Czy Na Płytki Można Położyć Panele Laminowane?
Pomyśl o tej chwili. Patrzysz na swoje stare, być może już nieco wysłużone, płytki ceramiczne i wzdychasz, marząc o cieplejszej, nowocześniejszej i cichszej podłodze z paneli laminowanych. Czy to oznacza jedyny scenariusz – skuwanie, tuman kurzu, tygodnie remontowego chaosu i góra gruzu do wywozu? Na szczęście rzeczywistość budowlana, choć bywa bezlitosna, czasem otwiera przed nami mniej inwazyjne drzwi. Odpowiadając wprost na palące pytanie "czy na płytki można położyć panele laminowane?", z ulgą donosimy: tak, jest to w zdecydowanej większości przypadków możliwe i stanowi atrakcyjną alternatywę dla tradycyjnego remontu. Ten artykuł to nasz wspólny kompas po meandrach tego procesu, rozwiewający wątpliwości i wskazujący drogę do wymarzonej podłogi bez zbędnej rewolucji.
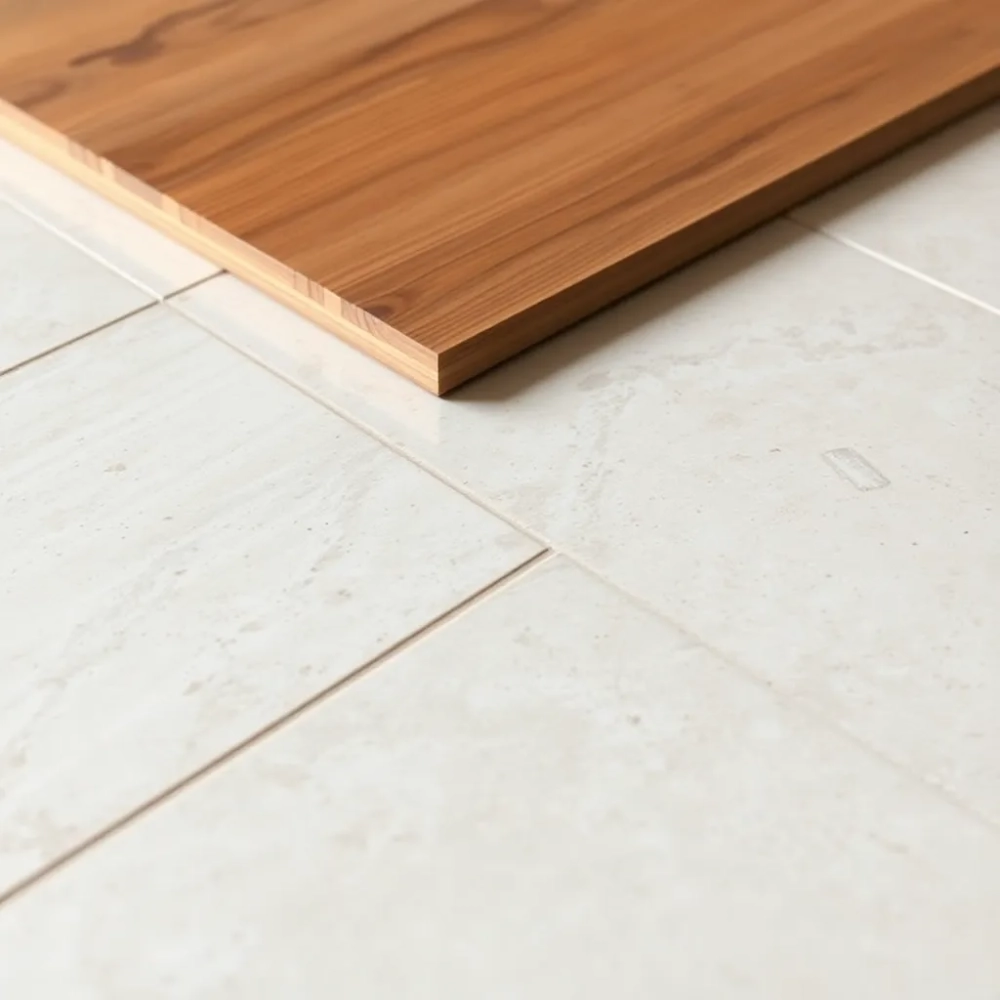
W przestrzeni remontowej, gdzie czas i budżet często odgrywają rolę nie mniejszą niż jakość materiałów, zdolność adaptacji do istniejących warunków bywa na wagę złota. Analizując setki, a nawet tysiące projektów renowacyjnych, w których inwestorzy decydowali się na metamorfozę podłogi z ceramicznej na laminowaną, wyraźnie rysuje się tendencja preferowania metody "na istniejącej warstwie". Nie jest to bynajmniej lenistwo, a często pragmatyczne podejście, poparte wymiernymi korzyściami, które udało się skwantyfikować w naszych studiach przypadków.
