Czy można kłaść panele podłogowe bezpośrednio na styrodur?
Stajemy często przed remontową zagadką: jak osiągnąć podłogę marzeń, która nie tylko wygląda świetnie, ale też realnie grzeje, a nie chłodzi nasze stopy? Wśród materiałów izolacyjnych pojawia się wielu kandydatów, ale jeden zyskuje na popularności w kontekście izolacji pod panelami – styrodur. Pojawia się zatem palące pytanie, które nurtuje wielu: Czy można kłaść panele bezpośrednio na styrodur? Otóż, eksperci są zgodni – bezpośrednie układanie paneli laminowanych czy winylowych prosto na płycie XPS bez warstw pośrednich to ryzykowna gra, której lepiej unikać.
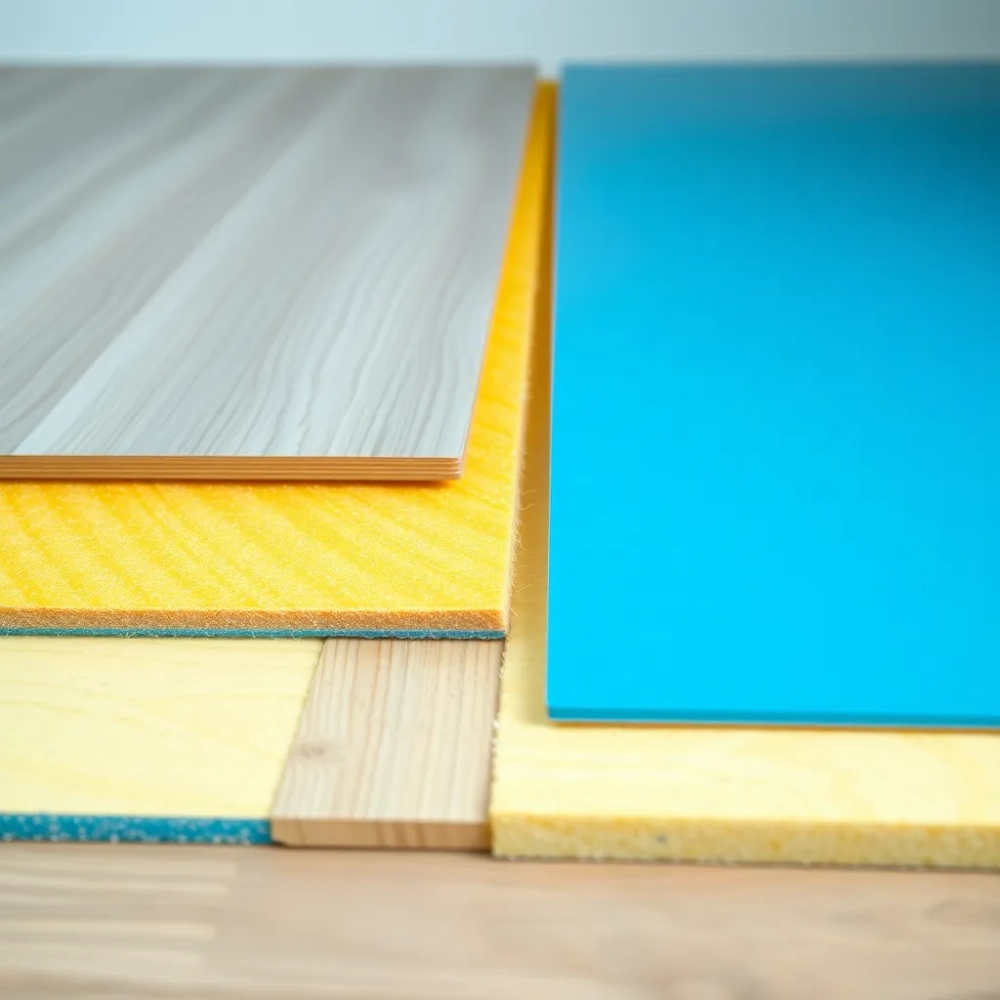
Patrząc na materiał od kuchni, warto zerknąć na jego suche parametry, które odróżniają go od tradycyjnych rozwiązań i czynią faworytem do stosowania w trudniejszych warunkach. Polistyren ekstrudowany, potocznie zwany styrodurem lub XPS, to techniczny materiał, który wyróżnia się na tle spienionego polistyrenu (EPS). Analiza kluczowych właściwości wskazuje, dlaczego budowlańcy go cenią pod podłogi, choć nadal pojawiają się pułapki, na które trzeba uważać podczas instalacji.
