Czy można położyć płytki na panele? Szczegółowy przewodnik (2025)
Gdy myślimy o remoncie podłogi, zazwyczaj wyobrażamy sobie zrywanie starych warstw aż do betonu. A co, gdyby można było pominąć ten kłopotliwy etap? Zagadnienie "Czy można położyć płytki na panele?" od lat budzi gorące dyskusje, często prowokując uniesione brwi i sceptyczne uśmiechy. Otóż, zaskakująca dla wielu prawda jest taka: można położyć płytki na panele, choć zadanie to jest porównywalne do wymagającej ekspedycji w nieznane – wymaga precyzyjnego planowania i przygotowania równie solidnego, jak budowanie bazy pod wierzchołkiem, aby nowa nawierzchnia była trwała i stabilna.
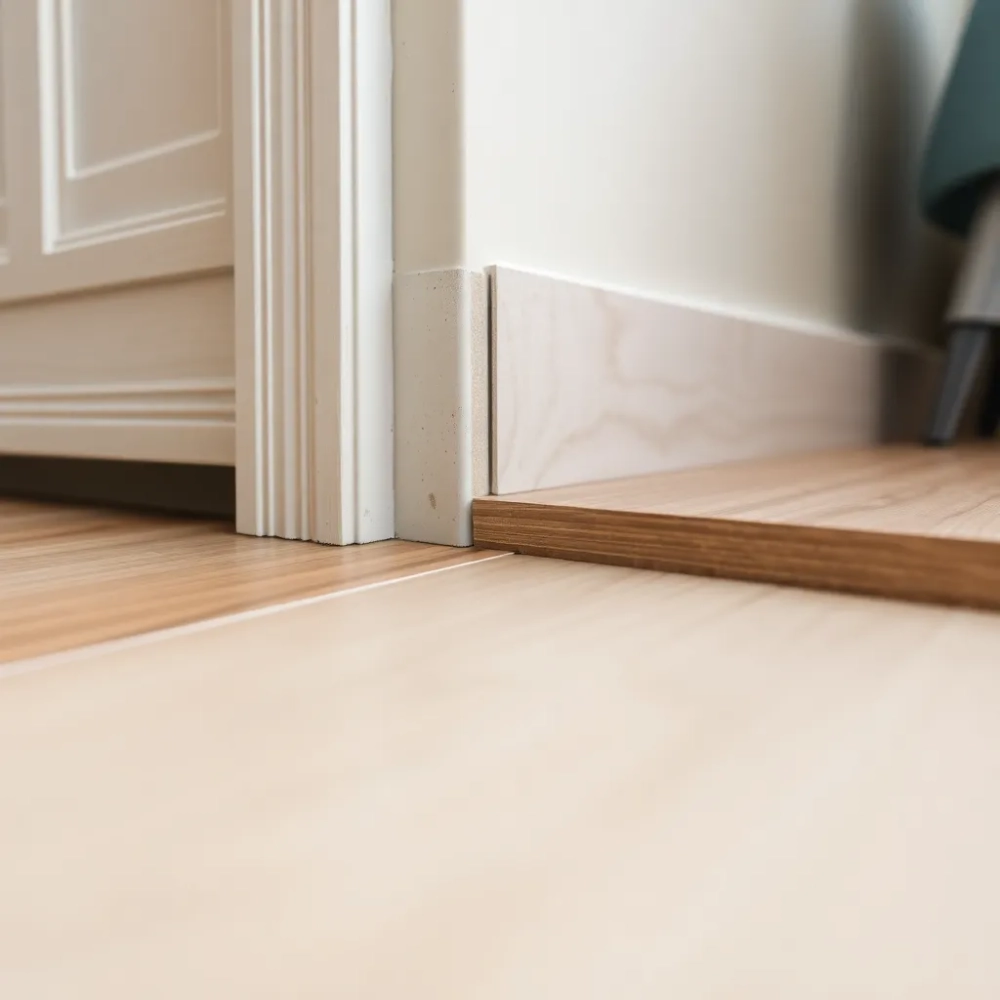
Aby lepiej zrozumieć, z jakimi realiami mamy do czynienia, przeanalizujmy kluczowe czynniki wpływające na powodzenie lub porażkę takiego przedsięwzięcia. Spojrzenie na potencjalne wskaźniki sukcesu, bazując na doświadczeniach i danych technicznych, daje nam solidny punkt wyjścia.