Aspekt Projektu | Układanie Paneli na Płytkach (w przeliczeniu na 50 m²) | Usunięcie Płytek + Przygotowanie Podłoża (w przeliczeniu na 50 m²) |
---|---|---|
Szacowany Czas Wykonania Etapu Podłoża | 4-16 godzin (sprawdzenie, naprawa drobnych usterek, sprzątanie) | 2-5 dni (skuwanie, wyniesienie gruzu, sprzątanie, gruntowanie, wylewka/masa samopoziomująca, czas schnięcia) |
Orientacyjny Dodatkowy Koszt Materiałów (poza panelami i listwami) | Ok. 20-50 zł/m² (folia PE o grubości 0.2mm, podkład akustyczny o dobrych parametrach) | Ok. 50-150+ zł/m² (worki na gruz, kontener/wywóz, materiały naprawcze/wypełniacze, grunt, masa samopoziomująca o zwiększonej wytrzymałości, narzędzia do skuwania/mieszania) |
Poziom Generowanego Bałaganu (kurz, gruz) | Minimalny do Niskiego (głównie sprzątanie po naprawie ubytków) | Ekstremalny (pył unosi się wszędzie, ogromne ilości gruzu) |
Typowe Ryzyka Procesu | Błędy w przygotowaniu podłoża (ukryte nierówności, wilgoć), pominięcie paroizolacji/podkładu. | Uszkodzenie instalacji podłogowych, błędy w przygotowaniu wylewki/masy, nierówności w nowej warstwie, długi czas schnięcia. |
Dane te dobitnie pokazują, że pominięcie etapu rozbiórki przynosi wymierne oszczędności, zarówno w portfelu, jak i kalendarzu. To nie tylko szybszy sposób na nową podłogę, ale często po prostu mniej obciążający domowników i sąsiadów. Niemniej jednak, sukces tej operacji opiera się na bezkompromisowej dbałości o szczegóły na kolejnych etapach, o których opowiemy poniżej. Każdy pominięty czy zaniedbany krok może słono kosztować w przyszłości, objawiając się skrzypieniem, deformacją paneli, a nawet zniszczeniem podłogi. To jak w medycynie – diagnoza i przygotowanie są kluczem do skutecznego leczenia, a w naszym przypadku – do trwałej i estetycznej podłogi.
Przejdźmy zatem przez poszczególne etapy, aby zrozumieć, jak bezpiecznie i skutecznie przeprowadzić tę metamorfozę.
Pierwszy Krok: Aklimatyzacja Paneli
Zanim pierwszy panel "kliknie" na swoje miejsce, musimy pozwolić mu "odpocząć". Pamiętam projekt w starej kamienicy, gdzie właściciel, zafascynowany nowo nabytymi panelami, zaczął montaż prosto po odebraniu dostawy. Efekt? Po kilku tygodniach pojawiły się nienaturalne wybrzuszenia i szczeliny. Lekcja była bolesna i kosztowna.
Konieczność aklimatyzacji wynika z higroskopijności materiałów drzewnych, z których w dużej mierze składają się panele laminowane (rdzeń z HDF, czyli płyty wysokiej gęstości). Materiał ten "pracuje", reagując na zmiany wilgotności i temperatury otoczenia. Producenci paneli, świadomi tej właściwości, zalecają pozostawienie zamkniętych paczek w docelowym pomieszczeniu na określony czas, zazwyczaj minimum 48 godzin, chociaż 24 godziny są często podawane jako absolutne minimum dla standardowych paneli o grubości 7-8 mm. Dla grubszych paneli (10-12 mm i więcej) lub w pomieszczeniach o wyraźnie różniących się warunkach od miejsca przechowywania, czas ten może być dłuższy, dochodząc nawet do 72 godzin.
Optymalne warunki do aklimatyzacji to temperatura pokojowa, zazwyczaj w przedziale 18-25°C, oraz stabilna wilgotność powietrza, mieszcząca się w przedziale 40-60%. Upewnij się, że system ogrzewania lub klimatyzacji w pomieszczeniu, gdzie będą montowane panele, pracuje w sposób stabilny przez cały okres aklimatyzacji. Unikaj skrajności – nie kładź paczek paneli bezpośrednio na zimnej posadzce (co jest ryzykiem właśnie przy układaniu na płytkach w chłodnym sezonie grzewczym) ani tuż przy źródłach ciepła, takich jak grzejniki.