Jego struktura jest inna – zamkniętokomórkowa, jednorodna, co przekłada się bezpośrednio na wydajność izolacyjną i mechaniczną. Spójrzmy na dane, które definiują płytę XPS i sprawiają, że jest to materiał wart rozważenia pod podłogi panelowe, o ile zostanie użyty w prawidłowym systemie warstw.
Właściwość kluczowa dla podłóg | Typowa Wartość dla XPS (przykłady) | Znaczenie dla podłogi panelowej |
---|---|---|
Współczynnik przewodzenia ciepła (Lambda, λ) | 0.028 - 0.034 W/mK | Lepsza izolacyjność termiczna na jednostkę grubości; kluczowe dla komfortu cieplnego i przy ogrzewaniu podłogowym. |
Wytrzymałość na ściskanie (CS przy 10% odkształceniu) | ≥ 250 kPa (często dostępne 300, 400, 500 kPa) | Odporność na obciążenia statyczne i dynamiczne; minimalizuje ryzyko trwałego odkształcenia izolacji pod meblami i ruchem. |
Nasiąkliwość wodą (długotrwałe zanurzenie) | ≤ 1.5% (często poniżej 1.0%) | Ekstremalna odporność na wilgoć, idealne rozwiązanie na posadzki na gruncie, w piwnicach, czy w pomieszczeniach narażonych na podwyższoną wilgotność z podłoża. |
Struktura materiału | Zamkniętokomórkowa, jednorodna | Zapewnia stabilność wymiarową, twardość powierzchni i odporność na wchłanianie wody; ułatwia cięcie bez kruszenia koralików. |
Te twarde liczby mówią nam jasno – mamy do czynienia z materiałem o solidnej konstrukcji i niskiej wrażliwości na wodę, co w przypadku podłóg na gruncie lub w wilgotnych pomieszczeniach jest zbawienne dla samej izolacji. Jest to podstawa o doskonałych parametrach izolacyjnych i wytrzymałościowych. Lecz nawet takie supercechy nie zwalniają nas z myślenia o kompletnym systemie warstw, który musi zostać położony powyżej XPS, aby podłoga panelowa działała prawidłowo przez lata.
Aby uzmysłowić sobie skalę inwestycji w poszczególne warstwy oraz ich wzajemne relacje, spójrzmy na orientacyjny rozkład kosztów materiałów w typowym, poprawnym systemie podłogi panelowej na izolacji XPS. Prezentowany wykres przedstawia przykładowe procentowe udziały kosztów dla 50 m² powierzchni podłogi, uwzględniając niezbędne warstwy: izolację XPS, folię paroizolacyjną oraz specjalistyczny podkład pod panele.
Powyższy diagram pokazuje, że sama izolacja XPS to tylko część inwestycji w kompleksowy system podłogowy. Folia paroizolacyjna, choć tania, jest krytycznie ważnym elementem układanki, a podkład pod panele, stanowiąc znaczący procent kosztów materiałowych, odpowiada za kluczowe parametry użytkowe podłogi. Zaplanowanie wszystkich warstw z góry pozwala uniknąć kosztownych błędów i cieszyć się trwałą, komfortową podłogą, która jest zarówno ciepła, jak i cicha.
Dlaczego nie zaleca się bezpośredniego układania paneli na styrodurze?