Czynnik | Optymalna Kondycja dla Sukcesu | Potencjalne Ryzyko Niepowodzenia |
---|---|---|
Stabilność Paneli (brak ugięć, luzów) | Panele całkowicie nieruchome, sztywno osadzone | Panele uginające się, luźne na łączeniach |
Wilgotność Paneli | Poniżej 10% | Powyżej 15% (ryzyko puchnięcia/kurczenia) |
Rodzaj Kleju/Przyczepność | Specjalistyczny, wysoko elastyczny, epoksydowy | Standardowy klej cementowy do płytek |
Przygotowanie Powierzchni Paneli (czyszczenie, gruntowanie) | Grunt epoksydowy, powierzchnia idealnie czysta | Brak gruntowania lub niewłaściwy produkt, kurz/brud |
Ruchy Termiczne Paneli | Minimalne (np. ogrzewanie podłogowe pod spodem wpływa na stabilność temperatury) | Znaczące wahania temperatury i wilgotności w pomieszczeniu |
Przedstawione dane jasno wskazują, że możliwość powodzenia nie jest zerowa, ale dramatycznie zależy od stanu wyjściowego podłogi panelowej i rygorystycznego przestrzegania specyficznych procedur oraz użycia dedykowanych materiałów. Kluczowe wydaje się potraktowanie paneli nie jako docelowego podłoża, lecz jako warstwy pośredniej, którą trzeba "uciszyć" i przygotować na zupełnie inne obciążenia i siły, niż te do których została pierwotnie zaprojektowana. Zignorowanie któregokolwiek z tych punktów to prosta droga do katastrofy i zmarnowanych pieniędzy. Mówimy tu o wymagającej, lecz w odpowiednich warunkach, wykonalnej operacji.
Główne wyzwania: Dlaczego kładzenie płytek na panelach jest trudne?
Decydując się na położenie płytek ceramicznych na istniejącej podłodze z paneli, stajemy w obliczu kilku poważnych wyzwań technicznych, które odróżniają to zadanie od tradycyjnego układania płytek na betonowym podłożu. Podstawowym problemem jest natura paneli, które – w przeciwieństwie do sztywnej wylewki – charakteryzują się ograniczoną stabilnością wymiarową i strukturalną.
Panele, zwłaszcza te starszego typu lub oparte na płycie HDF, są podatne na wahania wilgotności i temperatury. Powoduje to ich rozszerzanie się i kurczenie, a także niewielkie ruchy na łączeniach. Dla sztywno osadzonej płytki ceramicznej i spoiny cementowej, taki dynamiczny podkład to wyrok – prędzej czy później pojawią się pęknięcia i odspojenia.
Innym istotnym czynnikiem jest przyczepność. Standardowy klej do płytek ceramicznych jest projektowany do wiązania z materiałami mineralnymi, takimi jak beton czy zaprawy cementowe. Powierzchnia laminowanych paneli jest gładka i często pokryta warstwą ścieralną lub lakierem, co drastically zmniejsza adhezję.
Co więcej, obciążenie punktowe wynikające z codziennego użytkowania podłogi – jak ciężkie meble czy chodzenie w twardym obuwiu – inaczej rozkłada się na sztywnej wylewce niż na lekko uginającej się powierzchni paneli. Może to prowadzić do naprężeń pod płytkami, skutkując ich uszkodzeniem lub luzowaniem.
Niewłaściwe przygotowanie powierzchni panelowej to najczęstsza przyczyna niepowodzeń. Pozostawienie brudu, tłuszczu czy resztek wosku na panelach całkowicie uniemożliwi skuteczne związanie jakiegokolwiek materiału wyrównującego czy kleju. Pamiętajmy, że dobra przyczepność jest jak solidny fundament dla budynku.
