magazyny wysokiego składowania, budynki użyteczności publicznej, obiekty przemysłowe czy ewakuacyjne drogi pożarowe. W takich przypadkach przepisy budowlane mogą wręcz wymuszać zastosowanie paneli z wełną mineralną o określonej odporności ogniowej (np. EI 30, EI 60, EI 120). Spełnienie tych norm może wpływać na koszt, gdyż panele z wełną mineralną spełniające wysokie wymagania ogniowe są droższe niż standardowe.
Współczynnik lambda dla wełny mineralnej jest wyższy niż dla PIR, oscylując zazwyczaj w granicach 0.039-0.045 W/(m·K). Oznacza to, że do osiągnięcia takiej samej izolacyjności termicznej jak panel PIR, potrzebujemy panela z wełną mineralną o większej grubości. Ta większa grubość przekłada się na większą wagę panela, co może wpływać na koszty transportu i wymagać solidniejszej konstrukcji wsporczej, co również generuje dodatkowe koszty.
Porównajmy ceny paneli o różnym rdzeniu, ale dążących do podobnego współczynnika U. Aby osiągnąć U = 0.25 W/(m²·K), możemy potrzebować panelu PIR o grubości 80 mm kosztującego np. 220 zł/m² lub panelu z wełną mineralną o grubości 120 mm kosztującego np. 250 zł/m². W tym hipotetycznym przypadku, panel z wełną mineralną jest droższy per metr kwadratowy, mimo niższej ceny bazowej "per grubość" w porównaniu do PIR. Decydując, inwestor musi zważyć priorytety: czy kluczowa jest efektywność termiczna przy mniejszej grubości panela (PIR), czy nadrzędna jest odporność ogniowa (wełna mineralna), akceptując potencjalnie większą grubość i wagę panelu?
Dodatkowo, na cenę panela z wełną mineralną może wpływać jej gęstość. Wyższa gęstość (np. 100-120 kg/m³) zapewnia lepsze parametry mechaniczne (większa sztywność, nośność) i akustyczne, ale jest też droższa od wełny o niższej gęstości (np. 80-90 kg/m³). Wybór gęstości wełny mineralnej powinien być podyktowany wymaganiami projektowymi, np. rozstawem elementów konstrukcji wsporczej, ale należy mieć świadomość, że ten parametr również ma odzwierciedlenie w cenie.
Panele z rdzeniem EPS (styropian) są zazwyczaj najtańszymi panelami warstwowymi. Mają przyzwoite parametry termoizolacyjne (choć zazwyczaj gorsze niż PIR) i są bardzo lekkie, co ułatwia montaż. Ich głównym ograniczeniem jest jednak niższa odporność ogniowa w porównaniu do PIR i wełny mineralnej. Są często stosowane w budynkach, gdzie przepisy przeciwpożarowe pozwalają na takie rozwiązania i gdzie budżet jest ograniczony, np. w niewielkich obiektach gospodarczych. Jednak w przypadku większości budynków komercyjnych i przemysłowych, szczególnie w Polsce, restrykcje dotyczące rozprzestrzeniania ognia po elewacji często wykluczają zastosowanie paneli EPS na dużą skalę.
Różnice w cenie paneli z poszczególnymi rdzeniami wynikają również z procesów produkcyjnych. Produkcja paneli PIR i z wełny mineralnej wymaga bardziej zaawansowanych technologii i maszyn niż produkcja paneli EPS, co również przekłada się na wyższe koszty produkcji, a w konsekwencji na wyższą cenę dla klienta.
Analizując oferty, natrafiamy czasem na rdzenie hybrydowe lub panele z sekcjami wykonanymi z różnych materiałów, np. część z wełny mineralnej (dla odporności ogniowej), a część z PIR (dla lepszej izolacji termicznej). Takie niestandardowe rozwiązania są zazwyczaj droższe niż panele jednorodnym rdzeniem, ale pozwalają optymalnie połączyć pożądane właściwości w ramach jednej przegrody.
Kolejnym aspektem jest dostępność materiałów. Czasem, w zależności od globalnej sytuacji na rynku surowców, ceny komponentów do produkcji PIR mogą dynamicznie rosnąć, wpływając na cenę paneli. Podobnie ceny wełny mineralnej mogą być uzależnione od dostępności bazaltu i cen energii potrzebnej do jej produkcji. Dlatego warto monitorować rynek i brać pod uwagę potencjalne fluktuacje cen w momencie planowania inwestycji. Zmienność cen surowców to coś, co zawsze trzeba mieć z tyłu głowy.