Pomysł, by położyć panele prosto na płycie XPS, może wydawać się kuszący ze względu na pozorne uproszczenie prac i redukcję kosztów materiałowych. W końcu styrodur to materiał twardy, stabilny i zapewniający dobrą izolację termiczną, prawda? Ah, gdyby tylko świat budownictwa był tak prosty i pozbawiony niuansów technicznych! Rzeczywistość jest jednak znacznie bardziej skomplikowana i kryje pułapki dla osób pomijających kluczowe warstwy.
Jednym z fundamentalnych problemów jest kwestia idealnej gładkości i równego podparcia na całej powierzchni. Chociaż płyty XPS są produkowane z dużą precyzją, ich krawędzie – nawet frezowane – rzadko kiedy zapewniają perfekcyjną płaskość i licowanie wymaganą przez systemy zamków nowoczesnych paneli podłogowych, czy to laminowanych, czy winylowych typu Click. Drobne różnice wysokości na łączeniach płyt XPS, wynoszące nawet poniżej milimetra, stanowią realne zagrożenie dla trwałości podłogi w perspektywie czasu.
Wyobraźmy sobie panele podłogowe jako delikatne konstrukcje z precyzyjnie frezowanymi "językami" i "wpustami". System Click działa dzięki idealnemu dopasowaniu i równomiernemu podparciu. Gdy pod panelami znajdują się mikroskopijne schodki na stykach płyt XPS, każdorazowe przejście, przesunięcie mebla czy upadek przedmiotu powoduje koncentrację naprężeń dokładnie w tym miejscu, gdzie panel nie ma pełnego podparcia. To jak ciągłe uderzanie miniaturowym młotkiem w najwrażliwszy punkt połączenia.
Taka sytuacja prędzej czy później prowadzi do uszkodzenia mechanicznego zamków. Mogą się one po prostu wyłamać, popękać lub trwale odkształcić. Konsekwencją są nieestetyczne szczeliny pojawiające się między panelami, skrzypienie podłogi przy każdym kroku (co potrafi być niezwykle irytujące!), a w skrajnych przypadkach nawet wybrzuszenie paneli w miejscach uszkodzeń lub konieczność wymiany pojedynczych desek, co w systemach pływających często wymaga demontażu dużej części podłogi.
Kolejnym poważnym problemem jest brak rozproszenia obciążeń punktowych. Owszem, XPS ma rewelacyjną wytrzymałość na ściskanie ogólne – te > 250 kPa to świetny wynik! Ale to jest wytrzymałość na równomiernie rozłożony ciężar na dużej powierzchni. Panele podłogowe są obciążane punktowo przez nogi mebli (zwłaszcza krzeseł, stołów, ciężkich szaf), a nawet przez twarde obuwie jak szpilki. Taka siła, skupiona na kilku centymetrach kwadratowych, generuje olbrzymie ciśnienie jednostkowe, znacznie przekraczające zdolność panela do równomiernego rozłożenia go na zbyt miękkim (w tym konkretnym kontekście obciążeń punktowych) podłożu XPS.
Bez specjalistycznego podkładu pod panele, który ma za zadanie "przyjąć" na siebie te punktowe naciski i rozłożyć je na większą powierzchnię izolacji XPS, dojdzie do trwałego wgniecenia samego styroduru dokładnie pod nogami mebli czy w często używanych ścieżkach ruchu. Te wgłębienia będą widoczne na powierzchni paneli jako nieestetyczne odciski, niszcząc efekt wizualny podłogi i świadcząc o błędzie w sztuce budowlanej. Przypomina to próbę postawienia ciężkiego przedmiotu o ostrych krawędziach bezpośrednio na bloku plasteliny – efekt jest przewidywalny.
Aspekt akustyczny również przemawia przeciwko bezpośredniemu układaniu paneli na styrodurze. O ile XPS jest dobrym izolatorem termicznym, o tyle jego sztywna struktura słabo tłumi dźwięki uderzeniowe, czyli odgłos kroków czy spadających przedmiotów. Panele ułożone bezpośrednio na twardym XPS działają jak membrana rezonansowa. Każdy krok zamienia się w głośne "tup-tup" przenoszone przez sztywną konstrukcję do niższej kondygnacji. Komfort akustyczny podłóg wymaga warstwy elastycznej, która zaabsorbuje energię dźwięku.