Nie można również zapomnieć o wysokości podłogi. Układanie płytek na istniejących panelach nieuchronnie zwiększy poziom podłogi, co może stwarzać problemy przy drzwiach, progach i styku z innymi pomieszczeniami. Jest to aspekt, który bezwzględnie należy uwzględnić na etapie planowania, aby uniknąć później problemów z niedomykającymi się drzwiami czy nieestetycznymi różnicami poziomów.
Kwestia wilgotności jest również kluczowa. Panele same w sobie reagują na wilgoć, a wprowadzenie zapraw i klejów na bazie wody w trakcie procesu kładzenia płytek może dodatkowo destabilizować podkład. Należy zminimalizować ilość wody używanej w procesie i zapewnić odpowiednie wysychanie.
Niezrozumienie tych podstawowych różnic między podłożem panelowym a betonowym jest główną przyczyną, dla której próby położenia płytek na panelach często kończą się fiaskiem. Wymaga to zupełnie innego zestawu technik, materiałów i podejścia, które omówimy w kolejnych sekcjach.
Kolejnym subtelnym, ale istotnym wyzwaniem jest kwestia przenoszenia drgań. Panele laminowane, ze swoją konstrukcją opartą na systemie klikowym, mogą nieznacznie wibrować lub przenosić drgania w inny sposób niż stabilna wylewka cementowa. Te mikroruchy, choć niezauważalne gołym okiem w przypadku paneli, mogą być destrukcyjne dla kruchego spoiwa i sztywnych płytek ceramicznych.
Trwałość paneli jako podłoża również bywa problematyczna. Stare, wyeksploatowane panele, z uszkodzonymi zamkami, zdartą powierzchnią czy miejscowymi ugięciami, po prostu nie nadają się do dalszego wykorzystania jako baza pod nowe pokrycie podłogowe. Próba oszczędności w tym przypadku może kosztować znacznie więcej w przyszłości.
Rozkład obciążeń jest kolejnym aspektem. Ciężar płytek i kleju znacząco zwiększa masę podłogi, co może mieć znaczenie zwłaszcza w przypadku stropów o ograniczonej nośności. Choć rzadko jest to problem w standardowych mieszkaniach, warto to wziąć pod uwagę, zwłaszcza w starszych budynkach lub przy zastosowaniu bardzo grubych i ciężkich płytek.
Na koniec, pamiętajmy o estetyce i trwałości efektu końcowego. Niedostateczna wiedza i pośpiech w tym procesie niemal gwarantują niezadowalający wygląd – pęknięte spoiny, odpadające płytki, a w skrajnych przypadkach nawet konieczność demontażu całej nowej podłogi. Trwałość estetyczna nowej posadzki zależy bezpośrednio od pokonania tych wstępnych wyzwań.
Rozwiązanie tych problemów wymaga specjalistycznych materiałów i technik, o których szczegółowo opowiemy w następnych rozdziałach. Bez ich zastosowania, kładzenie płytek na panelach pozostaje ryzykownym, a często skazanym na porażkę eksperymentem.
Podejście do tego zadania powinno być analityczne i ostrożne, niczym praca sapera. Każdy krok, od oceny stanu paneli po wybór chemii budowlanej, ma kolosalne znaczenie. Bagatelizowanie tych wyzwań to proszenie się o kłopoty. Pomyślmy o tym jak o operacji na otwartym sercu – precyzja i wiedza są kluczowe.
Praktycznym przykładem błędu, często popełnianego przez osoby bez doświadczenia, jest zastosowanie zbyt grubej warstwy kleju. O ile na betonie klej może kompensować niewielkie nierówności, o tyle na ruchomych panelach może prowadzić do lokalnych naprężeń i pęknięć. Klej powinien działać głównie jako spoiwo, a nie jako masa wyrównująca.
Dodatkowym wyzwaniem jest różnorodność dostępnych na rynku paneli laminowanych. Każdy producent i każda linia produktów może charakteryzować się nieco inną budową, grubością warstwy wierzchniej, rodzajem zamków czy odpornością na wilgoć. Brak uniwersalnego standardu komplikuje wybór odpowiednich materiałów przygotowawczych i klejów.