Panele powinny być składowane w oryginalnych, nieotwartych paczkach. Układaj je poziomo, płasko, najlepiej na suchych, stabilnych podkładkach lub palecie. Rozpakowanie ich zbyt wcześnie narazi poszczególne deski na nierównomierne wchłanianie wilgoci, co może prowadzić do wypaczania się elementów jeszcze przed rozpoczęciem montażu. Myśl o tym jak o gotowaniu – niektórych składników nie można dodawać za wcześnie, muszą czekać na swoją kolej w odpowiednich warunkach, aby danie się udało.
Brak odpowiedniej aklimatyzacji to proszenie się o kłopoty. Panele ułożone w momencie, gdy ich wilgotność odbiega znacząco od wilgotności docelowej w pomieszczeniu, będą "pracować" już po montażu. Jeśli wchłoną wilgoć, zwiększą objętość, prowadząc do wybrzuszeń i „łódkowania” podłogi, zwłaszcza przy ścianach lub w progach, jeśli szczelina dylatacyjna będzie za mała. Jeśli oddadzą wilgoć (np. po przeniesieniu z wilgotnego magazynu do suchego, ogrzewanego mieszkania), skurczą się, co zaowocuje nieestetycznymi szczelinami między deskami, których nie usunie żadne późniejsze działanie.
Podczas aklimatyzacji zwróć uwagę na pomieszczenia o podwyższonej wilgotności, takie jak łazienki (choć panele laminowane nie są najlepszym wyborem do typowych łazienek ze względu na wilgoć, to w niektórych aranżacjach np. sucha część WC czy pralni bywają rozważane) czy kuchnie. Warunki w tych miejscach są bardziej wymagające, co podkreśla potrzebę starannej aklimatyzacji i wyboru paneli o odpowiednich parametrach wilgotnościowych, jeśli są dostępne.
Dlaczego aklimatyzacja jest tak ważna, gdy kładziemy panele laminowane na płytki? Chociaż płytki same w sobie są materiałem stabilnym wymiarowo, stanowią twardą, często chłodniejszą barierę, która może wpływać na mikroklimat tuż przy podłodze. Panele, leżąc bezpośrednio na nich (choć z podkładem i paroizolacją), muszą dostosować się do temperatury i wilgotności całego pomieszczenia, ale też minimalnie uwzględnić warunki specyficzne dla kontaktu z zimniejszym (lub cieplejszym w przypadku ogrzewania podłogowego) podłożem.
Dobrym pomysłem jest sprawdzenie wilgotności podłoża z płytek oraz powietrza w pomieszczeniu za pomocą odpowiedniego miernika. Chociaż płytki są nienasiąkliwe, szczeliny fugowe mogą przewodzić wilgoć z głębszych warstw podłogi, a w przypadku starszych budynków czy piwnic, płytki położone bezpośrednio na betonie mogą oddawać resztkową wilgoć. Pamiętajmy, że panele są wrażliwe, a ich HDFowy rdzeń działa trochę jak gąbka dla wilgoci. Dostosowanie się do warunków przed montażem minimalizuje ryzyko późniejszych, nieprzewidzianych deformacji.
Podsumowując ten pierwszy, często niedoceniany etap: poświęcenie dodatkowych 2-3 dni na aklimatyzację to niewielka cena w porównaniu do potencjalnych problemów i kosztów związanych z naprawą podłogi, która zdeformowała się po kilku tygodniach użytkowania. Traktuj panele jak żywe drewno – potrzebują czasu, aby "odetchnąć" i przyzwyczaić się do nowego "domu" zanim zostaną trwale zainstalowane. To absolutny fundament sukcesu przy układaniu podłogi pływającej.
Przygotowanie Podłoża Z Płytek
Przejdźmy do sedna sprawy, czyli do samego podłoża – naszych dotychczasowych płytek. Złota zasada brzmi: nowa podłoga jest tak dobra, jak jej podstawa. Ignorowanie stanu istniejącej posadzki ceramicznej to prosta droga do rozczarowania. Pamiętacie stare powiedzenie "diabeł tkwi w szczegółach"? Tutaj jest ono bardziej niż prawdziwe.
Pierwsza, i chyba najważniejsza kwestia, to stabilność płytek. Czy wszystkie płytki są solidnie przytwierdzone do podłoża? Chodź po całej powierzchni przeznaczonej pod panele, stukając delikatnie młotkiem (nylonowym lub gumowym) lub nawet rękojeścią śrubokręta w różne miejsca na każdej płytce, zwłaszcza na rogach i środku. Głuchy odgłos, w odróżnieniu od dźwięcznego "dzwonienia", często świadczy o odspojeniu płytki od kleju. Takie płytki to bomby z opóźnionym zapłonem dla naszej nowej podłogi. Będą się ruszać pod naciskiem, powodując skrzypienie paneli i ostatecznie prowadząc do pękania zamków lub nawet uszkodzenia samych paneli w miejscach naprężeń.