Brak dedykowanego podkładu eliminuje warstwę, która kompensuje niewielkie ruchy paneli wynikające ze zmian temperatury i wilgotności. Panele laminowane i winylowe "pracują", nie stoją w miejscu. Potrzebują minimalnej przestrzeni do ruchu oraz warstwy, która stabilizuje ich pozycję i jednocześnie amortyzuje te mikroruchy. Bez podkładu, zwiększa się ryzyko naprężeń na zamkach, co może prowadzić do ich pękania lub rozchodzenia się paneli, zwłaszcza na dużych powierzchniach.
Wreszcie, pominięcie wymaganych warstw, w tym podkładu między folią a panelami, często równoznaczne jest z utratą gwarancji producenta paneli podłogowych. Większość renomowanych firm produkujących panele precyzyjnie określa w instrukcjach montażowych, jakie warstwy muszą znaleźć się pod panelami, w tym grubość i parametry podkładu. Brak spełnienia tych wymogów stanowi formalną podstawę do odrzucenia ewentualnej reklamacji dotyczącej trwałości zamków czy uszkodzeń mechanicznych powierzchni związanych z niewłaściwym podparciem.
Reasumując (bez robienia formalnego podsumowania rozdziału!): chociaż XPS to świetny materiał bazowy izolacyjny pod podłogę, kładzenie paneli podłogowych bezpośrednio na nim jest błędem wynikającym z niezrozumienia roli pozostałych warstw systemu. Oszczędność wynikająca z pominięcia podkładu jest iluzoryczna i niemal gwarantuje przyszłe problemy, koszty napraw i rozczarowanie estetyką oraz funkcjonalnością podłogi. Inwestując w dobrą izolację, nie warto psuć całości na ostatnim etapie.
Jakie warstwy są niezbędne pomiędzy styrodurem a panelami podłogowymi?
Skoro ustaliliśmy, że kładzenie paneli bezpośrednio na styrodurze to zły pomysł, czas na konkretne rozwiązania. Układanie podłogi panelowej na izolacji termicznej XPS to system wielowarstwowy, w którym każda warstwa pełni ściśle określoną funkcję. Pominięcie którejkolwiek z nich jest jak budowanie domu bez solidnego dachu – cała konstrukcja traci sens i odporność na czynniki zewnętrzne.
Podstawą jest oczywiście odpowiednio przygotowane podłoże – najczęściej jastrych cementowy lub anhydrytowy, który powinien być suchy, stabilny i w miarę równy. Na tym podłożu układamy płyty izolacyjne ze styroduru XPS. Ich grubość zależy od wymaganej izolacyjności termicznej, najczęściej od 5 do nawet 20 cm lub więcej, układane w jednej lub dwóch warstwach na mijankę, aby zminimalizować mostki termiczne na stykach płyt.
Pierwszą niezbędną warstwą układaną *na* styrodurze jest folia paroizolacyjna. I tu nie ma kompromisów, chyba że mówimy o bardzo specyficznych systemach, gdzie wilgoć jest całkowicie wyeliminowana, co w przypadku posadzek jest rzadkością. Folia ta ma za zadanie chronić zarówno izolację XPS, jak i same panele przed migracją wilgoci z podłoża, czyli z jastrychu pod XPS-em. Nawet suche na oko wylewki mogą oddawać pewną ilość pary wodnej przez długi czas.
Standardem rynkowym, który zapewnia odpowiednie zabezpieczenie, jest stosowanie folii polietylenowej (PE) o minimalnej grubości 0.2 mm, czyli 200 mikronów. Specjaliści często rekomendują grubszą folię, np. 0.3 mm (300 mikronów), dla większego spokoju i pewności. Kluczowe jest prawidłowe ułożenie tej folii: arkusze powinny zachodzić na siebie z zakładem minimum 20 cm, a wszystkie łączenia muszą być starannie sklejone dedykowaną taśmą klejącą. Co więcej, folia musi być wywinięta na ściany na wysokość kilku centymetrów (około 5-10 cm), tworząc szczelną "wannę" ochronną. Ten nadmiar folii przycina się dopiero po zainstalowaniu paneli i listew przypodłogowych.