Wiele osób ulega pokusie zastosowania "sprawdzonych" metod dla betonowego podłoża, co w przypadku paneli kończy się katastrofą. Historia remontów jest pełna takich smutnych przykładów, gdzie zamiast nowej podłogi, po kilku miesiącach trzeba było kuć i zrywać wszystko od nowa.
Rekomendowane jest przeprowadzenie prób na niewielkim, mniej widocznym fragmencie podłogi, aby sprawdzić reakcję paneli na gruntowanie i klejenie. Taki "test na małą skalę" może uchronić przed bolesnymi błędami w całej przestrzeni. Koszt próbki jest znikomy w porównaniu z kosztami generalnego remontu po nieudanej próbie.
Problem stanowi także brak naturalnej "oddychalności" paneli. Zamknięcie ich pod warstwą płytek i elastycznego kleju zmienia warunki wilgotnościowe pod powierzchnią. Może to wpłynąć na trwałość samego panela lub warstwy przygotowawczej.
Ostatecznie, decyzja o położeniu płytek na panelach powinna być poprzedzona gruntowną analizą stanu istniejącej podłogi i realną oceną własnych umiejętności. Czasem najtańszym i najbezpieczniejszym rozwiązaniem okazuje się po prostu usunięcie starych paneli.
Jeśli jednak panele są w doskonałym stanie, a specyficzne warunki remontowe (np. brak możliwości ingerencji w strop) wymuszają takie rozwiązanie, położenie płytek na panele jest technicznie możliwe, ale tylko i wyłącznie przy użyciu odpowiednich technologii i materiałów. To klucz do sukcesu.
Niezbędne kroki w przygotowaniu paneli pod płytki
Przystępując do tak nietypowego zadania, jakim jest położenie płytek na panelach, musimy podejść do etapu przygotowawczego z niemal chirurgiczną precyzją. To tutaj rozstrzyga się większość przyszłych sukcesów lub porażek. Pomińmy ten krok lub wykonajmy go niedbale, a nowa podłoga nie przetrwa próby czasu, tak jak niewłaściwie zaprawiony posiłek szybko ląduje w koszu.
Pierwszym, absolutnie fundamentalnym krokiem jest ocena stanu istniejących paneli. Czy są stabilne, czy nie uginają się pod ciężarem? Czy na łączeniach nie ma luzów lub uszkodzeń mechanicznych? Jeśli panele są pofałdowane, napuchnięte od wilgoci lub widocznie zniszczone, najlepiej po prostu je usunąć.
Następnie należy dokładnie oczyścić powierzchnię z kurzu, brudu, wosków, olejów i wszelkich innych substancji, które mogłyby zmniejszyć przyczepność. Czystość jest równie ważna, co dla chirurga przed operacją – każda drobina może zagrozić powodzeniu.
Po oczyszczeniu konieczne jest zastosowanie specjalistycznego środka gruntującego. Nie może być to zwykły grunt akrylowy do ścian. Potrzebujemy produktu, który zapewni doskonałą adhezję do gładkiej, laminowanej powierzchni paneli, tworząc jednocześnie barierę dla wilgoci z zapraw i zwiększając spójność podłoża. Najczęściej są to grunty epoksydowe lub specjalistyczne grunty adhezyjne na bazie żywic.
Kolejnym kluczowym etapem jest wyrównanie powierzchni i nadanie jej niezbędnej sztywności. Często stosuje się w tym celu samopoziomujące masy wyrównujące, które nakłada się na zagruntowane panele. Masa taka powinna charakteryzować się elastycznością i dobrą przyczepnością do podłoża, tworząc jednocześnie stabilną i równą warstwę.
Grubość warstwy wyrównującej powinna być dostosowana do zaleceń producenta chemii budowlanej, ale zazwyczaj wynosi od kilku do kilkunastu milimetrów. To właśnie ta warstwa, po związaniu, tworzy rzeczywiste podłoże dla płytek, redukując wpływ ruchów paneli pod spodem.
Po nałożeniu masy wyrównującej należy pozwolić jej dokładnie wyschnąć zgodnie z instrukcją producenta. Jest to proces, którego nie wolno przyspieszać. Wilgoć uwięziona pod nową warstwą może spowodować problemy w przyszłości.