Z mojej perspektywy, jako eksperta obserwującego rynek od lat, wybór rdzenia to zawsze balans między ceną, wymaganą izolacją termiczną a bezpieczeństwem pożarowym. Najdroższy panel nie zawsze jest najlepszy – najlepszy jest panel optymalnie dobrany do specyfiki projektu i obowiązujących przepisów. Wartości współczynników lambda i klasyfikacja ogniowa (np. wg normy PN-EN 13501-1) powinny być tutaj drogowskazem, a nie tylko pusta informacja techniczna. Pamiętaj, że oszczędność na bezpieczeństwie pożarowym może mieć katastrofalne skutki.
Producenci paneli warstwowych często oferują pełne wsparcie techniczne, w tym obliczenia niezbędnej grubości i typu rdzenia dla uzyskania wymaganych parametrów termicznych i pożarowych dla danego projektu. Korzystanie z tej wiedzy jest nie tylko bezpłatne, ale wręcz konieczne, aby uniknąć kosztownych błędów na etapie projektowania i zakupu paneli. Nie ma sensu zgadywać – poproś o fachową poradę, a zaoszczędzisz czas, pieniądze i nerwy.
Reasumując wpływ rdzenia izolacyjnego na exterior metal wall panels cost, wiedz, że wybierając PIR płacisz więcej za wysoką izolacyjność cieplną i mniejszą grubość. Wybierając wełnę mineralną, inwestujesz w nadrzędne bezpieczeństwo pożarowe, często akceptując większą grubość panela, która także wpływa na cenę. Rdzeń EPS to opcja budżetowa, ograniczona przez przepisy ppoż. Pamiętaj, że cena to tylko część równania – druga to spełnienie wymagań technicznych i prawnych oraz długoterminowe oszczędności na ogrzewaniu lub chłodzeniu budynku, a także bezpieczeństwo ludzi i mienia.
Grubość Paneli a Koszt
Grubość paneli warstwowych to kolejny, bezpośredni i namacalny czynnik wpływający na ich cenę. Zasada jest prosta i logiczna – im grubszy panel, tym więcej materiału zużyto do jego produkcji, a co za tym idzie, tym wyższy jest jego koszt zakupu per metr kwadratowy. To jak z płaszczem zimowym – grubsza wyściółka zapewni lepszą izolację termiczną, ale też będzie droższa od cieńszego odpowiednika. W przypadku paneli elewacyjnych ta grubość ma kluczowe znaczenie nie tylko dla ceny, ale i dla kluczowych parametrów technicznych, zwłaszcza termoizolacyjności.
Standardowe grubości paneli warstwowych stosowanych na ściany wahają się zazwyczaj od 40 mm do 200 mm, choć dostępne są również panele cieńsze (np. 30 mm, często do zastosowań wewnętrznych) i znacznie grubsze (nawet do 300 mm i więcej, głównie do chłodni i mroźni). W przedziale grubości 60 mm do 120 mm znajdziemy rozwiązania najczęściej stosowane w standardowym budownictwie przemysłowym, magazynowym i handlowym w klimacie umiarkowanym.
Bezpośredni związek między grubością a ceną jest niezaprzeczalny. Panel o grubości 100 mm jest droższy od panelu o grubości 80 mm wykonanego z tego samego materiału (ta sama okładzina, ten sam typ rdzenia), który z kolei jest droższy od panela 60 mm. Producenci często podają cenniki z podziałem na grubości, wyraźnie wskazując wzrost ceny z każdym kolejnym milimetrem czy centymetrem grubości rdzenia. Przyrost ceny nie jest zazwyczaj liniowy i wpływa na cenę coraz bardziej odczuwalnie przy większych grubościach.