Następna krytycznie ważna warstwa to podkład pod panele podłogowe. To on jest bezpośrednim sąsiadem paneli i pełni wiele kluczowych funkcji, których sam styrodur nie zapewnia. Podkład ma za zadanie wyrównać drobne nierówności, które mogą pozostać na powierzchni płyt XPS lub na ich łączeniach. Chodzi tu o nierówności rzędu do 2-3 mm, w zależności od wymagań producenta paneli.
Jedną z najważniejszych funkcji podkładu jest zapewnienie izolacji akustycznej od dźwięków uderzeniowych. Specjalistyczne podkłady redukują głośność kroków (mierzona jako ΔLw) nawet o 20 dB i więcej. Rodzaj materiału ma tu kolosalne znaczenie. Popularne i ekonomiczne pianki PE zapewniają podstawową akustykę (np. ΔLw ok. 16-18 dB). Lepsze parametry akustyczne i większą odporność na ściskanie mają podkłady z włókna drzewnego, tekturowe (często w postaci płyt), czy specjalistyczne podkłady poliuretanowo-mineralne (PUM), które potrafią osiągnąć ΔLw > 20 dB i najwyższą odporność na ściskanie (CS > 400 kPa).
Podkład działa również jako warstwa rozpraszająca obciążenia. Jak wspomniano wcześniej, punktowe naciski od mebli czy kroków muszą być skutecznie rozprowadzone na większej powierzchni, zanim dotrą do izolacji XPS. Wytrzymałość podkładu na ściskanie (CS) jest tutaj kluczowym parametrem – im wyższy, tym lepiej chronione są zamki paneli przed uszkodzeniem i izolacja pod spodem przed trwałymi wgnieceniami. Dobre podkłady XPS pod panele czy PUM mają CS na poziomie porównywalnym lub wyższym niż sama płyta XPS, co stanowi dodatkową zaporę.
Typowe grubości podkładów pod panele wynoszą od 2 mm do 6 mm, w zależności od materiału i przeznaczenia (np. podłogi z ogrzewaniem podłogowym wymagają podkładów o niskim oporze cieplnym R, co zazwyczaj wiąże się z mniejszą grubością, ale wysokim CS). Ważne jest, aby podkład był dopasowany do rodzaju paneli (laminowane vs. winylowe, które mają inne wymagania co do twardości podkładu) i specyfiki pomieszczenia.
Sumując, system warstw wygląda następująco (od dołu do góry): 1. Przygotowane podłoże, 2. Izolacja termiczna ze styroduru XPS, 3. Folia paroizolacyjna (szczelnie ułożona), 4. Podkład pod panele (o odpowiednich parametrach: wyrównanie, akustyka, rozpraszanie obciążeń, opór cieplny), 5. Panele podłogowe. Pominięcie folii paroizolacyjnej lub podkładu pod panele to błąd, który poważnie zagraża trwałości paneli i komfortowi użytkowania podłogi.
Niewłaściwy wybór lub brak którejkolwiek z tych warstw na styrodurze oznacza brak spełnienia kluczowych wymogów technicznych, co prowadzi do problemów, których naprawa bywa skomplikowana i kosztowna. Pamiętajmy: prawidłowy system warstw to inwestycja w spokój ducha i długowieczność naszej podłogi.
Właściwości styroduru XPS kluczowe dla podłóg pod panelami
Styrodur, czyli polistyren ekstrudowany (XPS), to nie jest po prostu kolorowy styropian. Jego proces produkcji – ekstruzja – nadaje mu zupełnie odmienne właściwości, które czynią go materiałem wyjątkowo dobrze przystosowanym do trudnych zadań izolacyjnych, w tym izolacji posadzek. Zrozumienie tych kluczowych cech pomaga pojąć, dlaczego XPS jest często preferowanym wyborem w kontekście izolacji podłóg pod panele, w przeciwieństwie do tradycyjnego styropianu EPS.