W niektórych, bardziej wymagających przypadkach, stosuje się dodatkowe wzmocnienie, np. poprzez wklejenie siatki z włókna szklanego w masę wyrównującą lub klej. Zwiększa to odporność warstwy pod płytkami na naprężenia i ruchy podłoża.
Krawędzie podłogi wzdłuż ścian należy zabezpieczyć dylatacją. Panele pod spodem wciąż mogą podlegać niewielkim ruchom, a nowa podłoga z płytek musi mieć przestrzeń do minimalnej ekspansji. Zastosowanie taśmy dylatacyjnej na całym obwodzie pomieszczenia jest standardem.
Niezwykle ważne jest, aby każdy z tych kroków był wykonany starannie i z użyciem materiałów przeznaczonych do tego celu. Ignorowanie specyfikacji produktów lub próba zastąpienia specjalistycznej chemii standardowymi rozwiązaniami to prosta droga do zmarnowania czasu i pieniędzy.
Podczas pracy z gruntami i masami na bazie żywic, należy bezwzględnie przestrzegać zasad bezpieczeństwa – zapewnić dobrą wentylację pomieszczenia i stosować odpowiednie środki ochrony osobistej. Te produkty mogą być bardziej agresywne niż tradycyjne materiały budowlane.
Koszt materiałów przygotowawczych może być znaczący – szacunkowo od 50 do nawet 150 zł/m² w zależności od systemu i grubości warstwy wyrównującej. Nie jest to tania opcja, ale jest inwestycja w stabilność i trwałość całej konstrukcji podłogowej.
Dobrym zwyczajem jest skonsultowanie wyboru konkretnych produktów z doradcą technicznym producenta chemii budowlanej. Posiadają oni często gotowe systemy przeznaczone właśnie do kładzenia okładzin na podłożach nietypowych, w tym na drewnianych podłogach czy panelach.
Po zakończeniu wszystkich etapów przygotowawczych powinniśmy uzyskać idealnie czyste, równe, sztywne i dobrze związane z panelami podłoże, gotowe do przyjęcia warstwy kleju i płytek. Tylko takie podłoże gwarantuje, że nasza nowa podłoga ceramiczna przetrwa lata użytkowania.
Pamiętajmy, że czas potrzebny na wykonanie tych prac, włączając czasy schnięcia, może wynosić kilka dni. To nie jest remont "na szybko". Cierpliwość jest cnotą, która popłaca w tym przypadku.
Sumienne przygotowanie to połowa sukcesu. To etap, w którym eliminujemy główne zagrożenia związane z niestabilnością paneli i brakiem przyczepności. Bez tego nawet najlepsze płytki i najdroższy klej nie spełnią swojej funkcji.
Zapewnijmy sobie czas, odpowiednie materiały i precyzję wykonania. Stworzenie stabilnej bazy pod płytki na panelach jest realne, ale wymaga profesjonalnego podejścia do przygotowania podłoża.
Ten etap bywa najbardziej niedoceniany, a jego zaniedbanie skutkuje najpoważniejszymi konsekwencjami. Porównując do remontu samochodu – jeśli silnik nie jest właściwie przygotowany, to nawet najnowsze opony i karoseria nie uratują go przed awarią. Tutaj podłoże to "silnik" naszej nowej podłogi.
Niewłaściwe przygotowanie to jak budowa domu na ruchomych piaskach. Prędzej czy później konstrukcja zacznie pękać i osiadać. Uniknijmy tego scenariusza przez pedantyczne podejście do przygotowania paneli.
Dostępne na rynku systemy renowacyjne oferują kompleksowe rozwiązania – od gruntów, przez masy wyrównujące, aż po kleje dedykowane do takich zastosowań. Korzystanie z produktów jednego systemu daje największą gwarancję kompatybilności i trwałości.
Jakich materiałów użyć, kładąc płytki na panelach?