Dlaczego decydujemy się na większą grubość? Przede wszystkim dla uzyskania lepszych parametrów izolacyjnych. Współczynnik przenikania ciepła U [W/(m²·K)] jest wprost proporcjonalny do grubości warstwy izolacyjnej (i odwrotnie proporcjonalny do współczynnika lambda rdzenia). Im grubszy rdzeń o niskiej lambdzie, tym niższa wartość U, a więc lepsza izolacja termiczna ściany. Przy dzisiejszych wymaganiach dotyczących efektywności energetycznej budynków, coraz częściej projektuje się ściany o bardzo niskich wartościach U, co wymusza stosowanie paneli o znacznej grubości, zwłaszcza z rdzeniem z wełny mineralnej, który ma wyższą lambdę niż PIR.
Przykładowo, panele z rdzeniem PIR mają lambdę około 0.022 W/(m·K). Aby uzyskać U = 0.20 W/(m²·K) dla ściany, potrzebna jest grubość rdzenia około 110 mm. Jeśli chcemy osiągnąć U = 0.15 W/(m²·K), grubość rdzenia musi wzrosnąć do około 145 mm. Dla paneli z wełną mineralną o lambdzie około 0.044 W/(m·K), aby uzyskać U = 0.20 W/(m²·K) potrzebujemy rdzenia o grubości około 210 mm! Widać wyraźnie, że dążenie do coraz lepszej izolacyjności wiąże się z proporcjonalnym, a czasami nawet nieliniowym wzrostem grubości panela, co automatycznie zwiększa exterior metal wall panels cost per m².
Weźmy konkretne dane. Panel PIR o grubości 80 mm (U ok. 0.28 W/(m²·K)) może kosztować np. 220 zł/m². Panel PIR 120 mm (U ok. 0.19 W/(m²·K)) tego samego producenta i o tym samym wykończeniu może kosztować już 280-320 zł/m². Panel PIR 160 mm (U ok. 0.14 W/(m²·K)) może przekroczyć 350 zł/m². Różnica w cenie za metr kwadratowy między panelem 80 mm a 160 mm, mając lepszą izolację, wynosi ponad 50%!
Ta inwestycja w grubość panela, choć zwiększa koszt zakupu, ma jednak kluczowe znaczenie dla przyszłych kosztów eksploatacji budynku, przede wszystkim związanych z ogrzewaniem i chłodzeniem. Budynek z dobrze izolowaną przegrodą o niskim współczynniku U będzie zużywał znacznie mniej energii na utrzymanie komfortowej temperatury wewnątrz. W długim okresie oszczędności na rachunkach za energię mogą z nawiązką zrekompensować wyższy początkowy koszt zakupu paneli o większej grubości. To klasyczny przykład, gdy pozorna oszczędność na etapie inwestycji przekłada się na wyższe koszty w trakcie użytkowania obiektu – syndrom "taniego domu", który później pochłania fortunę na ogrzewanie.
Grubość paneli wpływa również na ich parametry mechaniczne – przede wszystkim na sztywność i nośność. Grubsze panele mogą przenosić większe obciążenia (np. wiatr, obciążenie dachem w przypadku montażu na skosach) i pozwalają na zastosowanie większego rozstawu między elementami konstrukcji wsporczej (ryglami ściennymi), na których są mocowane. Zwiększenie rozstawu rygli może potencjalnie zmniejszyć ilość potrzebnej stali na konstrukcję budynku, co częściowo zniweluje wyższy koszt grubszych paneli. Czasem droższy, ale grubszy panel pozwala na optymalizację konstrukcji nośnej, co w sumie może dać korzystniejszy efekt ekonomiczny. To element, który wymaga skoordynowanego projektowania architektonicznego i konstrukcyjnego.
Producenci paneli udostępniają tabele nośności dla poszczególnych grubości i rodzajów rdzeni, określające maksymalny rozstaw rygli dla danego obciążenia. Projektant konstrukcyjny musi wybrać taką grubość panelu, która sprosta przewidywanym obciążeniom i pozwoli na przyjęty rozstaw konstrukcji nośnej. Czasem minimalna wymagana grubość panela może być podyktowana nie tylko izolacyjnością termiczną, ale właśnie warunkami nośnościowymi.
Nie bez znaczenia jest też transport i montaż paneli o dużej grubości. Są one cięższe i bardziej nieporęczne, co może generować wyższe koszty transportu (mniejsza ilość na jednej ciężarówce) i wymagać użycia cięższego sprzętu (np. większych dźwigów czy ładowarek teleskopowych) do ich podnoszenia i precyzyjnego układania na elewacji. Te dodatkowe koszty montażu powinny być uwzględnione w całkowitym koszcie elewacji.