Co zrobić z takimi "luźnymi strzelcami"? Niestety, trzeba je usunąć. Odkuj ostrożnie odspojone płytki. Oczyść podłoże pod nimi z resztek starego kleju i kurzu. Powstałe ubytki należy następnie uzupełnić. Idealnie, jeśli użyjemy szybko schnącej masy naprawczej lub wylewki samopoziomującej przeznaczonej do stosowania w cienkich warstwach. Uzupełniona powierzchnia musi być równa z poziomem pozostałych płytek i stabilna. Drobne ubytki w fugach, które nie ruszają się pod naciskiem, zazwyczaj nie wymagają interwencji, chyba że są bardzo szerokie i głębokie.
Kolejny krytyczny aspekt to równość podłoża. Laminat jest tolerancyjny na nierówności tylko do pewnego stopnia. Standardowo większość producentów paneli laminowanych dopuszcza odchyłki od płaszczyzny na poziomie maksymalnie 2-3 milimetrów na długości 2 metrów. Jak to sprawdzić? Weź długą, prostą łatę lub poziomicę (minimum 2 metrową) i przykładaj ją do podłogi w różnych kierunkach – wzdłuż, w poprzek i na skos pomieszczenia. Wszelkie prześwity większe niż wspomniane 2-3 mm wymagają interwencji.
Jeśli nierówności są większe, mamy dwa wyjścia. Po pierwsze, spróbować punktowo szlifować lub frezować wystające fragmenty (np. garby po kleju). Po drugie, a częściej konieczne, użyć masy samopoziomującej. Tak, można zastosować masę samopoziomującą na płytki! Wymaga to jednak odpowiedniego przygotowania – płytki muszą być czyste, odtłuszczone i koniecznie zagruntowane specjalnym gruntem zwiększającym przyczepność do gładkich, nienasiąkliwych powierzchni. Masę należy wylać zgodnie z instrukcją producenta, upewniając się, że minimalna grubość wylewki będzie wystarczająca do zakrycia największych nierówności i że masa jest przeznaczona do tego typu zastosowań.
Czas schnięcia masy samopoziomującej jest kluczowy i nie wolno go skracać. Zazwyczaj wynosi od 24 godzin do kilku dni, w zależności od grubości warstwy, temperatury i wilgotności. Wilgotność resztkowa podkładu betonowego (jeśli płytki były na nim kładzione) lub samej masy samopoziomującej może negatywnie wpłynąć na panele, nawet jeśli użyjemy paroizolacji.
Poza stabilnością i równością, nie zapomnijmy o czystości. Podłoże z płytek musi być idealnie czyste, wolne od kurzu, tłuszczu, farby czy resztek kleju. Wszystko, co znajdzie się pod panelem, nawet niewielki kamyk, będzie tworzyło punktowy nacisk, który z czasem może objawić się jako "kliknięcie" pod stopą, a w skrajnych przypadkach – uszkodzeniem zamka. Dokładne odkurzenie i umycie (a w przypadku tłustych zabrudzeń odtłuszczenie np. acetonem technicznym lub specjalnym preparatem) jest obowiązkowe. Myjka parowa może być pomocna w usunięciu zaschniętych zabrudzeń w fugach, ale upewnij się, że podłoże jest całkowicie suche przed położeniem kolejnych warstw.
Fugi między płytkami, jeśli są standardowej szerokości (do kilku mm) i nie są popękane ani wykruszone, zazwyczaj nie stanowią problemu same w sobie dla nowoczesnych podkładów pod panele o dobrej wytrzymałości na ściskanie. Te podkłady są w stanie mostkować takie niewielkie szczeliny. Jednak bardzo szerokie fugi lub fugi o dużej głębokości mogą wymagać uzupełnienia elastyczną masą fugową lub cienką warstwą wspomnianej masy samopoziomującej na całej powierzchni, aby stworzyć bardziej jednolitą bazę dla podkładu.
Wrażliwość laminatu na wilgoć jest cechą inherentną jego konstrukcji. Choć powierzchnia jest chroniona warstwą żywicy melaminowej (wysoce odpornej na ścieranie i zaplamienie), boki i spód paneli, czyli rdzeń HDF, są jej wrogiem numer jeden. Woda, która dostanie się pod panel, może spowodować puchnięcie krawędzi i trwałe deformacje. Dlatego odpowiednie przygotowanie podłoża, eliminujące wszelkie potencjalne źródła wilgoci (np. przeciekające fugi, resztkowa wilgoć w podkładzie), jest krytyczne, nawet zanim pomyślimy o barierze paroizolacyjnej, która stanowi dodatkową linię obrony.