Najbardziej rzucającą się w oczy cechą techniczną jest jego imponująca wytrzymałość na ściskanie. Jak podają specyfikacje techniczne, typowe płyty XPS przeznaczone na podłogi posiadają współczynnik CS (Compressive Strength) wynoszący minimum > 250 kPa przy 10% odkształcenia. Oznacza to, że płyta może przyjąć obciążenie ponad 25 ton na metr kwadratowy, zanim odkształci się trwale o 10%. W praktyce rynkowej dostępne są produkty o znacznie wyższych parametrach, np. 300 kPa, 400 kPa, a nawet 500 kPa. Co więcej, XPS wykazuje bardzo małe odkształcenie pod długotrwałym obciążeniem stałym, co jest krytycznie ważne na posadzkach.
Dlaczego ta wytrzymałość jest tak ważna w kontekście podłóg pod panelami? Panele podłogowe, chociaż same w sobie sztywne, opierają się na podłożu. Cały ciężar wyposażenia pomieszczenia (mebli, sprzętów AGD/RTV) oraz obciążenia użytkowe (ciężar ludzi chodzących, dynamiczne obciążenia) są przenoszone przez panele na warstwy izolacyjne pod nimi. Jeśli izolacja jest zbyt miękka, jak ma to miejsce w przypadku tradycyjnego styropianu fasadowego czy o niskiej gęstości, będzie się ona trwale odkształcać pod długotrwałym ciężarem. To z kolei prowadzi do zapadania się podłogi w niektórych miejscach, co rujnuje efekt estetyczny i co gorsza – prowadzi do pękania zamków paneli oraz skrzypienia.
XPS, dzięki wysokiemu CS, stanowi stabilne i twarde podparcie dla systemu panelowego. Nie ugina się i nie zapada pod ciężarem mebli czy ruchem użytkowników (oczywiście przy założeniu zastosowania prawidłowego podkładu rozpraszającego obciążenia punktowe, o czym mówiliśmy wcześniej). Jest to szczególnie ważne w pomieszczeniach o dużym natężeniu ruchu lub z ciężkim wyposażeniem, jak np. kuchnie, jadalnie czy biura domowe.
Kolejną fundamentalną właściwością XPS, która czyni go niemal niezastąpionym materiałem do izolacji podłóg, jest jego ekstremalnie niska nasiąkliwość. Zgodnie z danymi, nasiąkliwość styroduru w warunkach długotrwałego zanurzenia wynosi zazwyczaj ≤ 1.5%, a często nawet poniżej 1.0%. Porównajmy to z nasiąkliwością tradycyjnego styropianu EPS, która może być wielokrotnie wyższa w podobnych warunkach. Ta cecha wynika z zamkniętokomórkowej struktury materiału, w której poszczególne komórki są od siebie oddzielone, uniemożliwiając swobodne przemieszczanie się wody wewnątrz materiału.
Niska nasiąkliwość jest kluczowa na posadzkach, zwłaszcza tych na gruncie, w piwnicach, na balkonach czy w pomieszczeniach narażonych na wilgoć. Woda wchłonięta przez materiał izolacyjny drastycznie obniża jego właściwości termiczne – mokry materiał przewodzi ciepło znacznie lepiej niż suchy. Co więcej, wilgoć w izolacji może prowadzić do rozwoju pleśni i grzybów, a także stopniowo niszczyć materiał izolacyjny od wewnątrz. XPS skutecznie zapobiega tym problemom, działając jak bariera przeciwko wilgoci w masie izolacyjnej, co zapewnia stałą i wysoką efektywność energetyczną podłogi przez dziesiątki lat.