Grubsze panele wymagają również dłuższych łączników montażowych (śrub, wkrętów), które również są droższe. Chociaż koszt łączników w stosunku do całego projektu elewacji jest niewielki, przy bardzo dużej powierzchni nawet drobna różnica w cenie pojedynczego elementu może zsumować się do zauważalnej kwoty. Diabeł, jak to zwykle bywa, tkwi w szczegółach i sumie drobnych pozycji.
W niektórych przypadkach, zwłaszcza przy projektach termomodernizacyjnych, konieczność osiągnięcia bardzo niskiego współczynnika U dla spełnienia obecnych przepisów może oznaczać konieczność zastosowania paneli o grubości przekraczającej standardowe zakresy, np. 200 mm PIR. Takie panele są droższe, mniej powszechnie dostępne i ich transport oraz montaż stają się większym wyzwaniem logistycznym i finansowym. Ale alternatywa (np. murowanie grubszych ścian z tradycyjnych materiałów izolacyjnych) często okazuje się jeszcze droższa i bardziej czasochłonna.
Mój własny tok myślenia, kiedy analizuję projekty, zawsze prowadzi do pytania: jaka grubość panela jest OPTYMALNA, a nie tylko minimalna czy maksymalna? Optymalna grubość to taka, która równoważy koszt zakupu paneli z wymaganymi parametrami izolacyjnymi, nośnościowymi oraz przyszłymi kosztami eksploatacji i kosztem montażu. Nie zawsze największa grubość jest ekonomicznie uzasadniona, podobnie jak najmniejsza grubość może generować olbrzymie koszty ogrzewania w przyszłości. Analiza cyklu życia budynku (LCA) jest tutaj bardzo pomocnym narzędziem decyzyjnym, choć rzadko stosowanym przy mniejszych projektach. Ale nawet intuicyjne rozważenie "co mi się bardziej opłaca na przestrzeni 15-20 lat" jest lepsze niż wybór w ciemno.
Reasumując, grubość paneli ma bezpośredni i znaczący wpływ na exterior metal wall panels cost. Większa grubość oznacza wyższy koszt zakupu, ale jednocześnie lepszą izolację termiczną i większą nośność. Decyzja o grubości paneli powinna być podyktowana wymaganiami normatywnymi dotyczącymi izolacyjności i bezpieczeństwa pożarowego, a także potrzebami konstrukcyjnymi, przy jednoczesnym uwzględnieniu długoterminowych kosztów eksploatacji i potencjalnej optymalizacji konstrukcji nośnej. To kluczowy element, który wymaga ścisłej współpracy między inwestorem, projektantem i dostawcą paneli.
Koszty Montażu i Elementy Dodatkowe
Kiedy już wybierzemy materiał paneli, rdzeń izolacyjny i optymalną grubość, wydaje się, że największe decyzje cenowe są za nami. Nic bardziej mylnego! Koszty montażu i zakupu elementów dodatkowych stanowią znaczącą część całkowitego kosztu elewacji i w żadnym wypadku nie można o nich zapominać. Myślenie, że "panel kupiony, reszta to drobiazgi" jest pułapką, w którą wpadło wielu inwestorów. To trochę jak kupić drogie auto i zapomnieć o koszcie ubezpieczenia i paliwa.
Chociaż panele warstwowe są znane z szybkości i prostoty montażu w porównaniu do tradycyjnych technologii murowych czy tynkowych – co jest ich ogromnym atutem przekładającym się na oszczędności w kosztach robocizny i szybsze oddanie obiektu do użytku – to jednak sam proces instalacji generuje niemałe wydatki. Potrzebna jest przecież wykwalifikowana ekipa montażowa, specjalistyczny sprzęt i niezbędne akcesoria. Cena za montaż metra kwadratowego panela może być bardzo zróżnicowana w zależności od regionu, złożoności projektu, wysokości budynku czy specyfiki elewacji (np. liczne detale, okna, bramy). Zazwyczaj koszt robocizny za montaż paneli elewacyjnych waha się od 50 do nawet 100+ zł/m² brutto. Przy elewacji o powierzchni 2000 m² to już kwota rzędu 100 000 - 200 000 zł tylko za robociznę.