Reasumując, przygotowanie podłoża z płytek pod panele to proces, który wymaga detektywistycznej dociekliwości i gotowości do pracy "na kolanach". Sprawdzenie każdej płytki, niwelacja nierówności i perfekcyjne wyczyszczenie powierzchni to fundament, bez którego cała reszta wysiłku może pójść na marne. Zainwestowany czas i praca na tym etapie zwrócą się w postaci trwałej, równej i bezproblemowej podłogi przez długie lata.
Bariera Paroizolacyjna (Folia PE)
Kiedy podłoże z płytek jest już równe, stabilne i czyste jak łza, przychodzi czas na kolejny kluczowy element układanki, którego pominięcie jest proszeniem się o katastrofę: bariera paroizolacyjna. To ta pozornie prosta folia PE stanowi pierwszą, newralgiczną linię obrony paneli laminowanych przed wilgocią, która może migrować z podłoża.
Dlaczego wilgoć z podłoża jest zagrożeniem, skoro płytki są nienasiąkliwe? Tutaj dochodzimy do sedna. Po pierwsze, fugi. Choć ciasne, nie są one całkowicie paroszczelne, zwłaszcza w przypadku starych lub uszkodzonych fug. Po drugie, i co ważniejsze, potencjalna wilgoć pochodząca z głębszych warstw podłogi betonowej (w której posadzono płytki). Nawet jeśli beton jest pozornie suchy na powierzchni, może zawierać resztkową wilgoć technologiczną lub być narażony na podciąganie kapilarne (zwłaszcza na parterze bez odpowiedniej izolacji poziomej). Panele laminowane, jak już wiemy, składają się w dużej mierze z HDF – materiału, który chłonie wilgoć jak gąbka.
Folia paroizolacyjna (zwykle oznaczana jako folia PE, od polietylenu) działa jak nieprzepuszczalna membrana, która fizycznie odseparowuje panele od podłoża z płytek i blokuje przenikanie pary wodnej w górę. Powszechnie stosowana folia powinna mieć grubość minimum 0.2 mm (200 mikronów). Folie cieńsze, np. 0.1 mm, mogą być niewystarczające i podatne na uszkodzenia podczas montażu.
Sposób układania folii paroizolacyjnej jest równie ważny, co jej obecność. Folię układa się luźno na całej powierzchni podłogi, paskami, które zachodzą na siebie na szerokość co najmniej 20-40 centymetrów. Te zakłady to krytyczne miejsca – muszą być szczelnie sklejone specjalną taśmą do łączenia folii paroizolacyjnych, zazwyczaj o zwiększonej odporności na wilgoć i parę. Sklejenie zakładów zapobiega przedostawaniu się wilgoci przez te łączenia.
Folię należy również wywinąć na ściany na wysokość około 5-10 centymetrów. Ten naddatek zapewnia, że bariera jest ciągła również przy krawędziach pomieszczenia. Po zakończeniu montażu paneli i listew przypodłogowych, nadmiar folii wystający ponad podłogę należy ostrożnie odciąć ostrym nożykiem.
Pamiętaj, aby folii nie naciągać. Ma leżeć swobodnie. Nadmierne naciągnięcie może spowodować jej pęknięcie przy niewielkim ruchu podłoża lub panelu. Chodzi o stworzenie bariery, nie napiętego namiotu. Każde przypadkowe przebicie folii podczas montażu (np. upuszczonym narzędziem) powinno być natychmiast załatane kawałkiem folii i zaklejone taśmą.
Współczesny rynek oferuje również podkłady pod panele zintegrowane z barierą paroizolacyjną. To wygodne rozwiązanie "2w1", które skraca czas pracy – nie musisz układać dwóch osobnych warstw. Takie podkłady zazwyczaj posiadają od spodu folię PE i taśmę samoprzylepną do łączenia pasów. Choć wygodne, zawsze sprawdź parametry takiej zintegrowanej warstwy paroizolacyjnej – czy ma odpowiednią grubość i czy jej paroszczelność jest na odpowiednim poziomie (powinna być nie mniejsza niż standardowej folii PE 0.2 mm). Wybierając takie rozwiązanie, upewnij się, że podkład ma również dobre parametry akustyczne i wytrzymałościowe, które są kluczowe przy układaniu na płytkach.