Wybór odpowiednich materiałów to kolejny newralgiczny punkt podczas układania płytek na panelach. Nie możemy sięgnąć po standardowe produkty, które sprawdzają się na betonowej wylewce. Potrzebna jest specjalistyczna chemia budowlana, która sprosta wyzwaniom związanym z elastycznym i niestabilnym podłożem. Użycie niewłaściwych materiałów jest jak próba gaszenia pożaru benzyną – pogarszamy sytuację.
Fundamentalną rolę odgrywa gruntowanie powierzchni panelowej. Jak już wspomniano, tradycyjne grunty nie zapewnią odpowiedniej przyczepności do gładkiej, nienasiąkliwej powierzchni paneli. Konieczne jest zastosowanie gruntów adhezyjnych, najczęściej na bazie żywic epoksydowych lub poliuretanowych. Koszt takiego gruntu to zazwyczaj od 30 do 80 zł/litr, a wydajność to ok. 0,1-0,2 l/m², co daje ok. 3-16 zł/m² za samo gruntowanie.
Następnym kluczowym materiałem jest masa wyrównująca lub szpachlowa. Musi ona być elastyczna, szybkowiążąca i charakteryzować się doskonałą przyczepnością do zagruntowanych paneli. Na rynku dostępne są specjalne masy renowacyjne przeznaczone do układania na drewnianych lub panelowych podłożach. Cena za 25 kg worek może wynosić od 80 do nawet 250 zł, a zużycie to zazwyczaj ok. 1,5-2 kg/m² na 1 mm grubości. Przy minimalnej zalecanej grubości kilku milimetrów, koszt materiału wyrównującego to znaczący element budżetu.
Absolutnie krytycznym elementem jest klej do płytek. Zapomnijmy o standardowych klejach cementowych (typu C1, C2). Potrzebujemy kleju o wysokiej elastyczności, zdolnego do przenoszenia naprężeń i ruchów podłoża. Idealnie sprawdzają się kleje klasy C2 S1 lub C2 S2, a w niektórych przypadkach rekomendowane są kleje epoksydowe lub poliuretanowe. Kleje elastyczne S1 kosztują ok. 60-150 zł za 25 kg worek, a kleje S2 czy epoksydowe od 200 zł wzwyż. Zużycie kleju to typowo ok. 3-5 kg/m², co daje koszt 7-30 zł/m² w zależności od typu i grubości warstwy.
Spoina do płytek również powinna być elastyczna, aby absorbować minimalne ruchy. Elastyczne fugi cementowe lub fugi epoksydowe będą najlepszym wyborem. Koszt fugi to od 20 do 100 zł za opakowanie, zużycie zależy od rozmiaru płytki i szerokości spoiny, ale jest to relatywnie mniejszy koszt jednostkowy.
Do uszczelnienia narożników, styków podłogi ze ścianami i wokół sanitariatów, niezbędny jest elastyczny silikon sanitarny lub poliuretanowy uszczelniacz. Koszt to ok. 15-40 zł za tubę, potrzebne jest zazwyczaj kilka tub na przeciętne pomieszczenie.
W przypadku systemów renowacyjnych, producenci często proponują kompletne pakiety materiałów: grunt, masa wyrównująca, klej, a czasem i taśma zbrojąca. Korzystanie z produktów jednego systemu minimalizuje ryzyko niekompatybilności materiałów i zapewnia największą gwarancję producenta.
Nie zapomnijmy o narzędziach – pacy zębatej o odpowiednim rozmiarze zębów, mieszadle mechanicznym do zapraw, wiertarce z mieszadłem, kuwecie na klej, gąbce do czyszczenia płytek, pace do fugowania, a także sprzęcie do cięcia płytek (gilotyna, piła diamentowa). Koszt narzędzi jednorazowych lub wynajmu sprzętu to również pozycja w budżecie.
Podsumowując koszty materiałów (bez kosztów płytek), szacunkowy koszt materiałów na 1 m² może wahać się od 70 zł (przy najprostszych systemach renowacyjnych i minimalnej warstwie wyrównującej) do nawet 200 zł i więcej (przy zastosowaniu specjalistycznych mas grubowarstwowych lub klejów epoksydowych). Przykładowy kosztorys materiałów na 10 m² może wyglądać tak:
Należy pamiętać, że powyższe dane są tylko szacunkowe i rzeczywiste koszty mogą się różnić w zależności od cen producentów, zużycia i warunków na budowie. Zawsze warto doliczyć ok. 10-15% na zapas materiału.