Na koszt robocizny wpływa także dostępność do elewacji. Prace na wysokościach wymagają użycia podnośników nożycowych, teleskopowych, a nawet rusztowań lub specjalistycznych podestów, co generuje koszty wynajmu lub zakupu tego sprzętu. Im wyższy budynek, tym trudniejszy i droższy montaż. Elewacje parterowe czy dwukondygnacyjne są znacznie tańsze w montażu niż wieżowce czy budynki wymagające alpinistów przemysłowych.
Elementy mocujące generują dodatkowe wydatki. Mowa tu o śrubach, wkrętach samowiercących i samogwintujących, uszczelkach, taśmach rozprężnych i innych akcesoriach niezbędnych do prawidłowego i szczelnego zamocowania paneli do konstrukcji nośnej. Rodzaj i ilość łączników zależy od typu panela, obciążeń (wiatr, śnieg) i rodzaju konstrukcji wsporczej (stalowa, betonowa, drewniana). Chociaż koszt pojedynczej śruby to ułamek złotówki, na metr kwadratowy elewacji przypada ich zazwyczaj kilka sztuk, a na dużą powierzchnię tysiące. Koszt łączników może wynieść od kilku do kilkunastu złotych na metr kwadratowy elewacji.
Dodatkowe koszty generuje obróbka detali, czyli elementów maskujących i uszczelniających w narożach budynku, wokół okien, bram, drzwi, a także wzdłuż cokołu czy dachu. Obróbki blacharskie wykonane z blachy w kolorze paneli są absolutnie niezbędne dla estetyki, szczelności i trwałości elewacji. Są one zazwyczaj wyceniane na metry bieżące. Ich ilość i złożoność zależy od geometrii budynku. Prosty "pudełkowy" budynek będzie wymagał mniej obróbek niż obiekt o skomplikowanym kształcie, z wieloma przeszkleniami czy załamaniami ścian.
Cena obróbek blacharskich zależy od typu materiału (stal, aluminium, stal nierdzewna), powłoki, koloru oraz kształtu profilu (standardowy, czy wymagający niestandardowego gięcia na wymiar). Proste kątowniki maskujące są tańsze od skomplikowanych profili "Z", "U" czy dedykowanych listew maskujących. Koszt obróbek może wahać się od 20-30 zł za metr bieżący prostego profilu do ponad 100 zł za metr bieżący elementu niestandardowego czy wykonanego ze stali nierdzewnej.
Niektóre projekty wymagają zastosowania specjalistycznych systemów montażowych, np. systemów wentylowanych fasad (jeśli panele są częścią bardziej złożonej konstrukcji), systemów mocowania w nietypowy sposób (np. niewidoczne mocowanie). Te specjalistyczne rozwiązania są zazwyczaj droższe od standardowego montażu na widoczne łączniki.
Koszty transportu paneli na budowę również należy wliczyć w exterior metal wall panels cost. Zależą one od odległości, wielkości zamówienia i możliwości rozładunku na placu budowy. Dłuższe i grubsze panele wymagają dłuższego transportu i często specjalistycznego rozładunku (np. dźwigiem). Koszt transportu na dużym projekcie może sięgnąć nawet kilku czy kilkunastu procent wartości zamówionych paneli.
W kontekście montażu nie można pominąć kosztów związanych z przygotowaniem podłoża, czyli konstrukcji nośnej. Choć ten element nie wchodzi w cenę paneli, jest nierozerwalnie związany z całością projektu elewacji. Koszt zakupu i montażu rygli stalowych, betonowych słupów czy drewnianej podkonstrukcji pod panele również musi być ujęty w całkowitym koszcie elewacji.
Wspomniałem o szybkości montażu jako zalecie paneli warstwowych. I to prawda! Podczas gdy murowanie i tynkowanie elewacji potrwa tygodnie, a nawet miesiące (z uwzględnieniem przerw technologicznych, warunków pogodowych), montaż paneli warstwowych na przygotowaną konstrukcję nośną na hali o powierzchni kilku tysięcy metrów kwadratowych może zająć zaledwie kilka do kilkunastu dni roboczych. Ta szybkość przekłada się na gigantyczne oszczędności czasu i pieniędzy. Mniej dni pracy ekipy to niższe koszty robocizny. Szybsze zakończenie budowy oznacza wcześniejsze uruchomienie działalności w budynku, co dla inwestora generuje szybszy zwrot z inwestycji i brak strat wynikających z opóźnień. Ten aspekt często umyka w analizie kosztów, skupiając się tylko na cenie samego materiału czy robocizny. Czas to pieniądz, szczególnie w biznesie.