Zastosowanie bariery paroizolacyjnej jest bezwzględnie wymagane, gdy kładziemy podłogę laminowaną na płytkach, zwłaszcza w pomieszczeniach na parterze, w starym budownictwie, w piwnicach adaptowanych na cele mieszkalne lub w budynkach bez odpowiedniej izolacji przeciwwilgociowej pod płytkami. Nawet jeśli masz pewność co do braku wilgoci w starych płytkach, zastosowanie folii PE jest tanią polisą ubezpieczeniową od problemów w przyszłości. Jej koszt w przeliczeniu na metr kwadratowy (około 2-5 zł/m²) jest minimalny w porównaniu do kosztów naprawy paneli uszkodzonych przez wilgoć. To jak z pasem bezpieczeństwa – masz nadzieję, że nie będzie potrzebny, ale gdy nadejdzie krytyczna sytuacja, okaże się nieoceniony.
Podsumowując, bariera paroizolacyjna na płytkach w formie folii PE to absolutnie niezbędny etap montażu paneli laminowanych. Chroni Twoją inwestycję przed "cichym wrogiem" – wilgocią. Układaj ją starannie, szczelnie klejąc zakłady i wywijając na ściany, a zapewnisz panelom suchy start i długie życie na nowym podłożu.
Podkład Akustyczny: Eliminacja Hałasu
Zastanawialiście się kiedyś, dlaczego podłogi z paneli laminowanych bywają postrzegane jako głośne? To kwestia fizyki i konstrukcji podłogi pływającej. Panele, niezwiązane trwale z podłożem, wibrują pod wpływem chodu czy spadających przedmiotów, a twarde podłoże (takie jak płytki czy beton) doskonale przenosi te drgania w dół, generując tak zwany "dźwięk uderzeniowy". Jest to szczególnie uciążliwe dla sąsiadów mieszkających pod nami, ale też potrafi drażnić w samym pomieszczeniu, tworząc efekt echa lub "pustego" dźwięku.
Tutaj z pomocą przychodzi podkład akustyczny, układany bezpośrednio na barierze paroizolacyjnej (lub będący integralną częścią zintegrowanego podkładu). Jego głównym zadaniem, gdy kładziemy panele laminowane na płytki, jest tłumienie tego właśnie dźwięku uderzeniowego. Działa trochę jak amortyzator i bariera dźwiękowa w jednym. Dobry podkład potrafi zredukować odczuwalny hałas nawet o kilkanaście, a nawet ponad dwadzieścia decybeli (co jest ogromną różnicą, bo skala decybelowa jest logarytmiczna!).
Wybór odpowiedniego podkładu jest kluczowy, zwłaszcza w przypadku podłoża z płytek. Podkład musi spełniać kilka funkcji jednocześnie: tłumić dźwięk, izolować termicznie (jeśli nie ma ogrzewania podłogowego, a podłoże jest zimne), a przede wszystkim – charakteryzować się odpowiednio wysoką wytrzymałością na ściskanie (parametr CS - Compressive Strength). Dlaczego wytrzymałość na ściskanie jest tak ważna, gdy układamy panele na płytkach ceramicznych? Grout lines, czyli fugi. Płytki nie tworzą idealnie płaskiej powierzchni – między nimi są niewielkie zagłębienia. Podkład o niskiej wytrzymałości na ściskanie może z czasem "wcisnąć" się w te zagłębienia pod ciężarem mebli czy intensywnego ruchu, co może doprowadzić do ugięcia paneli nad fugami, pękania zamków i w efekcie uszkodzenia podłogi. Zalecana wytrzymałość na ściskanie podkładów stosowanych na płytkach to minimum 60 kPa, a optymalnie 90 kPa lub więcej, zwłaszcza jeśli fugi są szerokie.
Na rynku dostępnych jest wiele rodzajów podkładów:
- Pianka PE (polietylenowa): Najtańsza opcja, ale zazwyczaj o niskiej gęstości i słabej wytrzymałości na ściskanie (często poniżej 20 kPa). Raczej niezalecana do układania na płytkach, chyba że są idealnie równe i mają bardzo wąskie fugi. Niska izolacyjność akustyczna w porównaniu do innych typów.
- Pianka XPS (polistyren ekstrudowany): Lepsza od pianki PE, dostępna w różnych gęstościach, o lepszych parametrach CS (od 40 do 120 kPa, a nawet więcej) i izolacyjności termicznej. Stosowana na płytkach, wybierajmy warianty o wyższym parametrze CS, np. min 60 kPa.
- Podkłady kwarcowe (minerałowo-polimerowe): Nowoczesne podkłady w postaci maty nasypanej drobnymi granulkami spiętymi lepiszczem. Charakteryzują się bardzo wysoką wytrzymałością na ściskanie (nawet powyżej 200 kPa), doskonale niwelują drobne nierówności podłoża (do 1-2 mm) i dobrze tłumią dźwięk uderzeniowy (choć nie zawsze są najlepsze w tłumieniu hałasu w pomieszczeniu). Doskonały wybór na płytki.