Nie można zapomnieć o korzystnym współczynniku przewodzenia ciepła (Lambda, λ). Choć różnice między XPS a dobrym styropianem podłogowym EPS mogą wydawać się niewielkie, parametry 0.028 - 0.034 W/mK dla XPS są generalnie niższe (lepsze) niż dla większości EPS-ów podłogowych. Oznacza to, że ta sama izolacyjność termiczna może zostać osiągnięta przy zastosowaniu cieńszej warstwy materiału. To niezwykle cenne tam, gdzie wysokość podłogi jest ograniczona – np. w remontowanych budynkach czy przy budowie pasywnych domów, gdzie kładzie się duży nacisk na każdy element systemu. Cieplejsza podłoga to nie tylko niższe rachunki za ogrzewanie, ale przede wszystkim nieporównywalny komfort użytkowania, gdy nasze stopy stykają się z powierzchnią.
Wreszcie, jednorodna, zamkniętokomórkowa struktura XPS przekłada się na jego stabilność wymiarową i łatwość obróbki. Płyty są sztywne, gładkie, a podczas cięcia nie kruszą się tak jak styropian EPS, z którego sypią się wszędobylskie "koraliki". Ta gładkość i stabilność minimalizują (choć nie eliminują całkowicie!) drobne nierówności na powierzchni izolacji, ułatwiając późniejsze układanie folii i podkładu.
Podsumowując (ponownie, bez formalnego akapitu kończącego rozdział!), właściwości takie jak wysoka wytrzymałość na ściskanie, minimalna nasiąkliwość i korzystny współczynnik przewodzenia ciepła sprawiają, że styrodur XPS jest materiałem pierwszego wyboru do izolacji termicznej posadzek pod wszelkiego rodzaju wykończenia, w tym panele podłogowe. Te cechy gwarantują trwałość izolacji, jej odporność na warunki panujące w podłożu oraz realnie przekładają się na oszczędności energetyczne i komfort cieplny. Stanowi on solidną, wytrzymałą i ciepłą bazę dla systemu podłogowego.
Ryzyko i błędy związane z pominięciem podkładu na styrodurze
Pokusa oszczędności bywa potężna w procesie budowy lub remontu. Skoro położyliśmy już solidną, odporną na ściskanie i wilgoć izolację XPS, a nawet zabezpieczyliśmy się folią paroizolacyjną, to czy ten cienki podkład pomiędzy folią a panelami jest naprawdę konieczny? Przecież to kolejny wydatek i dodatkowa warstwa do ułożenia. Czy można go bezpiecznie pominąć, kładąc panele bezpośrednio na folii (a co za tym idzie, de facto na XPS)? Otóż, absolutnie nie. Pominięcie podkładu to klasyczny błąd, który bywa opłakany w skutkach, a pozorna oszczędność na kilku złotych za metr kwadratowy przekłada się na koszty idące w setki, a nawet tysiące złotych na późniejszą naprawę.
Głównym ryzykiem związanym z pominięciem podkładu jest przyspieszone i nieuniknione uszkodzenie systemu zamków paneli podłogowych. Tak, panele laminowane czy winylowe potrzebują podkładu! Jak już wspomnieliśmy, panele nie są sztywnymi deskami leżącymi płasko na podłożu. Działają w systemie pływającym, a ich wytrzymałość w dużej mierze opiera się na integralności precyzyjnie frezowanych zamków. Te zamki są jednak bardzo wrażliwe na dwa czynniki: nierównomierne podparcie i punktowe obciążenia. Podkład, nawet cienki (np. 2-3 mm), doskonale spełnia rolę bufora i warstwy wyrównującej.
Bez podkładu, wszelkie mikronierówności na łączeniach płyt XPS czy nawet pojedyncze ziarenka piasku czy resztki kleju pozostawione na folii, będą stanowić punkty koncentracji naprężeń pod panelami. Gdy postawimy krzesło, szafę, czy po prostu przejdziemy, cały ciężar w tym miejscu skupia się na niewielkiej powierzchni. Brak warstwy, która rozłoży to obciążenie, sprawia, że zamek panela jest miażdżony lub wyłamywany w tym właśnie punkcie. To cichy zabójca każdej podłogi panelowej. Znam przypadki, gdy panele "padły" już po kilku miesiącach intensywnego użytkowania tylko dlatego, że inwestor zlekceważył znaczenie podkładu. Frustracja gwarantowana.