Wyobraźmy sobie: dwie identyczne hale o powierzchni 1000 m² każda. Jedna w tradycyjnej technologii murowanej z ociepleniem, druga w systemie paneli warstwowych. Elewacja tradycyjna wymagałaby pracy 5-osobowej ekipy przez ok. 6-8 tygodni (murowanie, ocieplenie, tynki, malowanie) – powiedzmy, że koszt robocizny to łącznie 80 000 zł. Elewacja z paneli warstwowych dla 5-osobowej ekipy to ok. 10-12 dni roboczych – koszt robocizny ok. 20 000-25 000 zł. Oszczędność na samej robociźnie elewacyjnej sięga 55 000-60 000 zł, nie wspominając o wcześniejszym dostępie do hali. To argument, który przemawia do wyobraźni każdego, kto choć raz zmagał się z przeciągającą się budową.
Dodatkowe koszty paneli elewacyjnych mogą obejmować również takie pozycje jak transport specjalistyczny (np. ponadgabarytowy), wynajem dodatkowego sprzętu (dźwigi o większym udźwigu), koszty utylizacji odpadów opakowaniowych czy specjalistyczne ubezpieczenie budowy obejmujące ryzyko związane z montażem paneli na wysokości. Każdy projekt jest inny i wymaga indywidualnego podejścia do kalkulacji kosztów montażu i elementów dodatkowych.
Do kosztów montażu należy również wliczyć koszt prac przygotowawczych na placu budowy, takich jak utwardzenie dróg dojazdowych dla ciężarówek z panelami, przygotowanie miejsca składowania paneli (powinny być składowane na płaskim, suchym podłożu, często na legarach, zabezpieczone przed warunkami atmosferycznymi), wynajem kontenerów na odpady czy zapewnienie zaplecza socjalnego dla ekipy montażowej. To wszystko ma wpływ na ostateczną kwotę projektu.
Podsumowując kwestię kosztów montażu i elementów dodatkowych – są to pozycje w kosztorysie, które mogą znacząco wpłynąć na ostateczny wydatek. Choć panele warstwowe oferują oszczędności czasu i kosztów robocizny dzięki szybkiemu montażowi, nie można pominąć kosztów samej robocizny za m², elementów mocujących, obróbek blacharskich, transportu, wynajmu sprzętu i przygotowania placu budowy. Staranna kalkulacja tych elementów jest kluczowa dla prawidłowego zaplanowania budżetu inwestycji. Pamiętajmy, że dobrze zamontowane panele to gwarancja szczelnej, trwałej i estetycznej elewacji na długie lata. Oszczędzanie na jakości montażu czy niezbędnych elementach dodatkowych to proszenie się o problemy w przyszłości.
Dla lepszego zobrazowania, jak rozkładają się przykładowe koszty elewacji z paneli warstwowych, można spojrzeć na uproszczony rozkład procentowy na przykładowej hali magazynowej:
- Koszt zakupu paneli (materiał, rdzeń, grubość): 50-65% ostatecznej sumy
- Koszt zakupu obróbek blacharskich: 10-15%
- Koszt zakupu elementów mocujących (śruby, uszczelki itp.): 2-5%
- Koszt transportu paneli i akcesoriów: 3-7%
- Koszt robocizny (montaż paneli, obróbek): 15-25%
- Koszty dodatkowe (sprzęt, przygotowanie placu itp.): 2-5%
Procentowe udziały są oczywiście orientacyjne i mogą się znacząco różnić w zależności od specyfiki projektu (np. bardzo skomplikowana elewacja z mnóstwem obróbek vs. prosta hala). Warto jednak mieć świadomość, że cena paneli na fakturze od producenta to tylko część układanki. Całość to suma tych wszystkich składowych. Nie da się precyzyjnie określić exterior metal wall panels cost bez uwzględnienia wszystkich tych elementów. Planowanie budżetu bez szczegółowej analizy montażu i elementów dodatkowych jest jak planowanie wyjazdu na wakacje bez uwzględnienia kosztów wyżywienia czy atrakcji na miejscu – można się srogo rozczarować finalną kwotą.