- Podkłady naturalne (korek, filc drzewny): Ekologiczne, ale mogą być droższe. Korek (granulowany lub w arkuszach) ma dobrą izolacyjność akustyczną i termiczną, ale jego odporność na ściskanie bywa niższa niż XPS czy podkładów kwarcowych (choć są wyjątki o wyższych parametrach). Wymagają idealnie równego podłoża z płytek.
- Podkłady gumowe lub gumowo-korkowe: Bardzo dobre właściwości akustyczne i często wysoka wytrzymałość na ściskanie. Doskonałe, choć należą do droższych opcji.
Parametr tłumienia dźwięku uderzeniowego podawany jest jako ΔLw w decybelach [dB]. Im wyższa wartość, tym lepsze tłumienie. Dobry podkład powinien oferować redukcję na poziomie minimum 16-18 dB, a w budynkach wielorodzinnych czy dla własnego komfortu – powyżej 20 dB.
Grubość podkładu również ma znaczenie, zarówno dla izolacyjności (im grubszy, tym zazwyczaj lepiej, ale do pewnego stopnia), jak i dla niwelowania nierówności (niektóre podkłady mogą niwelować drobne defekty podłoża, np. do 1-2 mm). Jednak główną funkcją wyrównującą powinno być odpowiednie przygotowanie samego podłoża z płytek masą samopoziomującą, a nie "mostkowanie" dużych nierówności samym podkładem, co może prowadzić do jego uszkodzenia pod obciążeniem.
Układając podkład, pamiętajmy o kilku zasadach. Układaj go pasami, "na styk" – krawędzie poszczególnych pasów powinny do siebie przylegać bez szczelin, ale też bez nachodzenia na siebie (co mogłoby stworzyć nierówność). Jeśli podkład nie ma zintegrowanej folii paroizolacyjnej, zawsze kładzie się go NA folii PE. Pasma podkładu można połączyć taśmą klejącą, aby się nie przesuwały podczas układania paneli. Unikaj zakładów, chyba że instrukcja producenta podkładu wyraźnie na to wskazuje dla konkretnego typu produktu.
Ignorowanie lub wybór zbyt cienkiego/słabego podkładu przy montażu laminatu na płytkach to jeden z najczęstszych błędów. Skutkuje nieprzyjemnym odgłosem kroków (tupot jak na bębenku) i potencjalnymi uszkodzeniami mechanicznymi paneli nad fugami w przyszłości. Zawsze wybieraj podkład o parametrach CS dopasowanych do rzeczywistego stanu podłoża z płytek i o jak najwyższym parametrze ΔLw, na jaki pozwala budżet. To inwestycja w komfort akustyczny i trwałość podłogi.
Dobry podkład akustyczny jest nie tylko dowodem naszej troski o uszy sąsiadów, ale też znacząco poprawia odczucie komfortu w naszym własnym mieszkaniu. Podłoga staje się cichsza, kroki są przyjemniej stłumione, a nawet drobne przedmioty upadające na podłogę wydają mniej ostry dźwięk. Zastosowanie podkładu akustycznego na płytki ceramiczne to kluczowy element zapewniający trwałość i komfort użytkowania Twojej nowej podłogi z paneli.
Finalny Etap: Montaż Paneli Metodą Click i Dylatacja
Dochodzimy do momentu, na który wszyscy czekaliśmy – samego układania paneli! Po starannej aklimatyzacji, przygotowaniu podłoża z płytek, ułożeniu bariery paroizolacyjnej i odpowiedniego podkładu akustycznego, jesteśmy gotowi, by dać "klik" i zobaczyć, jak nowa podłoga nabiera kształtów. Współczesne panele laminowane wykorzystują systemy zamków zatrzaskowych, potocznie zwane systemem "click". Dzięki niemu panele są łączone na zasadzie pióro-wpustu, zatrzaskując się bez użycia kleju.
System "click" umożliwia montaż paneli jako tzw. podłogi pływającej. Oznacza to, że podłoga nie jest w żaden sposób trwale związana z podłożem – ani klejona, ani przybijana, ani przykręcana do płytek. Cała powierzchnia paneli spoczywa luźno na podkładzie. Ta niezależność od podłoża jest absolutnie kluczowa i musisz to zrozumieć: laminat na click jest układany na płytkach podłogowych! Jakiekolwiek próby przyklejenia lub unieruchomienia paneli spowodują uszkodzenie podłogi laminowanej. Panele muszą mieć możliwość minimalnego "ruchu" w odpowiedzi na zmiany temperatury i wilgotności.