Innym, niemniej uciążliwym ryzykiem jest problem akustyczny. Bez specjalistycznego podkładu, który pochłania energię dźwięków uderzeniowych, podłoga będzie niezwykle głośna. Każdy krok, przesuwanie krzesła, a nawet upadek długopisu, będzie generował irytujący hałas przenoszący się do pomieszczenia poniżej. Panele położone bezpośrednio na sztywnej folii i sztywnym XPS-ie będą po prostu rezonować. Jeśli zależy Wam na komforcie własnym i sąsiadów, podkład o dobrych parametrach ΔLw (redukcji dźwięków uderzeniowych) jest absolutnie niezbędny. Nikt chyba nie chce, żeby jego podłoga "mówiła" do sąsiadów przy każdej okazji.
Pominięcie podkładu to również zagrożenie dla samego XPS-u w perspektywie. Chociaż styrodur ma wysoką ogólną wytrzymałość, powtarzające się, nierozproszone obciążenia punktowe mogą z czasem prowadzić do lokalnych odkształceń izolacji, nawet tej tak wytrzymałej jak XPS. Te trwałe wgniecenia, spowodowane np. nogami od ciężkich mebli, będą szpeciły podłogę panelową i świadczyły o wadzie montażu. Podkład działa jak amortyzator, który chroni również bazową warstwę izolacyjną przed takimi uszkodzeniami.
Kwestia gwarancji – to argument, który powinien przemówić do najbardziej oszczędnych. Producenci paneli podłogowych, zarówno laminowanych, jak i winylowych (szczególnie tych na twardym rdzeniu SPC), w swoich instrukcjach montażu kładą duży nacisk na stosowanie odpowiedniego podkładu. Określają jego parametry – przede wszystkim minimalną odporność na ściskanie (CS), często też współczynnik redukcji dźwięków uderzeniowych (ΔLw) oraz opór cieplny (R) w przypadku ogrzewania podłogowego. Pominięcie podkładu lub zastosowanie podkładu o zbyt niskich parametrach (np. cienkiej pianki PE tam, gdzie wymagany jest podkład o wysokim CS) jest podstawą do odrzucenia reklamacji na uszkodzenia paneli, w tym pękające zamki.
Wyobraźmy sobie scenariusz: po dwóch latach panele zaczynają skrzypieć, pojawiają się szczeliny. Zgłaszacie reklamację. Pierwsze, co zrobi rzeczoznawca, to sprawdzi poprawność montażu i zastosowane materiały. Jeśli odkryje brak podkładu lub podkład niezgodny z wymogami producenta paneli – gwarancja przepada. Cała inwestycja w panele – które mogą kosztować od kilkudziesięciu do nawet kilkuset złotych za metr kwadratowy – idzie na marne, bo popełniliśmy błąd na podkładzie wartym kilkanaście czy kilkadziesiąt złotych za metr. Matematyka jest bezlitosna: to fatalna kalkulacja ekonomiczna.
Podsumowując (ale nie finalnie!), skutki pominięcia podkładu na styrodurze są liczne i kosztowne. Obejmują one uszkodzenia mechaniczne paneli i izolacji, drastyczne pogorszenie komfortu akustycznego oraz utratę gwarancji. Podkład nie jest opcją ani dodatkiem; jest kluczową, funkcjonalną warstwą systemu podłogi panelowej na izolacji XPS, której rola w ochronie zamków, rozpraszaniu obciążeń i wyciszeniu jest nie do przecenienia. Traktujmy go jako absolutnie niezbędny element prawidłowego montażu, a unikniemy wielu problemów i rozczarowań związanych z naszą nową podłogą.