Płytki ceramiczne same w sobie to kolejny koszt, który całkowicie zależy od naszych upodobań – od kilkudziesięciu do kilkuset złotych za metr kwadratowy. Warto jednak pamiętać, że nawet najpiękniejsze i najdroższe płytki położone na źle przygotowanym podłożu szybko stracą swój urok.
Podsumowując, kluczem jest wybór systemowych materiałów renomowanych producentów, które są dedykowane do tego typu zastosowań. To nie jest miejsce na oszczędności czy eksperymenty z niesprawdzonymi produktami. Inwestycja w wysokiej jakości chemię budowlaną minimalizuje ryzyko awarii w przyszłości i gwarantuje długotrwały efekt.
Proces układania płytek na panelach – krok po kroku
Gdy etap przygotowania podłoża został przeprowadzony z należytą starannością – panele są oczyszczone, zagruntowane, a warstwa wyrównująca osiągnęła pełną twardość i jest idealnie równa – możemy przystąpić do właściwego układania płytek. Ten etap wymaga równie dużej precyzji jak przygotowanie, a każdy detal ma znaczenie dla ostatecznego wyglądu i trwałości podłogi.
Pierwszym krokiem jest rozplanowanie układu płytek. Należy określić, od którego miejsca zacząć, aby zminimalizować ilość cięć i ukryć je w mniej widocznych miejscach (np. przy ścianach). Standardowo rozpoczyna się od środka pomieszczenia lub od ściany z drzwiami, ale w tym przypadku, gdy podłoże ma swoją specyfikę, dokładne rozmierzenie jest kluczowe, aby unikać wąskich "odpadów" na końcu rzędów.
Klej należy nanosić na podłoże pacą zębatą, używając zębów o rozmiarze odpowiednim do rozmiaru płytek. Grubość warstwy kleju powinna być zgodna z zaleceniami producenta, zazwyczaj 3-5 mm. Należy nanosić klej tylko na taką powierzchnię, na której jesteśmy w stanie położyć płytki w ciągu czasu "otwartego" kleju (zanim zacznie wysychać).
Każdą płytkę należy docisnąć i delikatnie przesunąć w świeżym kleju, aby zapewnić pełne wypełnienie przestrzeni pod płytką (minimum 80% dla pomieszczeń suchych, 100% dla wilgotnych). Brak pełnego styku płytki z klejem prowadzi do pustek powietrznych, które osłabiają połączenie i zwiększają ryzyko pęknięć.
Między płytkami należy stosować krzyżyki dystansowe lub klipsy do poziomowania, aby uzyskać równe, docelowe spoiny. Ich szerokość zależy od rodzaju płytek i naszych preferencji, ale przy podłożu o podwyższonej elastyczności zaleca się spoiny o szerokości co najmniej 3-4 mm, co pozwoli na większą swobodę ruchów.
Regularnie sprawdzajmy poziom i równość układanych płytek za pomocą poziomicy. W razie potrzeby, dokonujmy korekt, zanim klej zacznie wiązać. Pamiętajmy, że raz położoną i związaną płytkę trudno jest poprawić bez uszkodzenia podłoża lub samej płytki.
Przy ścianach i przeszkodach płytki należy odpowiednio dociąć. Do cięcia prostych linii na płytkach ceramicznych i gresowych najlepiej użyć gilotyny ręcznej, natomiast do cięcia bardziej skomplikowanych kształtów czy otworów niezbędna będzie piła kątowa z tarczą diamentową (tzw. "fleksa") lub profesjonalna piła do glazury na mokro.
Na obwodzie pomieszczenia, przy styku płytek ze ścianą, należy bezwzględnie pozostawić szczelinę dylatacyjną o szerokości ok. 5-10 mm. Tej szczeliny nie wypełniamy klejem ani fugą cementową. Zostanie ona później wypełniona elastycznym materiałem (np. silikonem) lub zasłonięta listwą przypodłogową.