Pierwszym krokiem w montażu jest decyzja o kierunku układania. Najczęściej panele układa się równolegle do kierunku padania światła z głównego okna. Taki układ optycznie ukrywa łączenia między deskami. Alternatywnie, w długich i wąskich pomieszczeniach, można układać je wzdłuż dłuższego wymiaru pokoju, co optycznie go wydłuża. Niezależnie od kierunku, zazwyczaj zaczynamy od ściany z najmniejszą liczbą przeszkód lub najdłuższej prostej ściany.
Zanim położysz pierwszy panel, musisz zapewnić niezbędną szczelinę dylatacyjną (zwaną też przerwą dylatacyjną lub fugą dylatacyjną) wokół całego obwodu pomieszczenia. Ta szczelina to pusta przestrzeń pozostawiona celowo między krawędzią ułożonej podłogi a ścianami, futrynami drzwi, rurami grzewczymi, kolumnami czy wszelkimi innymi elementami trwale związanymi z konstrukcją budynku lub inną wykładziną podłogową. Szerokość tej szczeliny zazwyczaj wynosi od 10 do 15 milimetrów (czyli 1 do 1,5 cm). Jak to uzyskać? Używamy specjalnych klinów dylatacyjnych lub po prostu kawałków paneli/listew dociętych na odpowiednią szerokość i wkładamy je między panel a ścianę podczas montażu pierwszej i kolejnych rzędów. Usuniemy je dopiero po zakończeniu układania całej podłogi.
Dlaczego dylatacja jest tak ważna przy układaniu laminatu na płytkach (i w ogóle)? Jak wspomnieliśmy, panele "pracują" – rozszerzają się i kurczą pod wpływem wahań temperatury i wilgotności. W szczególności wilgoć może spowodować ich znaczące zwiększenie objętości. Jeśli podłoga ułożona jest "na sztywno", bez miejsca na ten ruch, naprężenia będą rosły aż do momentu, gdy podłoga zacznie się wybrzuszać (podnosić do góry), zwłaszcza na środku pomieszczenia, lub dojdzie do pęknięć paneli czy zniszczenia zamków. Szerokość 1-1.5 cm jest zazwyczaj wystarczająca dla standardowych pomieszczeń (do około 10x10 metrów) i paneli o typowej grubości.
Pierwszy rząd paneli kładziemy piórem w stronę ściany, pamiętając o klinach dylatacyjnych. Odcinamy pióro na pierwszym panelu tylko wtedy, gdy producent tak zaleca. Kolejne panele w pierwszym rzędzie łączymy krótszymi bokami za pomocą systemu "click". W kolejnych rzędach najpierw łączymy dłuższe boki paneli z rzędem już ułożonym, a następnie delikatnie dobijamy (używając klocka do dobijania i młotka gumowego) krótkie boki, aby zamki zatrzasnęły się na całej długości.
Przy docinaniu paneli do ścian, futryn czy rur, pamiętajmy, że nacięcie musi uwzględniać szczelinę dylatacyjną. Na przykład, jeśli docinasz panel wokół rury grzewczej, otwór w panelu powinien być o około 2-3 cm większy w średnicy niż rura, aby panel miał "luz" na ruch wokół rury. Podobnie przy ościeżnicach drzwiowych – często najlepszym rozwiązaniem jest podcięcie dołu ościeżnicy, aby panel mógł swobodnie wsunąć się pod nią, zapewniając ciągłość dylatacji.
Koniecznie używaj odpowiednich narzędzi: dobrej piły (tarczowej lub wyrzynarki z odpowiednim brzeszczotem do laminatu – tnąc wyrzynarką od spodu unikniesz odprysków na stronie wierzchniej), kątownika, miarki, ołówka, klocka do dobijania, metalowego dobijaka (do dobijania paneli przy ścianach, gdzie nie mieści się klocek), i wspomnianych klinów dystansowych.
Po ułożeniu całej powierzchni, usuwamy kliny dylatacyjne. Powstałą szczelinę dylatacyjną przykrywamy listwami przypodłogowymi. Listwy przypodłogowe (montowane do ściany!) maskują szczelinę, jednocześnie pozwalając podłodze "pracować" pod spodem. Przy przejściach do innych pomieszczeń lub innych typów podłóg stosuje się specjalne profile progowe (przejściowe), które maskują szczelinę i zapewniają estetyczne połączenie, jednocześnie zachowując dylatację między różnymi strefami podłogi.
Podsumowując montaż paneli laminowanych na płytkach to etap, który wymaga precyzji i cierpliwości, ale przy zastosowaniu systemu click i zachowaniu prawidłowej dylatacji, jest w zasięgu większości osób z zacięciem majsterkowicza. Pamiętaj o kluczowej zasadzie: podłoga pływająca nie może być unieruchomiona. Poprawne wykonanie tego etapu, po solidnych przygotowaniach, zwieńczy Twoją pracę trwałą, równą i estetyczną podłogą z paneli.