Po ułożeniu wszystkich płytek, zanim klej całkowicie zwiąże (czas ten podaje producent kleju, zazwyczaj od 12 do 48 godzin w zależności od warunków), należy delikatnie usunąć nadmiar kleju ze spoin i powierzchni płytek za pomocą wilgotnej gąbki.
Po całkowitym wyschnięciu kleju, można przystąpić do fugowania. Fugę nanosimy na czyste spoiny za pomocą gumowej pacy, wciskając ją dokładnie tak, aby całkowicie wypełnić przestrzeń między płytkami. Należy pracować sekcjami, a po lekkim związaniu fugi, usunąć jej nadmiar za pomocą wilgotnej gąbki, płucząc ją często w czystej wodzie.
Na koniec, po związaniu fugi, należy wykonać dylatacje obwodowe i wokół przeszkód stałych. Szczeliny te wypełniamy trwale elastycznym materiałem, np. silikonem sanitarnym w kolorze fugi. To jest absolutnie kluczowy krok, który zapobiega naprężeniom i pękaniu płytek w wyniku ruchów konstrukcji czy podłoża panelowego.
Czas potrzebny na ułożenie płytek na 1 m² jest bardzo zróżnicowany i zależy od wielkości płytek, stopnia skomplikowania wzoru, ilości cięć i naszego doświadczenia. Dla prostokątnych płytek o standardowym rozmiarze (np. 30x60 cm), można szacować od 1 do 3 godzin pracy fachowca na m². Przykładowy harmonogram dla 10 m² powierzchni, włączając czasy schnięcia, może wyglądać następująco:
Jest to praca wymagająca cierpliwości i dokładności. Pośpiech na którymkolwiek etapie – czy to przy przygotowaniu, czy przy samym układaniu – może zniweczyć cały wysiłek. Uczucie satysfakcji z idealnie położonej podłogi z płytek na nietypowym podłożu jest jednak warte tego wysiłku.
Warto również zaznaczyć, że warunki otoczenia, takie jak temperatura i wilgotność powietrza w pomieszczeniu, mają duży wpływ na czasy schnięcia i wiązania materiałów. Zawsze należy działać zgodnie z zaleceniami technicznymi producenta, które często zawierają wytyczne dotyczące minimalnej i maksymalnej temperatury pracy oraz wilgotności powietrza.
Kontrola jakości na każdym etapie procesu jest nieodzowna. Po ułożeniu kilku płytek, warto podnieść jedną z nich, aby sprawdzić, czy powierzchnia styku z klejem jest pełna i równomierna. Takie kontrole w trakcie pracy pozwalają na szybkie korygowanie błędów, zanim będzie za późno.
Pamiętajmy o właściwym doborze i użyciu narzędzi. Stępiona paca, niedokładne mieszadło czy niewłaściwa gilotyna do płytek mogą znacząco utrudnić pracę i wpłynąć na jej jakość. Warto zainwestować w dobrej jakości narzędzia lub je wynająć na czas remontu.
Na koniec, przed pełnym obciążeniem podłogi meblami, należy odczekać czas wskazany przez producenta kleju i fugi (zazwyczaj kilka dni do tygodnia) dla osiągnięcia pełnej wytrzymałości. Zbyt wczesne obciążenie może spowodować trwałe uszkodzenie lub poluzowanie płytek.
Podsumowując, proces układania płytek na panelach jest technicznie wykonalny, ale wymaga kompleksowego podejścia: gruntownego przygotowania, zastosowania odpowiednich materiałów systemowych i skrupulatnego przestrzegania etapów pracy. To przedsięwzięcie dla osób dokładnych i cierpliwych, które są gotowe poświęcić czas i uwagę każdemu szczegółowi.
Czy warto? To zależy od indywidualnej sytuacji i stanu paneli. Jeśli stare panele są w dobrej kondycji, a zrywanie ich jest wyjątkowo kłopotliwe, może to być opcja warta rozważenia. Ale tylko wtedy, gdy podejdziemy do niej z pełnym profesjonalizmem i bez kompromisów w kwestii materiałów i technik. Precyzja wykonania jest decydująca dla powodzenia.